Ceramic insulation, when unopened, typically has a shelf life of 18 months from the date of manufacture, while sound control variants may last up to 24 months. However, once opened, partially-used containers should be used within 6-8 months if stored properly. The expiration date is clearly marked on the barcode label of each container, ensuring users can track its usability. Proper storage and adherence to these timelines are critical to maintaining the insulation's effectiveness and performance.
Key Points Explained:
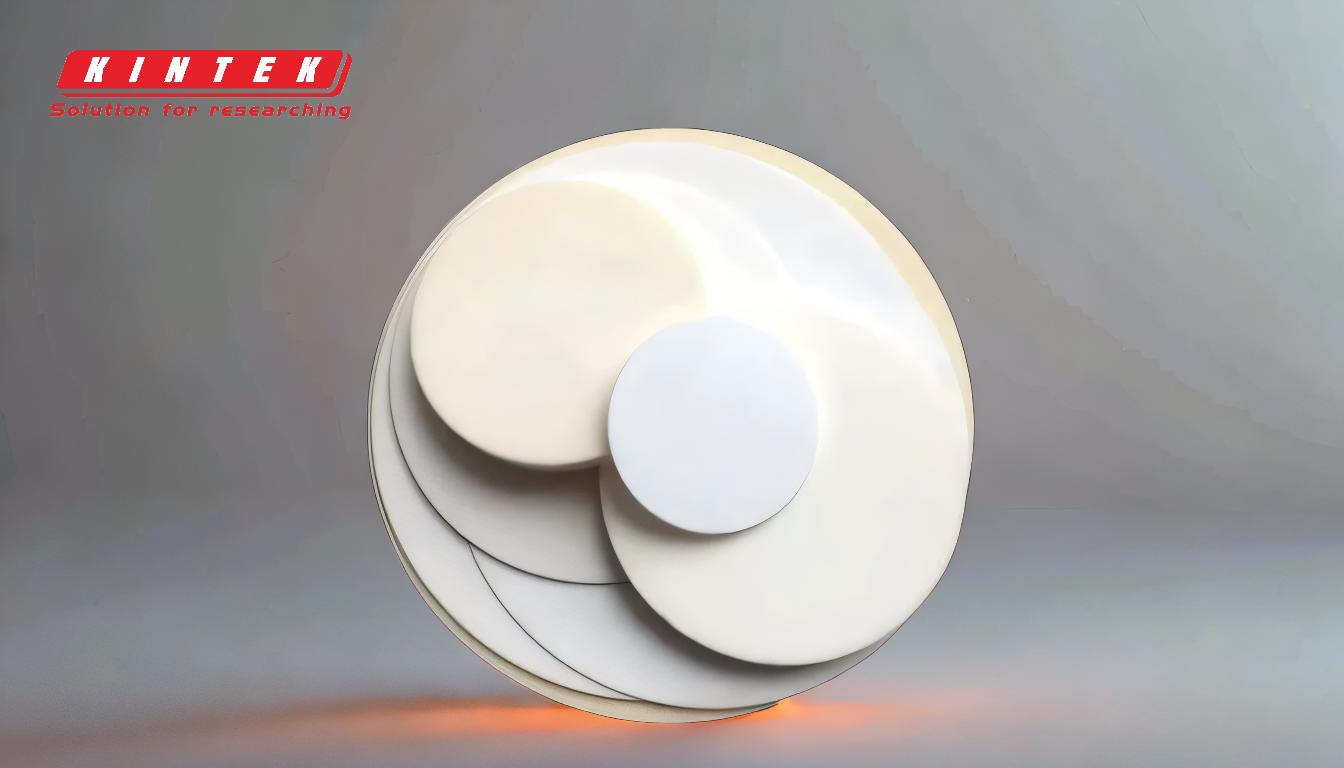
-
Shelf Life of Unopened Ceramic Insulation:
- Unopened ceramic insulation has a shelf life of 18 months from the date of manufacture. This ensures that the material retains its intended properties, such as thermal resistance and durability, when stored in its original, sealed container.
- For sound control variants, the shelf life extends to 24 months, likely due to differences in composition or additives that enhance its acoustic properties.
-
Partially-Used Containers:
- Once a container is opened, the insulation's shelf life decreases significantly. Partially-used containers should be used within 6-8 months, provided they are stored properly. This shorter timeframe is due to exposure to environmental factors like humidity, temperature fluctuations, and contaminants, which can degrade the material over time.
-
Proper Storage Conditions:
- Proper storage is critical to maintaining the insulation's effectiveness. This includes keeping the container tightly sealed, storing it in a cool, dry place, and avoiding exposure to direct sunlight or extreme temperatures. These measures help prevent premature degradation of the insulation material.
-
Expiration Date on Labels:
- Each container of ceramic insulation comes with a barcode label that clearly indicates the expiration date. This allows users to easily track the product's usability and ensure it is used within its optimal lifespan.
- Always check the label before use to confirm the product is still within its recommended shelf life.
-
Implications for Purchasers:
- For equipment or consumable purchasers, understanding the shelf life of ceramic insulation is essential for inventory management. Avoid overstocking to prevent material expiration and waste.
- Prioritize purchasing from suppliers who provide clear labeling and ensure the product is fresh upon delivery.
-
Performance and Effectiveness:
- Using ceramic insulation beyond its shelf life can compromise its thermal and acoustic performance. Degraded insulation may not provide the expected energy efficiency or soundproofing benefits, leading to increased costs and reduced effectiveness in applications.
By adhering to these guidelines, users can maximize the lifespan and performance of ceramic insulation, ensuring it meets the required standards for thermal and acoustic applications.
Summary Table:
Condition | Shelf Life | Key Notes |
---|---|---|
Unopened | 18 months (24 for sound control) | Retains thermal resistance and durability when stored in original, sealed containers. |
Partially-Used | 6-8 months | Store in cool, dry places; avoid humidity, temperature fluctuations, and contaminants. |
Expiration Date | On barcode label | Always check the label before use to confirm usability. |
Ensure your ceramic insulation performs at its best—contact us today for expert advice and fresh supplies!