Heating elements can stop working due to a variety of reasons, ranging from physical degradation to operational issues. The primary causes include the formation of hot spots, oxidation due to intermittent operation, embrittlement from grain growth, and contamination or corrosion. Additionally, electrical issues such as tripped breakers, blown fuses, or defective switches can prevent power from reaching the heating element, rendering it non-functional. Understanding these failure mechanisms is crucial for maintaining the longevity and efficiency of heating elements in various applications.
Key Points Explained:
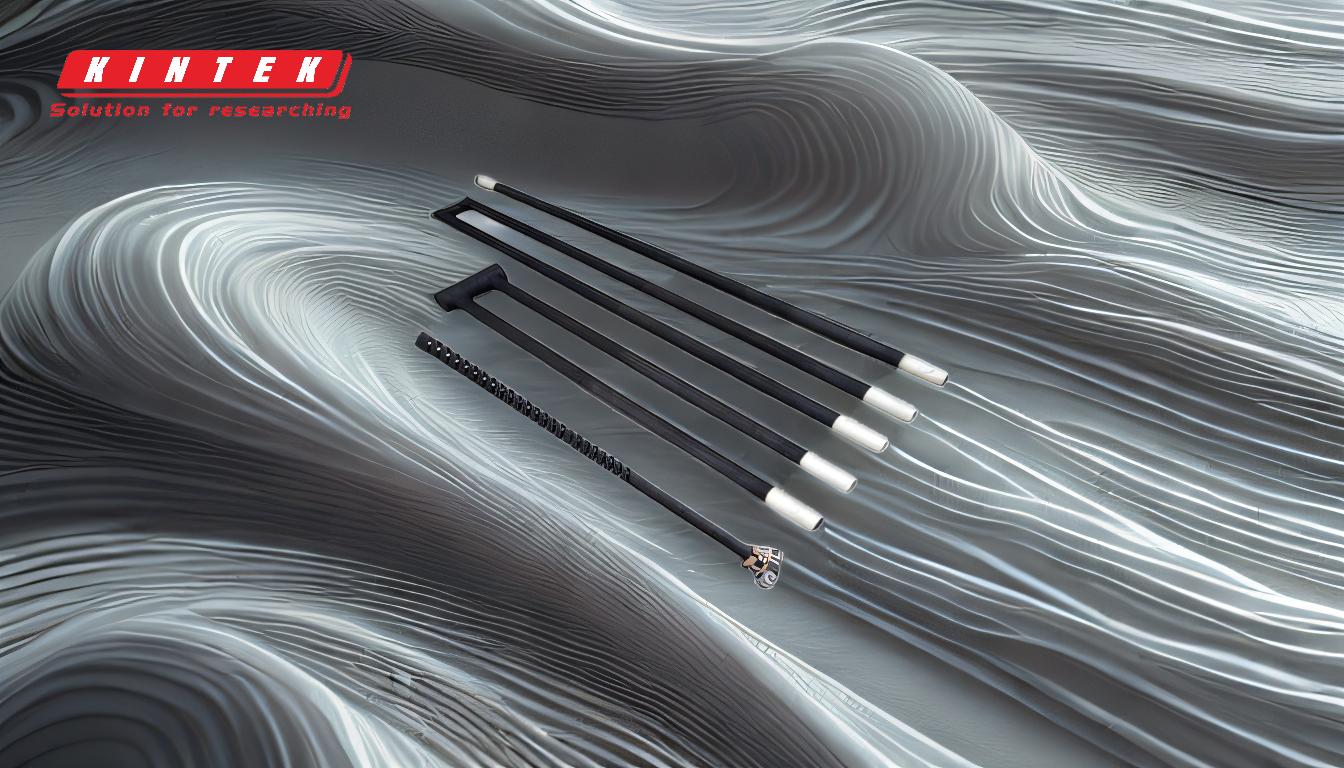
-
Formation of Hot Spots
- Description: Hot spots occur when certain areas of the heating element become significantly hotter than the rest. This can be due to high local oxidation or shielding by supports.
- Impact: These localized high temperatures can lead to accelerated degradation and eventual failure of the heating element.
- Prevention: Ensuring uniform heating and proper support placement can help mitigate the formation of hot spots.
-
Oxidation and Intermittency of Operation
- Description: Frequent heating and cooling cycles cause the oxide layer on the heating element to crack and flake off, exposing fresh metal to further oxidation.
- Impact: This process weakens the element over time, leading to its failure.
- Prevention: Minimizing rapid temperature changes and using materials with better oxidation resistance can extend the element's lifespan.
-
Embrittlement Due to Grain Growth
- Description: Heating alloys, especially those containing iron, can form large, brittle grains at high temperatures.
- Impact: This embrittlement makes the element more susceptible to cracking and breaking under stress.
- Prevention: Using alloys designed to resist grain growth and maintaining optimal operating temperatures can help prevent embrittlement.
-
Contamination and Corrosion
- Description: Exposure to corrosive gases or fumes in the furnace environment can contaminate the heating elements, leading to dry corrosion.
- Impact: Contamination and corrosion degrade the material, reducing its effectiveness and leading to failure.
- Prevention: Implementing proper ventilation and using corrosion-resistant materials can protect the elements from contamination.
-
Electrical Issues
- Description: Power supply problems such as tripped breakers, blown fuses, or defective switches can prevent the heating element from receiving power.
- Impact: Without power, the heating element cannot function, regardless of its physical condition.
- Prevention: Regular maintenance checks on the electrical system and immediate replacement of faulty components can ensure consistent power supply.
By addressing these key points, users can better understand the potential failure modes of heating elements and take proactive measures to prevent them, ensuring reliable and efficient operation over the long term.
Summary Table:
Cause of Failure | Description | Impact | Prevention |
---|---|---|---|
Formation of Hot Spots | Localized high temperatures due to oxidation or shielding by supports. | Accelerated degradation and failure. | Ensure uniform heating and proper support placement. |
Oxidation | Frequent heating/cooling cycles crack the oxide layer, exposing fresh metal. | Weakens the element over time. | Minimize rapid temperature changes; use oxidation-resistant materials. |
Embrittlement | Large, brittle grains form in heating alloys at high temperatures. | Increased susceptibility to cracking and breaking. | Use grain growth-resistant alloys; maintain optimal operating temperatures. |
Contamination/Corrosion | Exposure to corrosive gases or fumes contaminates the element. | Material degradation and failure. | Implement proper ventilation; use corrosion-resistant materials. |
Electrical Issues | Tripped breakers, blown fuses, or defective switches prevent power supply. | Heating element cannot function without power. | Perform regular electrical system checks; replace faulty components promptly. |
Need help maintaining or replacing your heating elements? Contact our experts today for tailored solutions!