A higher CFM (Cubic Feet per Minute) vacuum pump is not inherently better; its suitability depends on the specific application and requirements. CFM measures the volume of air a pump can move per minute, which is critical for tasks requiring rapid evacuation or handling large volumes of gas. However, other factors like vacuum level, gas type, system volume, and process requirements must be considered. For instance, a high CFM pump may be unnecessary for small-scale applications or processes requiring precise vacuum levels. Over-specifying CFM can lead to inefficiencies, higher costs, and potential operational issues. Therefore, the ideal CFM value should align with the application's needs, balancing performance, efficiency, and cost.
Key Points Explained:
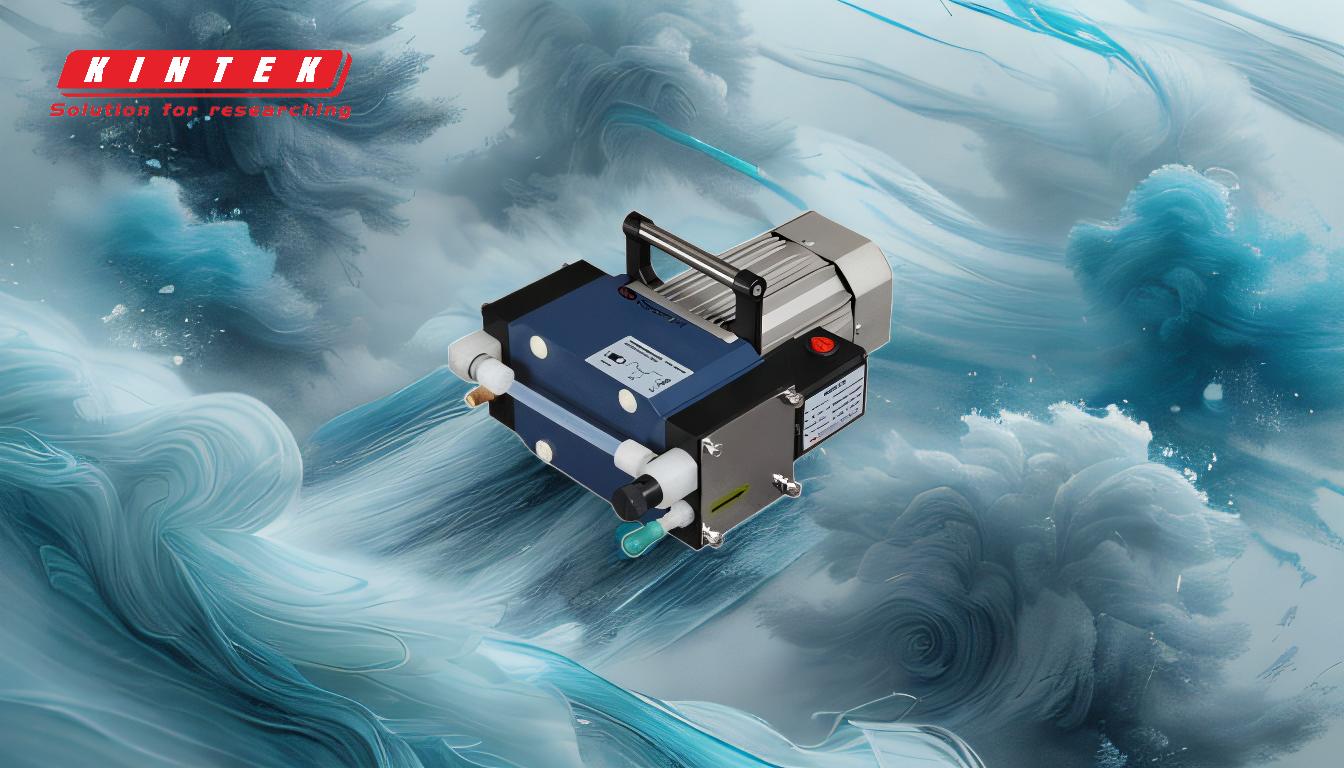
-
Understanding CFM in Vacuum Pumps:
- CFM measures the volume of air a vacuum pump can move per minute.
- It is a critical parameter for applications requiring rapid evacuation or handling large volumes of gas.
- However, CFM alone does not determine a pump's overall effectiveness.
-
Application-Specific Requirements:
- The suitability of a higher CFM pump depends on the specific application.
- For example, industrial processes like vacuum forming or large-scale degassing may benefit from high CFM pumps.
- Conversely, laboratory applications or small-scale processes may not require high CFM, as precision and vacuum level are more critical.
-
Vacuum Level and Gas Type:
- The required vacuum level (ultimate pressure) is a key consideration.
- High CFM pumps may not achieve the necessary vacuum depth for certain applications.
- The type of gas being pumped also affects performance; some gases require specialized pumps, regardless of CFM.
-
System Volume and Pumpdown Time:
- The internal volume of the vacuum vessel and the desired pumpdown time influence CFM requirements.
- A higher CFM pump can reduce pumpdown time for large systems but may be overkill for smaller systems.
-
Operational Efficiency and Cost:
- Over-specifying CFM can lead to inefficiencies, such as excessive energy consumption.
- Higher CFM pumps often come with higher upfront and operational costs.
- Balancing CFM with other factors ensures cost-effective and efficient operation.
-
Additional Considerations:
- Motor Speed and Horsepower: Higher CFM pumps may require more powerful motors, increasing noise and maintenance needs.
- Chemical Compatibility: Ensure the pump materials are compatible with the gases being handled.
- Maintenance and Lifespan: Higher CFM pumps may have shorter lifespans or require more frequent maintenance if not properly matched to the application.
-
Conclusion:
- A higher CFM vacuum pump is not universally better; its value depends on the specific application.
- Selecting the right pump involves balancing CFM with other factors like vacuum level, gas type, system volume, and cost.
- Properly matching the pump to the application ensures optimal performance, efficiency, and longevity.
Summary Table:
Factor | Consideration |
---|---|
CFM | Measures air volume moved per minute; critical for rapid evacuation or large volumes. |
Application | High CFM suits industrial processes; low CFM is better for precision tasks. |
Vacuum Level | Required ultimate pressure; high CFM may not achieve necessary vacuum depth. |
Gas Type | Some gases require specialized pumps, regardless of CFM. |
System Volume | Larger systems benefit from higher CFM; smaller systems may not need it. |
Operational Efficiency | Over-specifying CFM can lead to inefficiencies and higher costs. |
Additional Factors | Motor speed, chemical compatibility, and maintenance needs also play a role. |
Need help selecting the right vacuum pump for your application? Contact our experts today for personalized advice!