The speed of a ball mill is a critical factor in determining the efficiency and effectiveness of size reduction. At low speeds, the grinding balls slide or roll over each other, resulting in minimal grinding action. At high speeds, centrifugal force causes the balls to stick to the cylinder wall, preventing effective grinding. However, at an optimal or "normal" speed, the balls are lifted to the top of the mill and then cascade down, creating a powerful grinding action that maximizes size reduction. Other factors, such as ball size, grinding time, material hardness, and mill filling ratio, also play significant roles in the grinding process.
Key Points Explained:
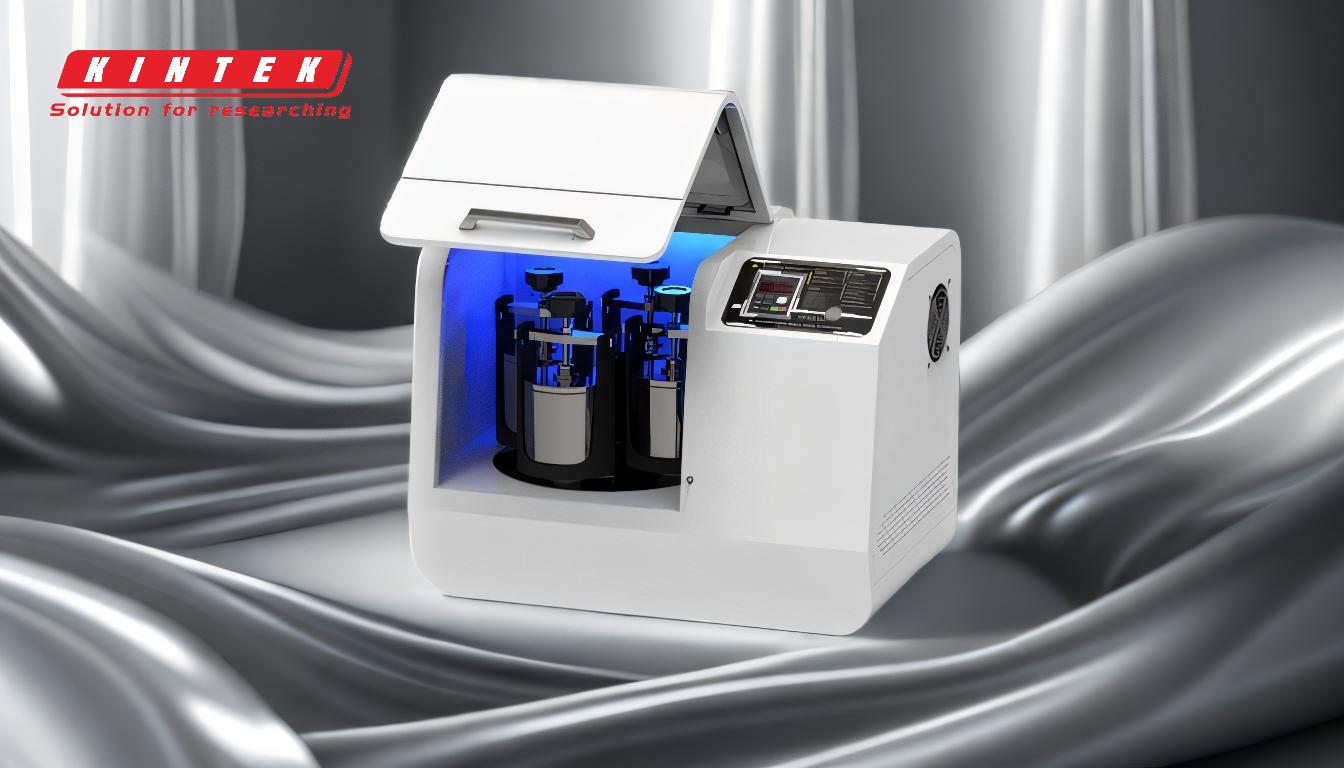
-
Impact of Ball Mill Speed on Size Reduction:
- Low Speed: At low rotational speeds, the grinding balls slide or roll over each other. This results in minimal impact and friction, leading to poor size reduction. The grinding action is inefficient because the balls do not gain enough momentum to break down the material effectively.
