Biofuels can be cost-effective, but their economic viability depends on several factors, including production methods, feedstock availability, government policies, and market conditions. While biofuels offer environmental benefits and energy security, their production costs are often higher than fossil fuels. However, advancements in technology, economies of scale, and government subsidies can make biofuels more competitive. The cost-effectiveness of biofuels varies by type (e.g., biodiesel, ethanol) and region, with some biofuels being more economically viable than others. Overall, biofuels are becoming increasingly cost-effective as technology improves and demand for sustainable energy grows.
Key Points Explained:
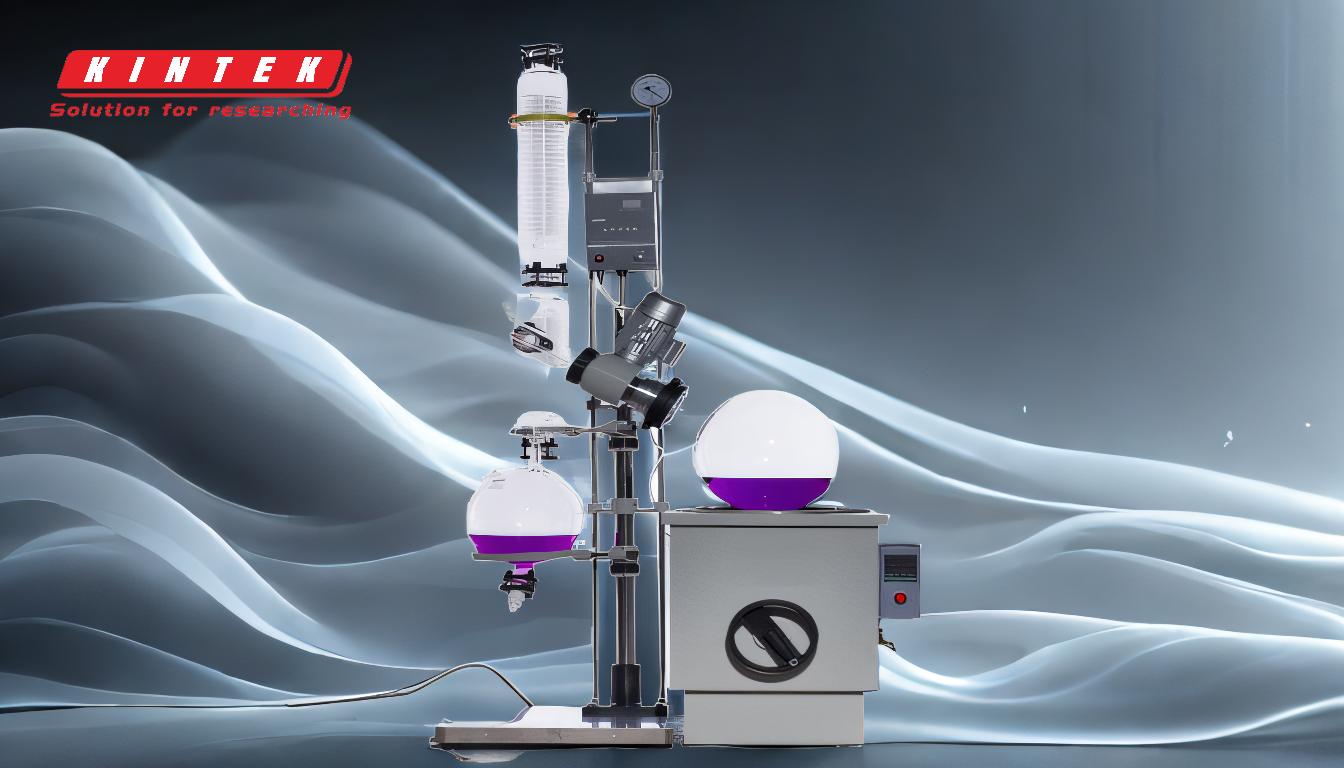
-
Production Costs of Biofuels:
- Biofuels are generally more expensive to produce than fossil fuels due to the costs associated with feedstock cultivation, processing, and conversion.
- Feedstock costs (e.g., corn, sugarcane, algae) are a significant factor in determining the overall cost of biofuels.
- Advanced biofuels, such as those derived from algae or waste materials, often have higher production costs but offer greater environmental benefits.
-
Types of Biofuels and Their Cost-Effectiveness:
- First-Generation Biofuels: These include ethanol (from corn or sugarcane) and biodiesel (from vegetable oils or animal fats). They are relatively cost-effective but face criticism for competing with food production and land use.
- Second-Generation Biofuels: Made from non-food biomass (e.g., agricultural residues, wood), these biofuels are more sustainable but currently more expensive due to complex production processes.
- Third-Generation Biofuels: Derived from algae or microorganisms, these have high potential but are still in the experimental stage and not yet cost-competitive.
-
Impact of Government Policies and Subsidies:
- Government incentives, such as tax credits, grants, and mandates (e.g., Renewable Fuel Standards), play a crucial role in making biofuels cost-effective.
- Subsidies can offset production costs and encourage investment in biofuel technology.
- Policies promoting renewable energy can create a favorable market environment for biofuels.
-
Economies of Scale and Technological Advancements:
- As biofuel production scales up, per-unit costs decrease due to economies of scale.
- Technological innovations, such as improved fermentation processes and genetic engineering of feedstock, are reducing production costs and improving efficiency.
- Research into alternative feedstocks (e.g., algae, waste materials) is also driving down costs.
-
Environmental and Social Benefits:
- Biofuels reduce greenhouse gas emissions compared to fossil fuels, contributing to climate change mitigation.
- They enhance energy security by reducing dependence on imported oil.
- Biofuels can create jobs in rural areas and support agricultural economies.
-
Regional Variations in Cost-Effectiveness:
- The cost-effectiveness of biofuels varies by region due to differences in feedstock availability, labor costs, and infrastructure.
- For example, Brazil’s sugarcane-based ethanol is highly cost-effective due to favorable climate conditions and established production systems.
- In contrast, regions with limited agricultural resources may find biofuels less economically viable.
-
Market Demand and Future Prospects:
- Growing demand for sustainable energy is driving investment in biofuels and improving their cost-effectiveness.
- As fossil fuel prices fluctuate and environmental regulations tighten, biofuels are likely to become more competitive.
- Long-term cost reductions are expected as technology matures and production processes become more efficient.
In conclusion, while biofuels are not universally cost-effective at present, they are becoming increasingly viable due to technological advancements, government support, and growing demand for sustainable energy. Their cost-effectiveness will continue to improve as the industry evolves.
Summary Table:
Aspect | Key Insights |
---|---|
Production Costs | Higher than fossil fuels due to feedstock and processing costs. |
Types of Biofuels | First-gen: cost-effective; Second-gen: sustainable but costly; Third-gen: experimental. |
Government Policies | Subsidies and mandates make biofuels more competitive. |
Technological Advances | Innovations reduce costs and improve efficiency. |
Environmental Benefits | Lower greenhouse gas emissions and enhanced energy security. |
Regional Variations | Cost-effectiveness varies by feedstock availability and infrastructure. |
Future Prospects | Growing demand and technological advancements will improve cost-effectiveness. |
Want to learn more about biofuels and their economic viability? Contact us today for expert insights!