Optical coatings are made through a precise and controlled process known as vacuum deposition, which involves creating a vacuum environment to deposit thin layers of material onto a substrate. This process ensures the formation of high-quality, multi-layered coatings with specific optical properties, such as antireflective (AR) coatings. The key steps include preparing the substrate, evaporating or sputtering the coating material, depositing it in a vacuum chamber, and cooling the coated substrate. The performance of these coatings is enhanced by varying the thickness and refractive indices of the layers. Below, the process is broken down into detailed steps and explanations.
Key Points Explained:
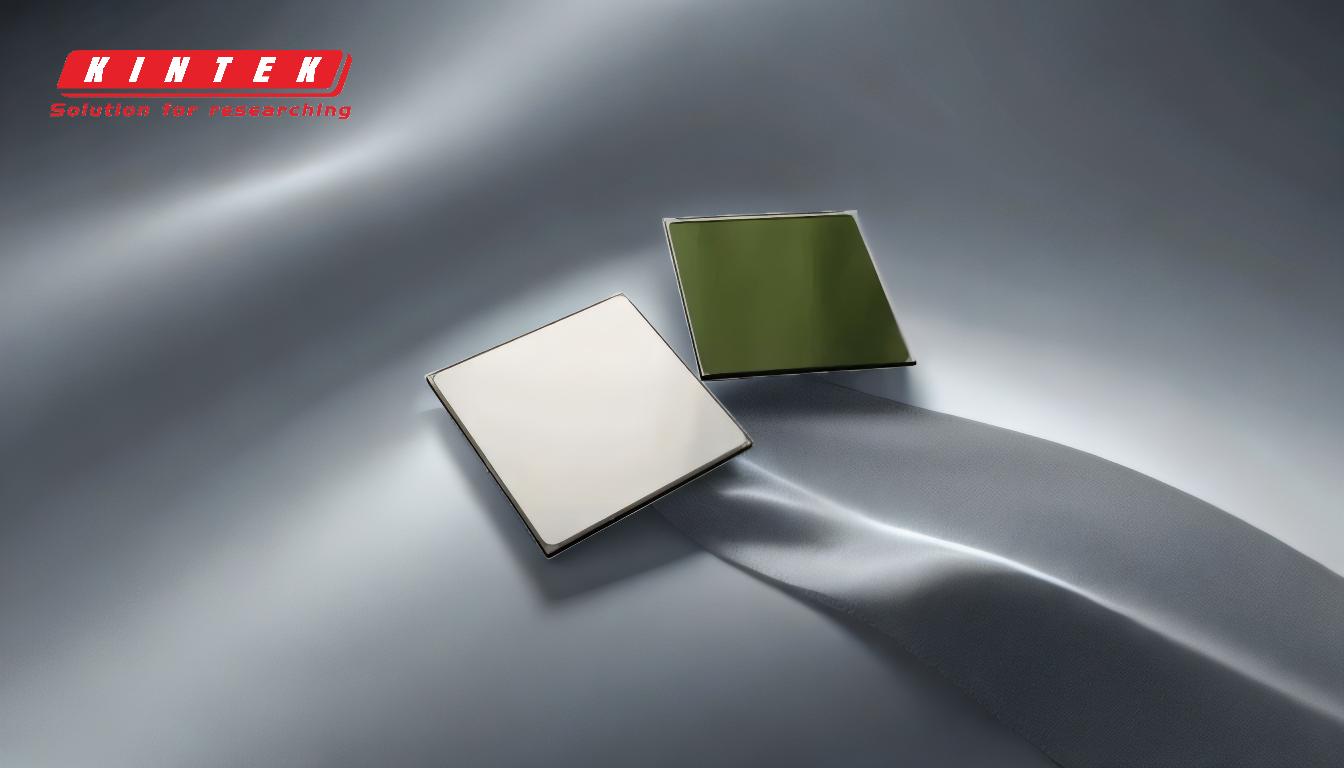
-
Cleaning and Preparing the Substrate
- Before the coating process begins, the substrate (e.g., glass or lens) must be thoroughly cleaned to remove any contaminants, such as dust, oils, or residues.
- Cleaning is typically done using abrasive liquids or specialized cleaning agents to ensure the surface is free of impurities that could interfere with the adhesion of the coating.
- A clean surface is critical for achieving uniform and defect-free coatings.
-
Creating a Vacuum Environment
- The substrate is placed inside a vacuum chamber, and air and gases are removed to create a high-vacuum environment.
- This step is essential because air molecules and gases can interfere with the deposition process, leading to imperfections in the coating.
- A vacuum also prevents oxidation and contamination during the coating process.
-
Evaporating or Sputtering the Coating Material
- The coating material, which can be a metal, dielectric, or other specialized material, is prepared for deposition.
- Evaporation: The material is heated until it turns into a vapor. This is often done using an electron beam or resistive heating.
- Sputtering: The material is knocked off a target using high-energy ions (e.g., argon ions) in a process called sputtering.
- Both methods allow the material to be deposited as a thin, uniform layer on the substrate.
-
Depositing the Coating Material
- The vaporized or sputtered material is directed toward the substrate, where it condenses and forms a thin film.
- The thickness of the film is carefully controlled, often measured in nanometers, to achieve the desired optical properties.
- For multi-layer coatings, this process is repeated with different materials or varying thicknesses to create layers with specific refractive indices.
-
Cooling and Venting the Chamber
- After the deposition is complete, the chamber is allowed to cool down to room temperature.
- The vacuum is then released, and the chamber is vented to allow the coated substrate to be removed.
- Cooling ensures the coating adheres properly and prevents thermal stress on the substrate.
-
Enhancing Performance with Multi-Layer Coatings
- Optical coatings, such as AR coatings, often consist of multiple layers with varying thicknesses and refractive indices.
- These layers are designed to interact with light in specific ways, such as reducing reflections or enhancing transmission.
- The precise control of layer thickness and material properties is critical for achieving the desired optical performance.
-
Applications and Benefits
- Optical coatings are used in a wide range of applications, including eyeglasses, camera lenses, telescopes, and laser systems.
- They improve the performance of optical components by reducing glare, increasing light transmission, and protecting surfaces from scratches or environmental damage.
- The vacuum deposition process ensures high precision and repeatability, making it ideal for producing high-quality optical coatings.
By following these steps, manufacturers can create optical coatings with exceptional performance and durability, tailored to meet the specific needs of various applications.
Summary Table:
Step | Description |
---|---|
Cleaning and Preparing Substrate | Substrate is cleaned to remove contaminants for uniform coating adhesion. |
Creating a Vacuum Environment | Air and gases are removed to prevent imperfections and contamination. |
Evaporating or Sputtering Material | Coating material is heated or sputtered to form a vapor for deposition. |
Depositing the Coating Material | Material condenses on the substrate, forming a thin, controlled layer. |
Cooling and Venting the Chamber | Chamber is cooled and vented to ensure proper coating adhesion. |
Multi-Layer Coatings | Layers with varying thicknesses and refractive indices enhance optical performance. |
Applications and Benefits | Used in eyeglasses, lenses, and lasers to reduce glare and improve transmission. |
Discover how optical coatings can enhance your applications—contact our experts today!