The cost of a biomass pyrolysis reactor varies significantly depending on factors such as scale, technology, and operational requirements. Small-scale pyrolysis equipment can start as low as $30,500, while more advanced or larger systems may cost upwards of $67,000 or even €1,000,000 for industrial-scale installations. Key cost drivers include feedstock availability, pre-treatment requirements, plant scale, and the type of technology used. Additionally, operational costs, such as energy consumption and maintenance, must be considered. However, the economic viability of pyrolysis is enhanced by factors like energy savings, revenue from by-products (e.g., bio-oil and combustible gas), and local incentives or regulatory support.
Key Points Explained:
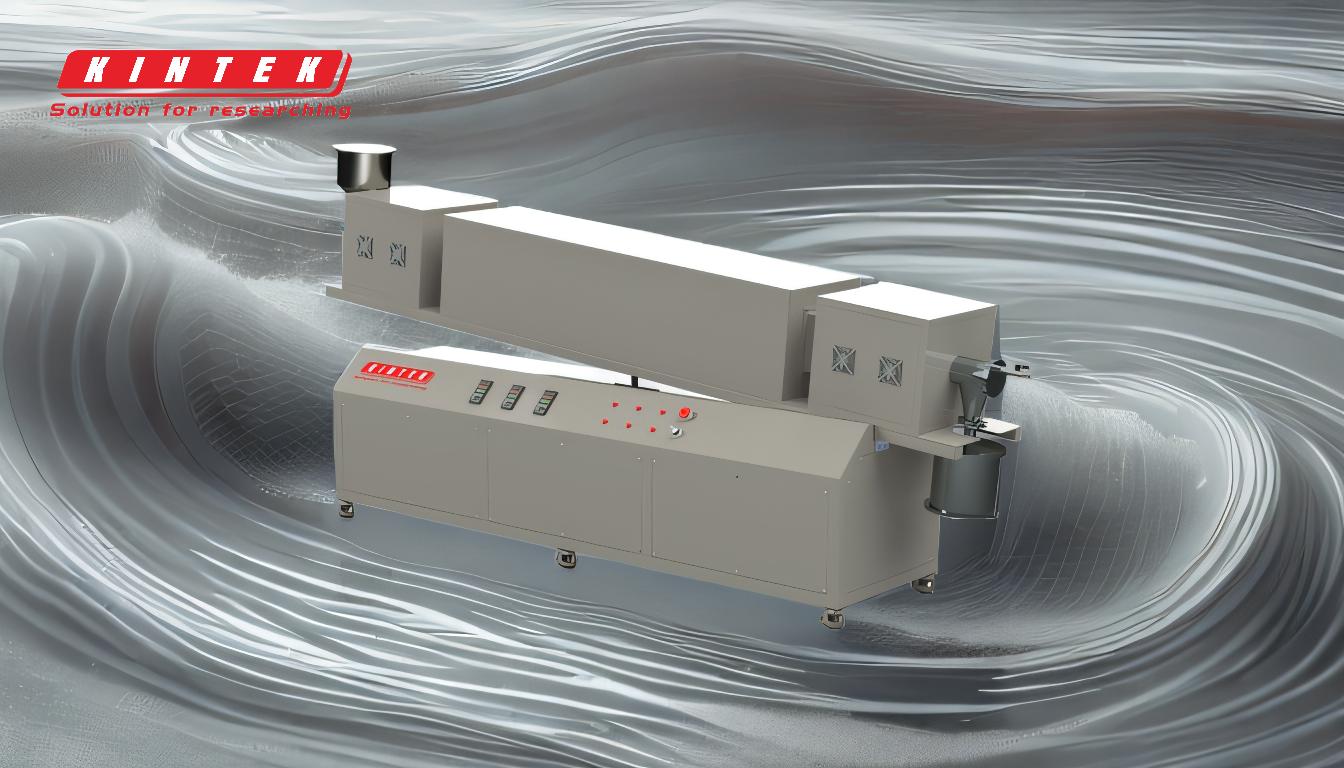
-
Cost Range for Biomass Pyrolysis Reactors:
- The cost of biomass pyrolysis reactors varies widely based on scale and complexity.
