Reactive sputtering is a specialized thin-film deposition technique where a reactive gas, such as oxygen or nitrogen, is introduced into a vacuum chamber containing a target material and an inert gas like argon. The reactive gas chemically interacts with the sputtered atoms from the target, forming compounds like oxides or nitrides, which are then deposited as thin films on a substrate. This process allows for precise control over film composition and properties, making it ideal for applications requiring specific functional characteristics, such as barrier layers or optical coatings. However, it requires careful management of parameters like gas flow rates and partial pressures to avoid issues like hysteresis and ensure optimal film quality.
Key Points Explained:
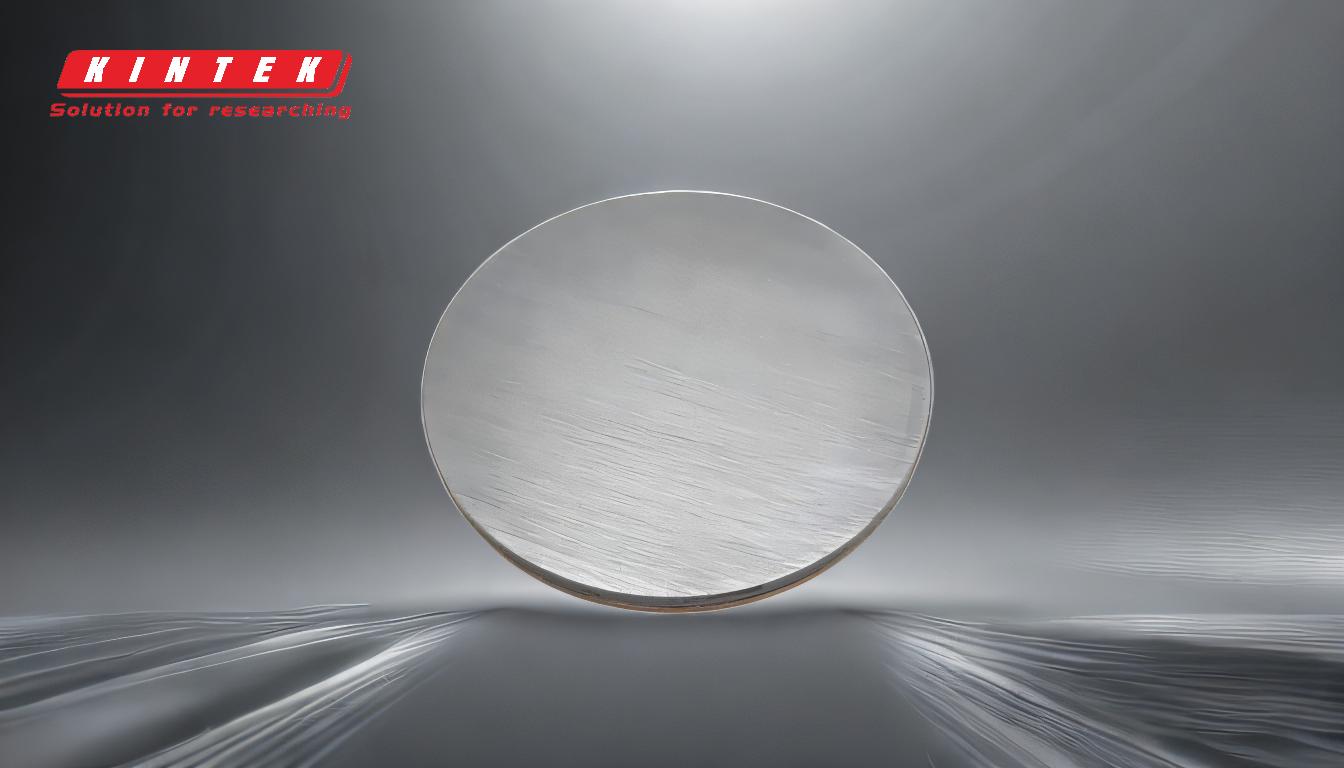
-
Basic Mechanism of Reactive Sputtering:
- Reactive sputtering involves introducing a reactive gas (e.g., oxygen, nitrogen) into a vacuum chamber alongside an inert gas (e.g., argon).
