Improving ball mill performance involves optimizing several key factors that influence grinding efficiency and productivity. These factors include the design and operation parameters of the mill, such as drum dimensions, rotation speed, ball filling ratio, and the properties of the material being ground. By carefully adjusting these variables, you can achieve better milling results, reduce energy consumption, and enhance the overall output of the grinding process. Below, we break down the essential aspects to consider for improving ball mill performance.
Key Points Explained:
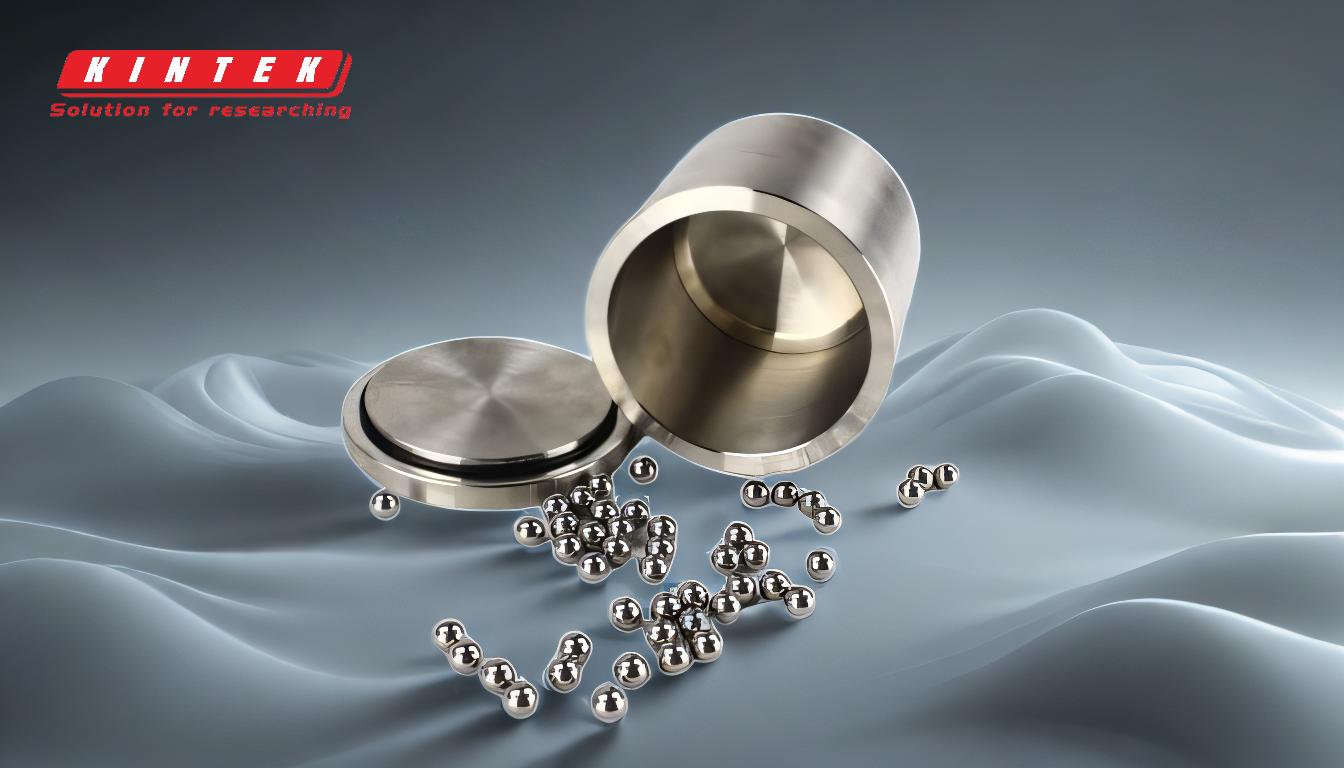
-
Optimize Drum Dimensions and L:D Ratio:
- The diameter and length of the drum significantly impact grinding efficiency. Research suggests that the optimal length-to-diameter (L:D) ratio for a ball mill is between 1.56 and 1.64. This ratio ensures a balance between material residence time and grinding intensity.
