Hydraulic pumps are critical components in hydraulic systems, and their cooling is essential to ensure efficient operation and longevity. Cooling methods for hydraulic pumps primarily involve managing the heat generated during operation. This heat is typically caused by friction, fluid compression, and inefficiencies in the system. Effective cooling ensures that the pump operates within safe temperature limits, preventing overheating, fluid degradation, and component failure. Cooling methods can be categorized into passive and active systems, with many modern hydraulic systems incorporating a combination of both to optimize performance.
Key Points Explained:
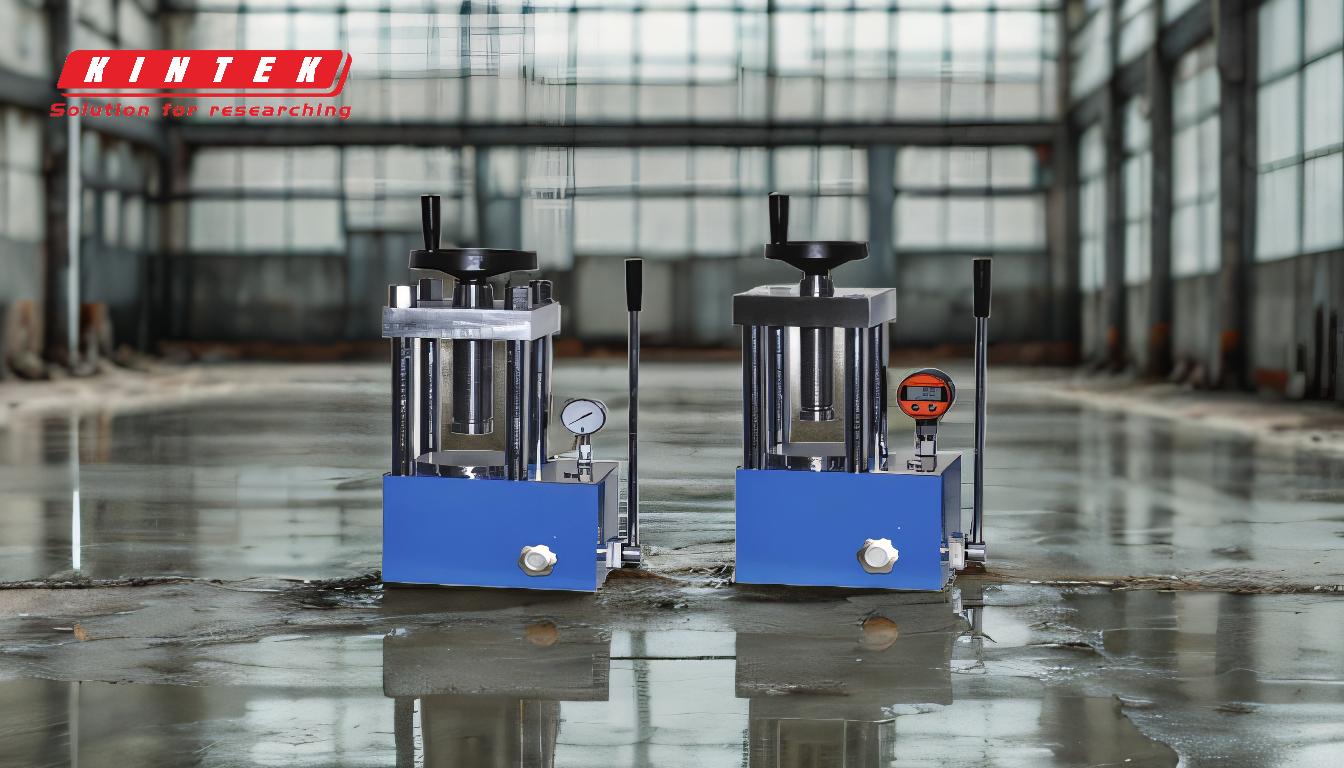
-
Heat Generation in Hydraulic Pumps
- Hydraulic pumps generate heat due to internal friction, fluid compression, and inefficiencies in energy conversion.
- Excessive heat can lead to fluid breakdown, reduced viscosity, and damage to seals and other components.
- Maintaining optimal operating temperatures is crucial for system reliability and efficiency.
-
Passive Cooling Methods
-
Heat Dissipation Through the Reservoir:
- The hydraulic fluid reservoir often acts as a heat sink, allowing heat to dissipate naturally into the surrounding environment.
- Larger reservoirs with increased surface area improve heat dissipation.
-
Cooling Fins and Heat Exchangers:
- Some pumps are designed with cooling fins to increase surface area for heat transfer.
- Heat exchangers, such as air-cooled or shell-and-tube designs, can be integrated into the system to passively cool the fluid.
-
Heat Dissipation Through the Reservoir:
-
Active Cooling Methods
-
Hydraulic Oil Coolers:
- Active cooling systems, such as oil coolers, use external mechanisms to remove heat from the hydraulic fluid.
- These coolers can be air-cooled (using fans) or water-cooled (using a coolant loop) to enhance heat transfer.
-
Forced Air Cooling:
- Fans or blowers are used to increase airflow over heat-generating components, improving heat dissipation.
-
Liquid Cooling Systems:
- In high-performance or heavy-duty applications, liquid cooling systems circulate coolant through channels in the pump or surrounding components to manage heat.
-
Hydraulic Oil Coolers:
-
System Design Considerations
-
Fluid Selection:
- The choice of hydraulic fluid plays a significant role in heat management. Fluids with high thermal stability and appropriate viscosity reduce heat generation.
-
Pump Efficiency:
- Selecting a pump with high efficiency reduces heat generation at the source.
-
Thermal Management Integration:
- Modern hydraulic systems often integrate thermal sensors and control systems to monitor and regulate temperatures automatically.
-
Fluid Selection:
-
Maintenance and Monitoring
- Regular maintenance, such as checking fluid levels, cleaning cooling components, and replacing worn parts, ensures effective cooling.
- Monitoring system temperatures and addressing anomalies promptly prevents overheating and extends the pump's lifespan.
By combining passive and active cooling methods, hydraulic systems can effectively manage heat, ensuring reliable and efficient operation. Proper system design, fluid selection, and maintenance further enhance cooling performance, making them essential considerations for equipment and consumable purchasers.
Summary Table:
Cooling Method | Description |
---|---|
Passive Cooling | - Heat dissipation through reservoirs and cooling fins. |
- Heat exchangers (air-cooled or shell-and-tube designs). | |
Active Cooling | - Hydraulic oil coolers (air-cooled or water-cooled). |
- Forced air cooling using fans or blowers. | |
- Liquid cooling systems for high-performance applications. | |
System Design | - Fluid selection with high thermal stability. |
- High-efficiency pumps and integrated thermal management systems. | |
Maintenance | - Regular checks, cleaning, and temperature monitoring to prevent overheating. |
Ensure your hydraulic pump operates efficiently—contact our experts today for tailored cooling solutions!