Ball mills are widely used in various industries for grinding and mixing materials. Improving their efficiency can lead to significant cost savings, better product quality, and reduced energy consumption. Key strategies include optimizing operational parameters, maintaining equipment properly, and using advanced technologies. By focusing on factors such as rotational speed, grinding media, material feed rate, and liner design, operators can enhance the performance of ball mills. Additionally, adopting modern control systems and monitoring tools can further improve efficiency and reduce downtime.
Key Points Explained:
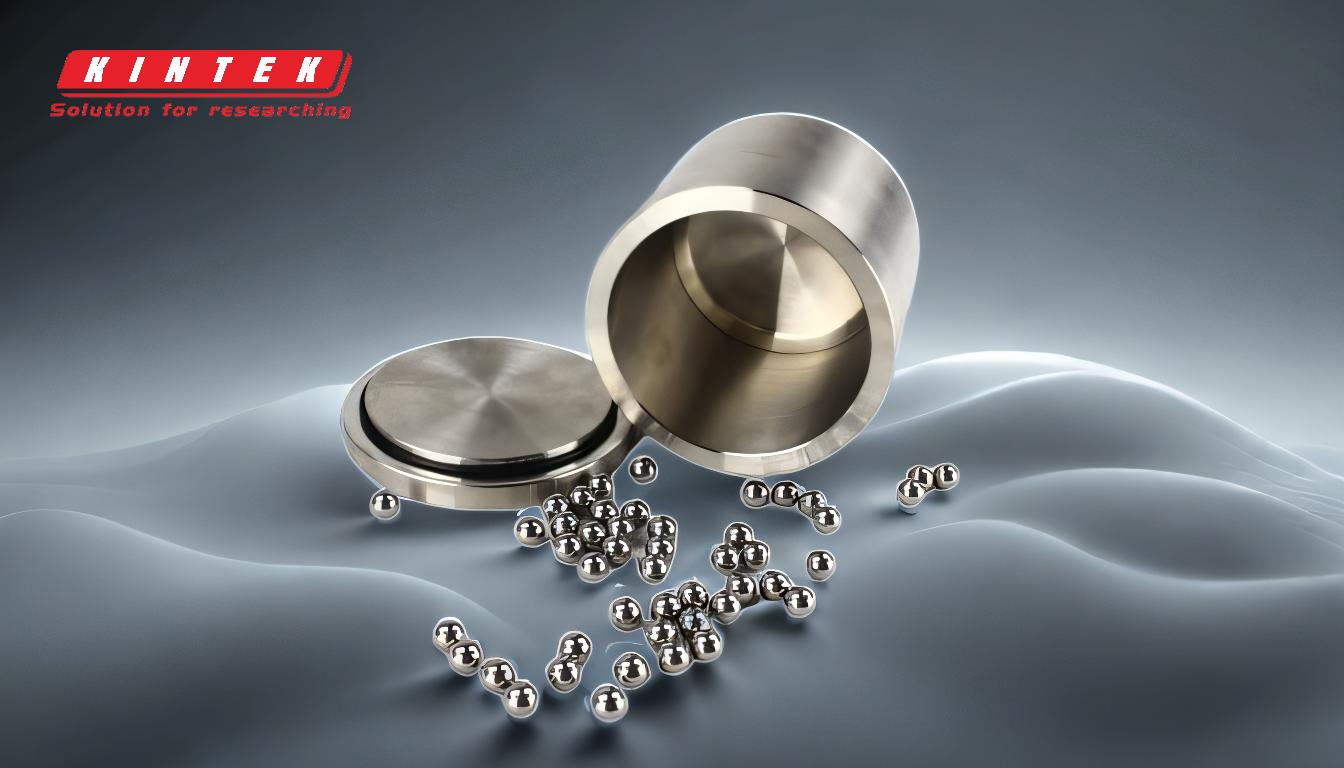
-
Optimize Rotational Speed:
- The rotational speed of the ball mill is a critical factor affecting its efficiency. If the speed is too low, the grinding media will not cascade effectively, leading to insufficient grinding. Conversely, if the speed is too high, the media may centrifuge, reducing grinding efficiency.
- Critical Speed: The optimal speed is typically 65-75% of the critical speed, which is the speed at which the grinding media begins to centrifuge. Operating within this range ensures that the media cascades and tumbles effectively, maximizing grinding efficiency.
-
Select Appropriate Grinding Media:
- The type, size, and density of the grinding media significantly impact the grinding process. Larger media are more effective for coarse grinding, while smaller media are better for fine grinding.
- Material: High-density materials like steel or ceramic are commonly used. The choice depends on the material being ground and the desired fineness.
- Size Distribution: A mix of different sizes can improve grinding efficiency by ensuring that both coarse and fine particles are effectively ground.