- High Speed: At high speeds, centrifugal force becomes dominant, causing the grinding balls to be thrown against the cylinder wall. This prevents the balls from cascading and effectively grinding the material. The grinding action is hindered because the balls are not free to move and impact the material.
- Normal Speed: At an optimal or "normal" speed, the balls are lifted to a certain height and then cascade down in a parabolic trajectory. This creates a combination of impact and friction forces that are ideal for size reduction. The cascading action ensures that the balls repeatedly strike and grind the material, leading to maximum size reduction.
-
Factors Influencing Size Reduction:
- Residence Time: The longer the material remains in the mill chamber, the more it is subjected to grinding forces. However, excessive residence time can lead to over-grinding or unnecessary energy consumption.
- Ball Size and Density: Smaller balls are more effective for grinding finer particles because they have a larger surface area relative to their mass, allowing for more contact points with the material. Denser balls can impart more energy upon impact, enhancing the grinding process.
- Material Hardness: Harder materials require more energy to break down, which may necessitate adjustments in mill speed, ball size, or grinding time to achieve the desired size reduction.
- Feed Rate and Level: The rate at which material is fed into the mill and the level of material in the vessel can affect the grinding efficiency. Overloading the mill can reduce the effectiveness of the grinding action, while underloading can lead to inefficient use of energy.
- Mill Filling Ratio: The percentage of the mill volume filled with grinding medium (balls) affects the grinding efficiency. An optimal filling ratio ensures that there is enough space for the balls to cascade and impact the material effectively.
-
Optimal Operating Conditions:
- Normal Speed: The optimal speed for a ball mill is typically around 65-75% of the critical speed, which is the speed at which the centrifugal force is just balanced by the gravitational force. At this speed, the balls cascade and impact the material most effectively.
- Ball Size and Grinding Time: Smaller balls and longer grinding times are generally required to produce finer particles. The size of the balls should be chosen based on the desired particle size and the hardness of the material being ground.
- Material Characteristics: Understanding the hardness, density, and other properties of the material being ground is crucial for optimizing the grinding process. Adjustments to mill speed, ball size, and grinding time may be necessary to achieve the desired size reduction.
-
Practical Considerations for Equipment Purchasers:
- Energy Efficiency: Operating the mill at the optimal speed and filling ratio can significantly reduce energy consumption. Purchasers should consider mills with variable speed controls to allow for adjustments based on the material being processed.
- Maintenance and Durability: High-speed operations can lead to increased wear and tear on the mill and grinding balls. Purchasers should consider the durability of the mill components and the availability of replacement parts.
- Scalability: The mill's design should allow for scalability, especially if the production requirements may increase in the future. This includes considering the mill's capacity, power requirements, and ease of operation.
In summary, the speed of a ball mill is a critical factor in achieving efficient size reduction. Operating the mill at the optimal speed ensures that the grinding balls cascade and impact the material effectively, leading to maximum size reduction. Other factors, such as ball size, grinding time, material hardness, and mill filling ratio, also play important roles in the grinding process. Equipment purchasers should consider these factors, along with energy efficiency, maintenance, and scalability, when selecting a ball mill for their specific needs.
Summary Table:
Factor | Impact on Size Reduction |
---|---|
Low Speed | Minimal grinding action; balls slide or roll, resulting in poor size reduction. |
High Speed | Centrifugal force causes balls to stick to the wall, hindering grinding. |
Normal Speed | Optimal cascading action maximizes size reduction through impact and friction. |
Ball Size | Smaller balls grind finer particles; denser balls impart more energy. |
Material Hardness | Harder materials require more energy and adjustments to mill speed or grinding time. |
Mill Filling Ratio | Optimal filling ensures space for cascading and effective grinding. |
Residence Time | Longer time increases grinding but may lead to over-grinding or energy waste. |
Ready to optimize your ball mill performance? Contact us today for expert advice and solutions!