- A drum that is too long may lead to over-grinding, while a drum that is too short may not provide sufficient grinding time. Ensuring the correct L:D ratio helps maximize productivity.
-
Adjust Rotation Speed:
- The rotation speed of the mill affects the motion of the grinding balls and the material inside the drum. Too low a speed may result in insufficient grinding action, while too high a speed can cause the balls to centrifuge, reducing grinding efficiency.
- The critical speed (the speed at which the balls begin to centrifuge) should be calculated, and the mill should operate at a percentage (typically 65-75%) of this speed for optimal performance.
-
Optimize Ball Filling and Sizes:
- The size and number of grinding balls influence the grinding process. Larger balls are more effective for coarse grinding, while smaller balls are better for fine grinding. A mix of ball sizes can improve overall grinding efficiency.
- The filling ratio (the percentage of the mill volume filled with balls) should also be optimized. Overfilling can reduce grinding efficiency, while underfilling may lead to insufficient grinding action.
-
Control Material Properties and Feed Rate:
- The physical and chemical properties of the material being ground, such as hardness, density, and moisture content, affect grinding performance. Adjusting the feed rate and ensuring consistent material properties can improve results.
- A higher feed rate may reduce grinding time but can also lead to coarser output. Balancing feed rate with desired fineness is crucial.
-
Enhance Armor Surface Shape:
- The shape and design of the mill's internal armor (liners) can influence grinding efficiency. Smooth liners reduce wear but may not provide adequate lifting action for the balls, while ribbed or stepped liners can enhance grinding by improving ball movement.
- Regularly inspecting and maintaining liners ensures consistent performance and reduces downtime.
-
Monitor and Control Milling Fineness:
- The desired fineness of the ground product should be carefully controlled. Over-grinding can waste energy and reduce throughput, while under-grinding may not meet product specifications.
- Adjusting parameters such as rotation speed, ball size, and residence time can help achieve the desired fineness.
-
Ensure Timely Removal of Ground Product:
- Efficient removal of the ground product from the mill prevents over-grinding and ensures a steady flow of material. This can be achieved through proper design of discharge mechanisms and regular monitoring of the grinding process.
- Clogging or inefficient discharge can lead to reduced throughput and increased energy consumption.
-
Regular Maintenance and Inspection:
- Regular maintenance of the mill, including checking for wear on liners and balls, ensures consistent performance. Worn components should be replaced promptly to avoid inefficiencies.
- Monitoring vibration, temperature, and other operational parameters can help identify potential issues before they affect performance.
By systematically addressing these factors, you can significantly improve the performance of your ball mill. Each parameter should be carefully evaluated and adjusted based on the specific requirements of your grinding process and the properties of the material being processed. Regular monitoring and optimization will help maintain high productivity and efficiency over time.
Summary Table:
Key Factor | Optimization Tips |
---|---|
Drum Dimensions & L:D Ratio | Maintain L:D ratio between 1.56 and 1.64 for balanced grinding efficiency. |
Rotation Speed | Operate at 65-75% of critical speed to avoid ball centrifuging. |
Ball Filling & Sizes | Use a mix of ball sizes; optimize filling ratio to avoid over/underfilling. |
Material Properties & Feed Rate | Adjust feed rate based on material hardness, density, and desired fineness. |
Armor Surface Shape | Use ribbed or stepped liners for better ball movement and grinding efficiency. |
Milling Fineness | Monitor and adjust rotation speed, ball size, and residence time for desired fineness. |
Ground Product Removal | Ensure efficient discharge mechanisms to prevent clogging and over-grinding. |
Maintenance & Inspection | Regularly inspect liners, balls, and operational parameters for consistent performance. |
Ready to optimize your ball mill performance? Contact our experts today for tailored solutions!