-
Control Material Feed Rate:
- The rate at which material is fed into the ball mill affects its efficiency. Overloading the mill can lead to inefficient grinding and increased wear, while underloading can result in excessive energy consumption.
- Optimal Feed Rate: Maintaining a consistent and optimal feed rate ensures that the mill operates at peak efficiency. This can be achieved through automated feeding systems that adjust the feed rate based on the mill's load.
-
Improve Liner Design:
- The liner inside the ball mill protects the shell from wear and helps lift the grinding media. The design of the liner can influence the grinding efficiency by affecting the movement of the media.
- Liner Profile: The shape and material of the liner should be chosen to maximize the lifting action of the media. Modern liners are designed to optimize the trajectory of the grinding media, improving grinding efficiency.
- Material: Liners made from wear-resistant materials like rubber or composite materials can reduce maintenance downtime and improve efficiency.
-
Maintain Proper Ball Charge:
- The amount and distribution of grinding media (balls) in the mill are crucial for efficient grinding. An insufficient ball charge will lead to poor grinding, while an excessive charge can cause energy wastage.
- Ball Charge Level: Regularly check and maintain the ball charge level to ensure it is within the recommended range. This can be done by periodically adding new balls to compensate for wear.
- Ball Size Distribution: A balanced mix of ball sizes ensures that both coarse and fine particles are effectively ground.
-
Use Advanced Control Systems:
- Modern control systems can monitor and adjust the operational parameters of the ball mill in real-time, ensuring optimal performance.
- Automation: Automated systems can adjust the feed rate, rotational speed, and other parameters based on real-time data, improving efficiency and reducing human error.
- Monitoring: Advanced sensors and monitoring tools can provide valuable data on the mill's performance, allowing operators to make informed decisions and prevent potential issues.
-
Reduce Energy Consumption:
- Energy efficiency is a key consideration in improving ball mill performance. Reducing energy consumption not only lowers operational costs but also minimizes environmental impact.
- Variable Speed Drives: Using variable speed drives allows the mill to operate at the optimal speed for different grinding tasks, reducing energy consumption.
- Energy Recovery Systems: Implementing energy recovery systems can capture and reuse energy that would otherwise be lost, further improving efficiency.
-
Regular Maintenance and Inspection:
- Regular maintenance and inspection are essential for keeping the ball mill in optimal condition. Neglecting maintenance can lead to increased wear, reduced efficiency, and costly downtime.
- Scheduled Maintenance: Implement a scheduled maintenance program to regularly inspect and replace worn parts, such as liners and grinding media.
- Condition Monitoring: Use condition monitoring tools to detect early signs of wear or malfunction, allowing for timely intervention and preventing major issues.
-
Optimize Material Properties:
- The properties of the material being ground, such as hardness, moisture content, and particle size distribution, can affect the efficiency of the ball mill.
- Moisture Control: Excessive moisture can lead to clogging and reduced grinding efficiency. Proper drying or pre-treatment of the material can help maintain optimal moisture levels.
- Particle Size: Pre-crushing the material to a smaller size before feeding it into the ball mill can improve grinding efficiency and reduce energy consumption.
-
Adopt Advanced Grinding Technologies:
- New grinding technologies, such as high-pressure grinding rolls (HPGR) or stirred mills, can be used in conjunction with ball mills to improve overall efficiency.
- Hybrid Systems: Combining different grinding technologies can optimize the grinding process, reducing energy consumption and improving product quality.
- Innovative Designs: Exploring innovative mill designs, such as vertical roller mills or horizontal ball mills, can offer new ways to improve efficiency and performance.
By focusing on these key areas, operators can significantly improve the efficiency of ball mills, leading to better performance, reduced energy consumption, and lower operational costs.
Summary Table:
Key Strategy | Details |
---|---|
Optimize Rotational Speed | Operate at 65-75% of critical speed for effective cascading and tumbling. |
Select Grinding Media | Use high-density materials (steel/ceramic) and mix sizes for better grinding. |
Control Material Feed Rate | Maintain consistent feed rates to avoid overloading or underloading. |
Improve Liner Design | Use wear-resistant materials and optimal profiles to enhance media movement. |
Maintain Ball Charge | Regularly check and adjust ball charge levels and size distribution. |
Use Advanced Control Systems | Automate and monitor operations for real-time adjustments and efficiency. |
Reduce Energy Consumption | Implement variable speed drives and energy recovery systems. |
Regular Maintenance | Schedule inspections and use condition monitoring to prevent downtime. |
Optimize Material Properties | Control moisture and pre-crush materials for better grinding efficiency. |
Adopt Advanced Technologies | Combine ball mills with HPGR or stirred mills for hybrid efficiency gains. |
Ready to optimize your ball mill efficiency? Contact us today for expert guidance and solutions!