- Small-scale systems can start as low as $30,500, making them accessible for small businesses or startups.
- Larger or more advanced systems, such as industrial-scale plants, can cost €1,000,000 or more, including additional infrastructure like fume gas purifiers and operational setups.
- The cost of biomass pyrolysis reactors varies widely based on scale and complexity.
-
Factors Influencing Costs:
- Feedstock Costs: The availability and cost of raw materials significantly impact the overall economics. Feedstock costs can range from 0 to 100 euros per ton, depending on local availability and pre-treatment requirements.
- Plant Scale: Larger plants generally have higher initial investment costs but may benefit from economies of scale, reducing per-unit production costs.
- Technology Type: Advanced pyrolysis technologies may have higher upfront costs but can offer better efficiency and product yields, improving long-term profitability.
-
Operational Costs and Savings:
- Annual operational costs for a pyrolysis plant can be substantial, with estimates around €961,000 for a 2 t/h installation. However, these costs can be offset by:
- Revenue from selling by-products like bio-oil and combustible gas.
- Energy savings from recycling combustible gas as fuel, reducing external energy costs.
- Annual operational costs for a pyrolysis plant can be substantial, with estimates around €961,000 for a 2 t/h installation. However, these costs can be offset by:
-
Economic Viability:
- The feasibility of biomass pyrolysis depends on several factors:
- Local Feed Availability: Proximity to reliable feedstock sources reduces transportation and pre-treatment costs.
- Regulatory and Incentive Frameworks: Supportive policies, such as restrictive landfill regulations or carbon reduction incentives, can enhance profitability.
- Product Value: The market value of pyrolysis products (e.g., bio-oil, char, and gas) plays a critical role in determining overall economic viability.
- The feasibility of biomass pyrolysis depends on several factors:
-
Revenue Streams:
- Pyrolysis plants can generate revenue from multiple sources:
- Bio-Oil Sales: Production costs for pyrolysis oil range between 75 and 300 EUR per ton, depending on feedstock and technology.
- Heat and Energy Sales: Excess heat and energy produced during the process can be sold to offset operational costs.
- Combustible Gas: Recycling gas as fuel reduces external energy expenses, contributing to cost savings.
- Pyrolysis plants can generate revenue from multiple sources:
-
Considerations for Purchasers:
- When evaluating the cost of a biomass pyrolysis reactor, purchasers should consider:
- Initial Investment vs. Long-Term Returns: Higher upfront costs may be justified by long-term savings and revenue potential.
- Local Market Conditions: Feedstock availability, regulatory support, and market demand for pyrolysis products are critical factors.
- Operational Efficiency: Energy-saving features and the ability to recycle by-products can significantly reduce operational expenses.
- When evaluating the cost of a biomass pyrolysis reactor, purchasers should consider:
In summary, the cost of a biomass pyrolysis reactor is influenced by a combination of initial investment, operational expenses, and revenue potential. While small-scale systems offer affordability, larger installations may provide greater efficiency and profitability, especially in regions with favorable feedstock availability and regulatory support. Purchasers should carefully evaluate these factors to determine the most cost-effective and economically viable solution for their specific needs.
Summary Table:
Aspect | Details |
---|---|
Cost Range | Small-scale: $30,500+; Industrial-scale: €1,000,000+ |
Key Cost Factors | Feedstock, plant scale, technology type, operational costs |
Operational Costs | ~€961,000/year for 2 t/h; offset by bio-oil, gas sales, and energy savings |
Revenue Streams | Bio-oil (75-300 EUR/ton), heat/energy sales, combustible gas recycling |
Economic Viability | Depends on local feed availability, regulatory support, and product value |
Ready to invest in a biomass pyrolysis reactor? Contact us today for expert guidance and tailored solutions!