- The target material is bombarded with ions from the inert gas, causing atoms to be ejected (sputtered) from the target.
- These sputtered atoms then react with the reactive gas in the chamber, forming compounds such as oxides or nitrides.
- The resulting compound is deposited as a thin film on the substrate.
-
Role of Reactive and Inert Gases:
- Inert Gas (Argon): Provides the ions necessary to sputter the target material. Argon is commonly used because it is chemically inert and does not react with the target or substrate.
- Reactive Gas (Oxygen, Nitrogen): Chemically reacts with the sputtered target atoms to form compounds like titanium oxide (TiO₂) or titanium nitride (TiN).
- The ratio of inert to reactive gas is critical for controlling the stoichiometry and properties of the deposited film.
-
Chemical Reactions in the Chamber:
- The reactive gas becomes ionized in the plasma environment created by the inert gas.
- These ions react with the sputtered target atoms, forming molecular compounds.
- For example, sputtering silicon in the presence of oxygen produces silicon oxide (SiO₂), while sputtering titanium in the presence of nitrogen produces titanium nitride (TiN).
-
Control of Film Composition and Properties:
- The composition of the deposited film can be precisely controlled by adjusting the partial pressures of the reactive and inert gases.
- This control is essential for optimizing functional properties such as stress, refractive index, and electrical conductivity.
- The Berg Model is often used to predict the impact of reactive gas on target erosion and deposition rates, aiding in process optimization.
-
Challenges and Complexities:
- Hysteresis Behavior: The introduction of a reactive gas can lead to non-linear behavior in the deposition process, requiring careful control of parameters like gas flow rates and partial pressures.
- Target Poisoning: Excessive reactive gas can form a compound layer on the target surface, reducing sputtering efficiency. This is managed by balancing the reactive gas flow and maintaining a stable plasma.
- Process Stability: Achieving consistent film properties requires precise control over the reactive sputtering environment, including gas ratios, pressure, and power supply.
-
Applications of Reactive Sputtering:
- Barrier Layers: Reactive sputtering is used to deposit thin films that act as diffusion barriers in microelectronics, such as titanium nitride (TiN) layers in semiconductor devices.
- Optical Coatings: Films like silicon oxide (SiO₂) and titanium oxide (TiO₂) are used in optical applications due to their tunable refractive indices.
- Wear-Resistant Coatings: Titanium nitride (TiN) and similar compounds are applied to tools and components to enhance durability and resistance to wear.
-
Variants of Reactive Sputtering:
- DC Reactive Sputtering: Uses a direct current power supply to generate the plasma. It is simpler but can be prone to target poisoning.
- RF (Radio Frequency) Reactive Sputtering: Uses high-frequency alternating current, which is better suited for insulating materials and can reduce target poisoning effects.
-
Advantages Over Non-Reactive Sputtering:
- Enables the deposition of compound films with precise stoichiometry and tailored properties.
- Expands the range of materials that can be deposited, including oxides, nitrides, and carbides.
- Provides greater flexibility in tuning film characteristics for specific applications.
By understanding these key points, equipment and consumable purchasers can better appreciate the technical nuances of reactive sputtering and make informed decisions about its use in their processes.
Summary Table:
Key Aspect | Description |
---|---|
Mechanism | Reactive gas reacts with sputtered target atoms to form compounds (e.g., oxides, nitrides). |
Gases Used | Inert gas (argon) for sputtering; reactive gas (oxygen, nitrogen) for compound formation. |
Applications | Barrier layers, optical coatings, wear-resistant coatings. |
Challenges | Hysteresis, target poisoning, process stability. |
Advantages | Precise film composition, tailored properties, expanded material range. |
Discover how reactive sputtering can enhance your processes—contact us today for expert guidance!