Using a press mould involves a series of steps to ensure the clay is evenly distributed and properly shaped. The process begins with preparing the clay slab and carefully lining it onto the mould. Gentle and even pressure is applied to ensure the clay conforms to the mould's shape. After allowing the clay to firm up, it is detached from the mould, resulting in a uniform replication of the mould's design. This method is ideal for creating consistent shapes and designs in pottery or other clay-based crafts.
Key Points Explained:
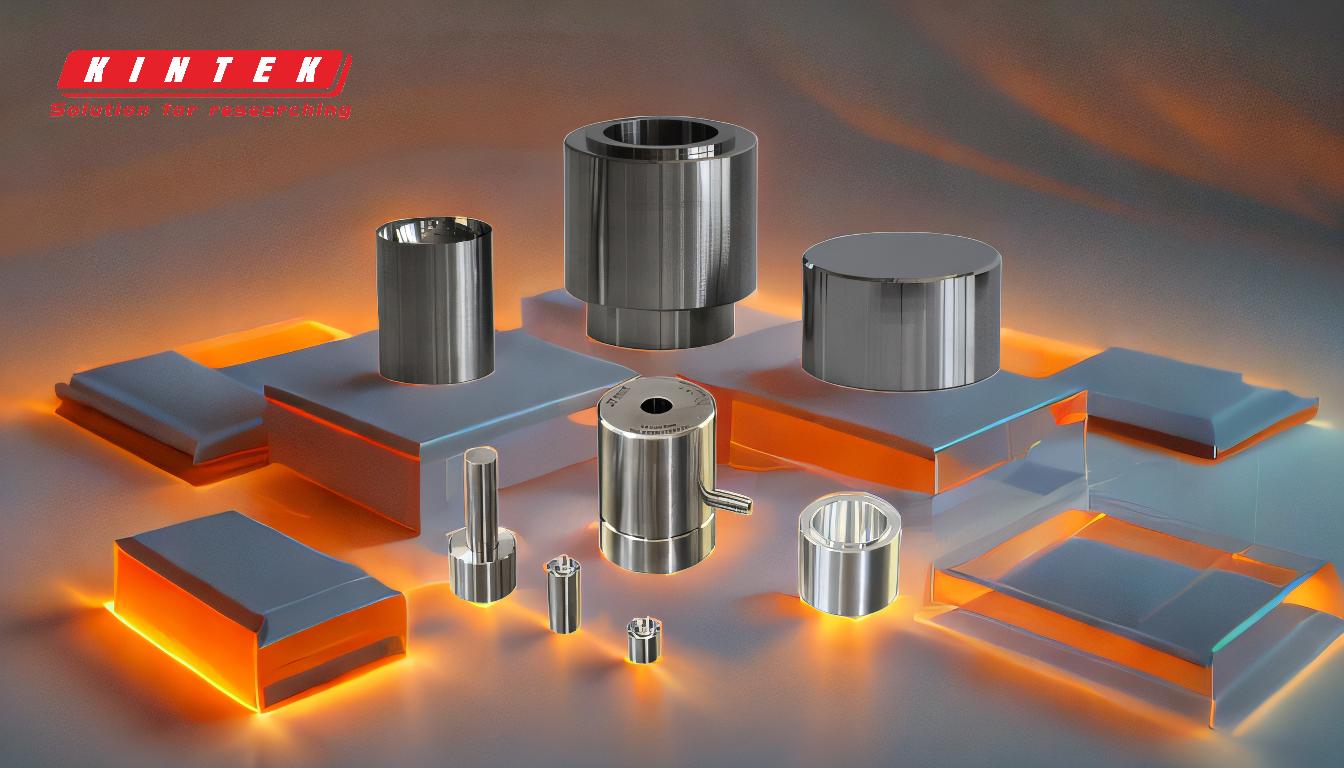
-
Preparing the Clay Slab:
- Start by rolling out a slab of fresh clay to the desired thickness. Ensure the clay is uniform in thickness to avoid uneven shaping.
- The slab should be large enough to cover the entire mould with some excess to trim later.
-
Lining the Clay on the Mould:
- Carefully place the clay slab onto the mould. Ensure it covers all the contours and details of the mould.
- Gently press the clay into the mould, starting from the center and moving outwards to the edges. This helps to avoid air pockets and ensures the clay adheres well to the mould.
-
Applying Even Pressure:
- Use your hands or a soft tool to press the clay gently and evenly across the surface of the mould. Pay special attention to intricate details and edges.
- Ensure consistent pressure to avoid thin spots or weak areas in the final product.
-
Allowing the Clay to Firm Up:
- Once the clay is evenly pressed into the mould, let it sit for a period to firm up. The time required depends on the type of clay and the ambient conditions.
- The clay should be firm enough to hold its shape but still pliable enough to be removed from the mould without cracking.
-
Detaching the Clay from the Mould:
- Carefully lift the clay away from the mould. Start from one edge and slowly peel it back to avoid distorting the shape.
- If the clay sticks, gently wiggle it loose or use a thin tool to help release it without damaging the details.
-
Trimming and Finishing:
- Trim any excess clay from the edges using a sharp tool. Smooth out any rough edges or imperfections.
- Allow the piece to dry completely before further finishing, such as sanding, painting, or glazing.
By following these steps, you can effectively use a press mould to create uniform and detailed clay pieces. This method is particularly useful for producing multiple identical items, ensuring consistency in shape and design.
Summary Table:
Step | Key Actions |
---|---|
Preparing the Clay Slab | Roll out a uniform slab of clay, ensuring it covers the mould with excess to trim. |
Lining the Clay on the Mould | Carefully place the clay, pressing from the center outward to avoid air pockets. |
Applying Even Pressure | Use hands or tools to press gently and evenly, focusing on intricate details. |
Allowing the Clay to Firm Up | Let the clay sit until firm but pliable for easy removal. |
Detaching the Clay from the Mould | Lift the clay carefully, starting from one edge to avoid distortion. |
Trimming and Finishing | Trim excess clay, smooth edges, and let the piece dry before further finishing. |
Ready to create consistent pottery designs? Contact us today for expert guidance and tools!