A ball mill reduces the size of materials through a combination of mechanical forces, including impact, extrusion, and friction. The process involves placing materials and grinding balls inside a rotating cylinder. As the cylinder rotates, the balls collide with the material and each other, breaking down the material into smaller particles. The efficiency of this process depends on achieving the critical speed, where the balls rotate along the inner walls of the cylinder, maximizing grinding action. The size reduction is achieved through repeated collisions and grinding actions, with larger balls breaking down coarse materials and smaller balls refining the particles further. This method is widely used in industries for grinding and mixing materials to achieve fine, uniform particle sizes.
Key Points Explained:
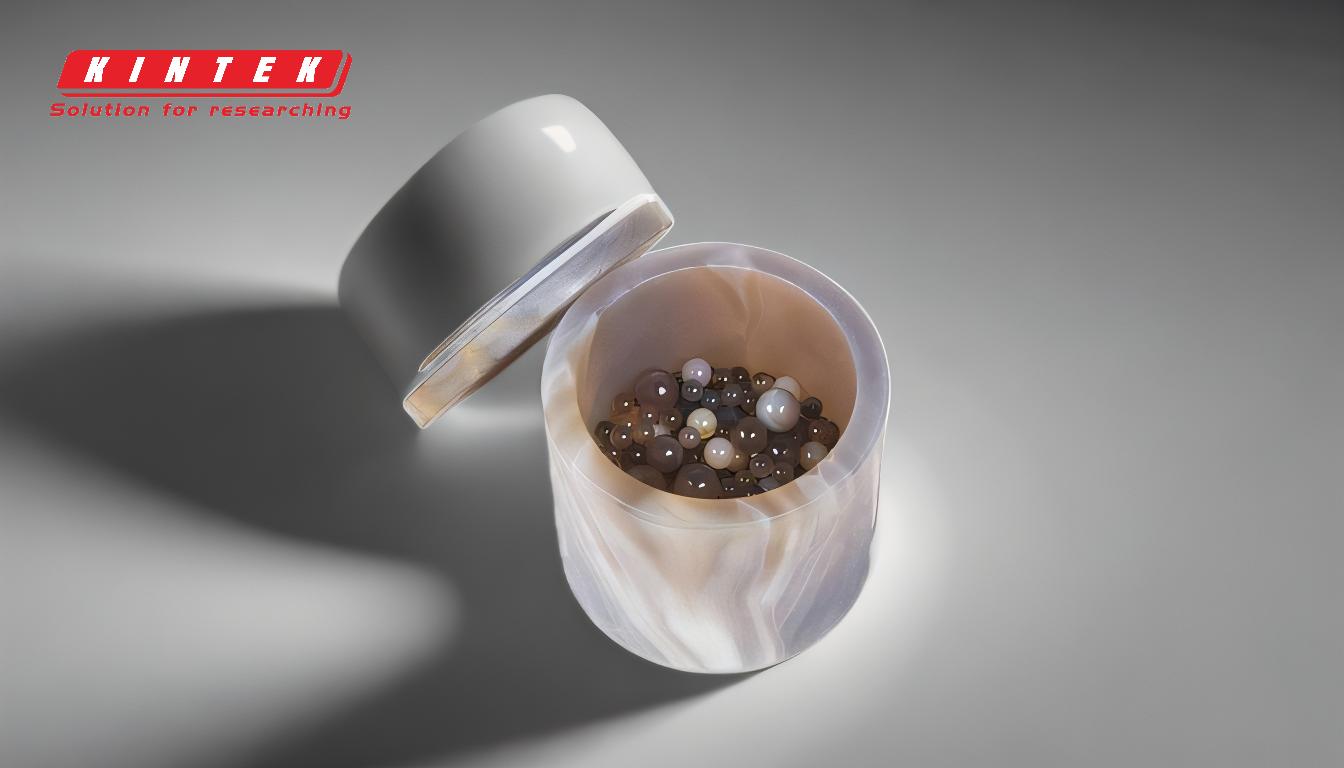
-
Mechanism of Size Reduction:
- Impact: The primary mechanism in a ball mill is the impact of grinding balls on the material. As the balls collide with the material, they break it down into smaller particles.
- Extrusion: The material is also subjected to extrusion forces as it is compressed between the balls and the walls of the cylinder.
- Friction: Friction between the balls and the material further aids in grinding, especially for finer particles.
-
Role of Grinding Balls:
- Large Balls: Larger balls are effective at breaking down coarse materials due to their greater mass and impact force.
- Small Balls: Smaller balls are used to reduce void spaces and refine the material into finer particles, ensuring a more uniform final product.
-
Critical Speed:
- Definition: Critical speed is the rotational speed at which the balls inside the mill begin to rotate along the inner walls of the cylinder.
- Importance: Achieving critical speed is crucial for effective grinding, as it ensures that the balls are lifted to a height where they can fall and impact the material with sufficient force.
-
Operational Steps:
- Loading: Materials and a fixed number of grinding balls are loaded into the cylinder.
- Rotation: The cylinder is rotated, either on a vertical or horizontal axis, at a speed that achieves critical speed.
- Adjustment: The speed can be adjusted as needed to optimize the grinding process.
- Completion: Once the desired particle size is achieved, the machine is stopped, and the materials are removed.
-
Types of Ball Mills:
- Tumbling Ball Mills: These are the most common type, where the cylinder rotates along a longitudinal axis, causing the balls to tumble and grind the material.
- Pebble Mills: Similar to tumbling ball mills but use pebbles as the grinding medium instead of metal balls.
-
Applications:
- Industrial Use: Ball mills are widely used in industries such as mining, ceramics, and pharmaceuticals for grinding and mixing materials.
- Laboratory Use: They are also used in laboratories for sample preparation and research purposes.
-
Advantages:
- Versatility: Ball mills can grind a wide variety of materials, from soft to very hard.
- Efficiency: They are highly efficient in reducing particle size and achieving a uniform product.
- Scalability: Ball mills can be used for both small-scale laboratory experiments and large-scale industrial production.
-
Considerations for Purchasers:
- Material Compatibility: Ensure the ball mill is compatible with the materials to be ground.
- Size and Capacity: Choose a ball mill with the appropriate size and capacity for the intended use.
- Speed Control: Opt for a ball mill with adjustable speed settings to achieve optimal grinding conditions.
- Maintenance: Consider the ease of maintenance and availability of spare parts.
By understanding these key points, purchasers can make informed decisions when selecting a ball mill for their specific needs, ensuring efficient and effective size reduction of materials.
Summary Table:
Key Aspect | Details |
---|---|
Mechanism | Impact, extrusion, and friction break down materials into smaller particles. |
Grinding Balls | Large balls for coarse materials; small balls for finer particles. |
Critical Speed | Optimal rotational speed for maximum grinding efficiency. |
Applications | Mining, ceramics, pharmaceuticals, and laboratory research. |
Advantages | Versatile, efficient, and scalable for various industries. |
Purchasing Tips | Consider material compatibility, size, speed control, and maintenance. |
Ready to optimize your material grinding process? Contact us today to find the perfect ball mill for your needs!