Industrial vacuum systems are specialized equipment designed to create and maintain a vacuum environment for various industrial processes. These systems are critical in industries such as electronics, metallurgy, and materials science, where controlled environments are necessary for processes like thin-film deposition, metal melting, and solvent evaporation. Industrial vacuum systems are tailored to specific applications, ensuring optimal performance and efficiency. They are often integrated with other technologies, such as sputtering systems, induction melting, and cold traps, to enhance material properties and process outcomes.
Key Points Explained:
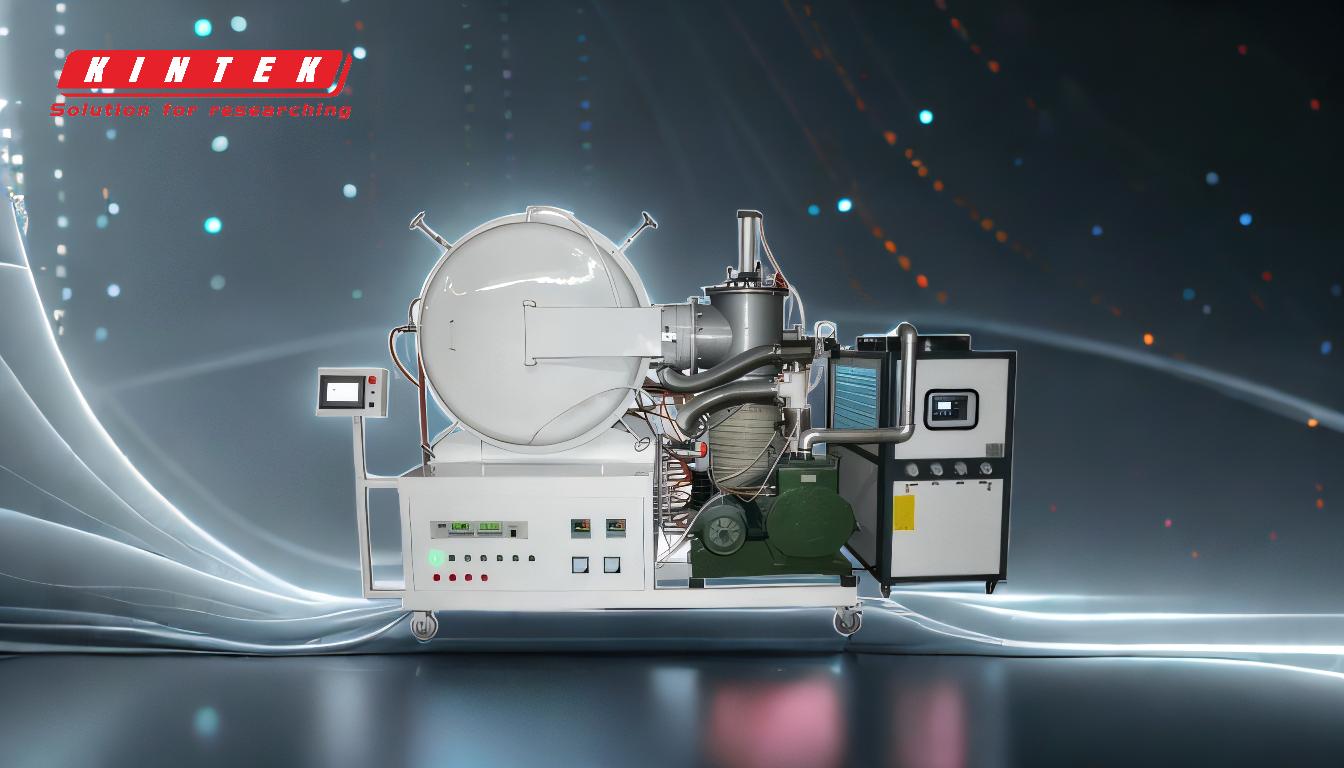
-
Definition and Purpose of Industrial Vacuum Systems:
- Industrial vacuum systems are engineered to create a vacuum environment, which is essential for processes that require controlled atmospheres. These systems are used in applications such as thin-film deposition, metal smelting, and solvent evaporation. The vacuum environment helps in reducing contamination, improving material properties, and enhancing process efficiency.
-
Applications in Thin-Film Deposition:
- Industrial vacuum systems are integral to processes like Chemical Vapor Deposition (CVD) and sputtering. CVD systems are used to generate thin layers on various materials, which are crucial in industries ranging from electronics manufacturing to packaging. Sputtering techniques, such as DC and RF sputtering, are used to deposit thin films on substrates, with each method offering specific advantages depending on the material and application.
-
Role in Vacuum Induction Melting:
- Vacuum induction melting is a widely used method in vacuum metallurgy. It is employed to smelt high-temperature alloys, such as nickel-based, cobalt-based, and iron-based alloys, significantly improving their thermal processing and mechanical properties. The vacuum environment in this process ensures material purity and quality, making it essential for producing high-performance alloys.
-
Importance in Solvent Evaporation:
- Industrial vacuum systems are also crucial in processes like rotary evaporation, where solvents need to be removed under vacuum conditions. The selection of an appropriate vacuum pump for rotary evaporation depends on factors such as the type of solvents, the size of the evaporation flask, and the temperature of the heating bath. These systems ensure efficient solvent removal and process control.
-
Integration with Cold Traps:
- Cold traps are often used in conjunction with industrial vacuum systems to capture outgassing or contaminants. They are particularly useful in applications like brazing and freeze drying, where significant amounts of liquid or vapor need to be removed from the vacuum environment. Cold traps help maintain the integrity of the vacuum system and improve process outcomes.
-
Advantages of Vacuum Environments:
- The use of industrial vacuum systems offers several advantages, including reduced contamination, improved material properties, and enhanced process efficiency. For example, vacuum induction melting can significantly improve the toughness, fatigue strength, and corrosion resistance of metal materials. Similarly, vacuum environments in sputtering processes help in achieving high-quality thin films with precise control over deposition parameters.
-
Customization and Selection Criteria:
- Industrial vacuum systems are often customized to meet specific process requirements. Factors such as the type of materials being processed, the desired vacuum level, and the specific application dictate the design and selection of these systems. For instance, the choice between DC and RF sputtering depends on the conductivity of the target material and the desired deposition rate.
In summary, industrial vacuum systems are versatile and essential tools in modern manufacturing and materials science. They enable a wide range of processes that require controlled environments, ensuring high-quality outcomes and efficient operations. Whether it's for thin-film deposition, metal melting, or solvent evaporation, these systems play a critical role in advancing industrial capabilities.
Summary Table:
Key Aspects | Details |
---|---|
Definition | Specialized equipment for creating and maintaining vacuum environments. |
Applications | Thin-film deposition, vacuum induction melting, solvent evaporation. |
Key Processes | CVD, sputtering, rotary evaporation, cold trap integration. |
Advantages | Reduced contamination, improved material properties, enhanced efficiency. |
Customization | Tailored to specific materials, vacuum levels, and application needs. |
Learn how industrial vacuum systems can optimize your processes—contact us today for expert guidance!