To create nickel foam, the process involves electroplating nickel onto a polyurethane foam substrate, followed by sintering to form a stable and conductive structure. The polyurethane foam must first be made conductive by immersing it in a colloidal graphite dispersion and then drying it. This conductive layer allows for effective electroplating of nickel. The final step involves sintering, which strengthens the structure by bonding the nickel particles together. Below is a detailed breakdown of the process and its key steps.
Key Points Explained:
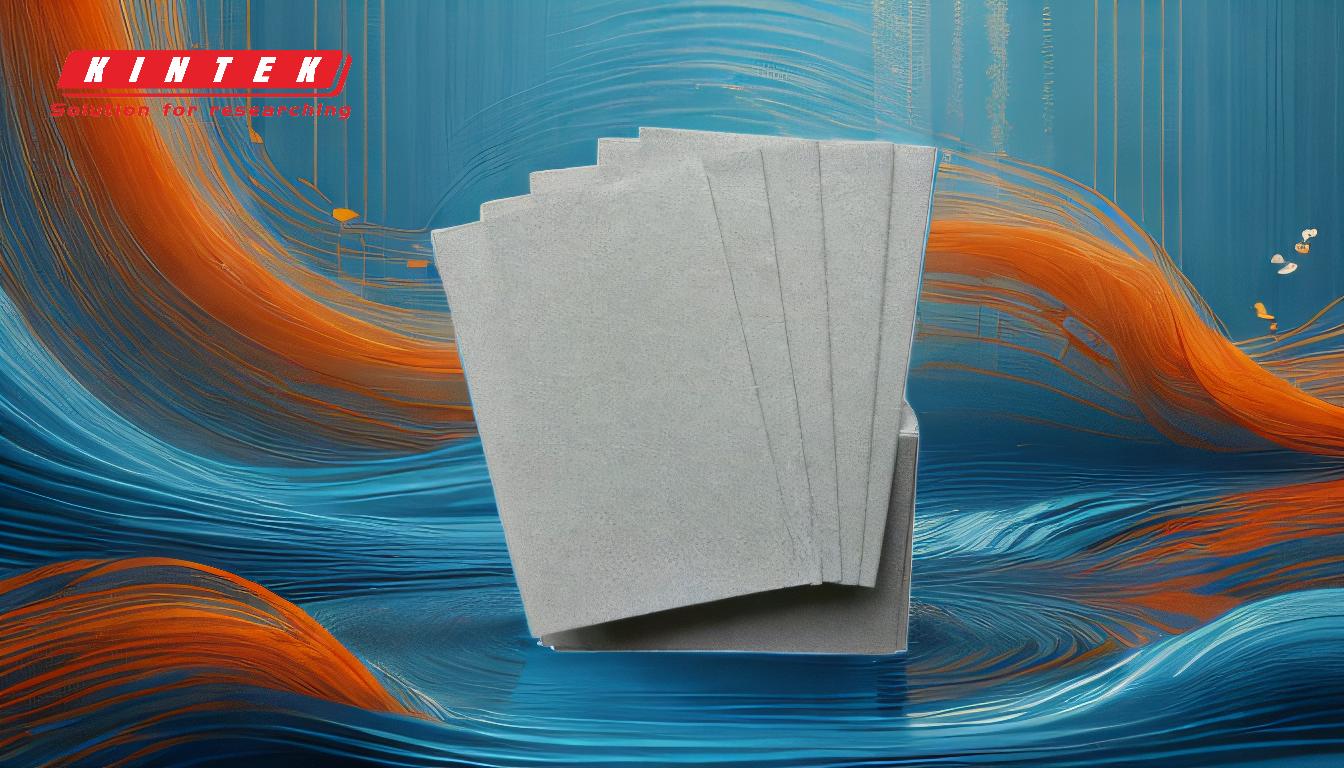
-
Preparation of Polyurethane Foam
- Polyurethane foam is chosen as the base material due to its porous and flexible structure, which is ideal for creating a lightweight and high-surface-area foam.
- The foam must be cleaned and prepared to ensure proper adhesion of the conductive coating.
-
Making the Foam Conductive
- The foam is immersed in a colloidal graphite dispersion. Graphite is a conductive material that coats the foam's surface, enabling it to conduct electricity.
- After immersion, the foam is dried to remove any solvents or moisture, leaving behind a thin, conductive graphite layer.
-
Electroplating Nickel onto the Foam
- The conductive foam is placed in an electroplating bath containing a nickel salt solution.
- An electric current is applied, causing nickel ions to deposit onto the foam's surface. This process uniformly coats the foam's structure with a layer of nickel.
-
Sintering the Nickel-Coated Foam
- After electroplating, the nickel-coated foam undergoes sintering, a heat treatment process.
- Sintering bonds the nickel particles together, creating a strong and stable metallic structure while maintaining the foam's porous nature.
-
Final Product Characteristics
- The resulting nickel foam is lightweight, highly porous, and electrically conductive.
- It is widely used in applications such as battery electrodes, catalysts, and filters due to its unique properties.
This step-by-step process ensures the creation of high-quality nickel foam, tailored for various industrial applications. The combination of electroplating and sintering provides a durable and functional material with excellent conductivity and structural integrity.
Summary Table:
Step | Description |
---|---|
1. Preparation of Foam | Clean and prepare polyurethane foam for conductive coating adhesion. |
2. Making the Foam Conductive | Immerse foam in colloidal graphite dispersion and dry to create a conductive layer. |
3. Electroplating Nickel | Apply nickel ions via electroplating to uniformly coat the foam. |
4. Sintering | Heat-treat the nickel-coated foam to bond particles and strengthen the structure. |
5. Final Product | Resulting nickel foam is lightweight, porous, and electrically conductive. |
Discover how nickel foam can enhance your industrial applications—contact us today for more details!