Metal casting is a manufacturing process where molten metal is poured into a mold to create a desired shape. The four main types of casting are sand casting, investment casting, die casting, and evaporative casting. Each method has unique characteristics, advantages, and applications, making them suitable for different industrial needs. Sand casting is versatile and cost-effective, investment casting offers high precision and surface finish, die casting is ideal for high-volume production, and evaporative casting is known for its simplicity and low-cost tooling. Understanding these methods helps in selecting the right process for specific manufacturing requirements.
Key Points Explained:
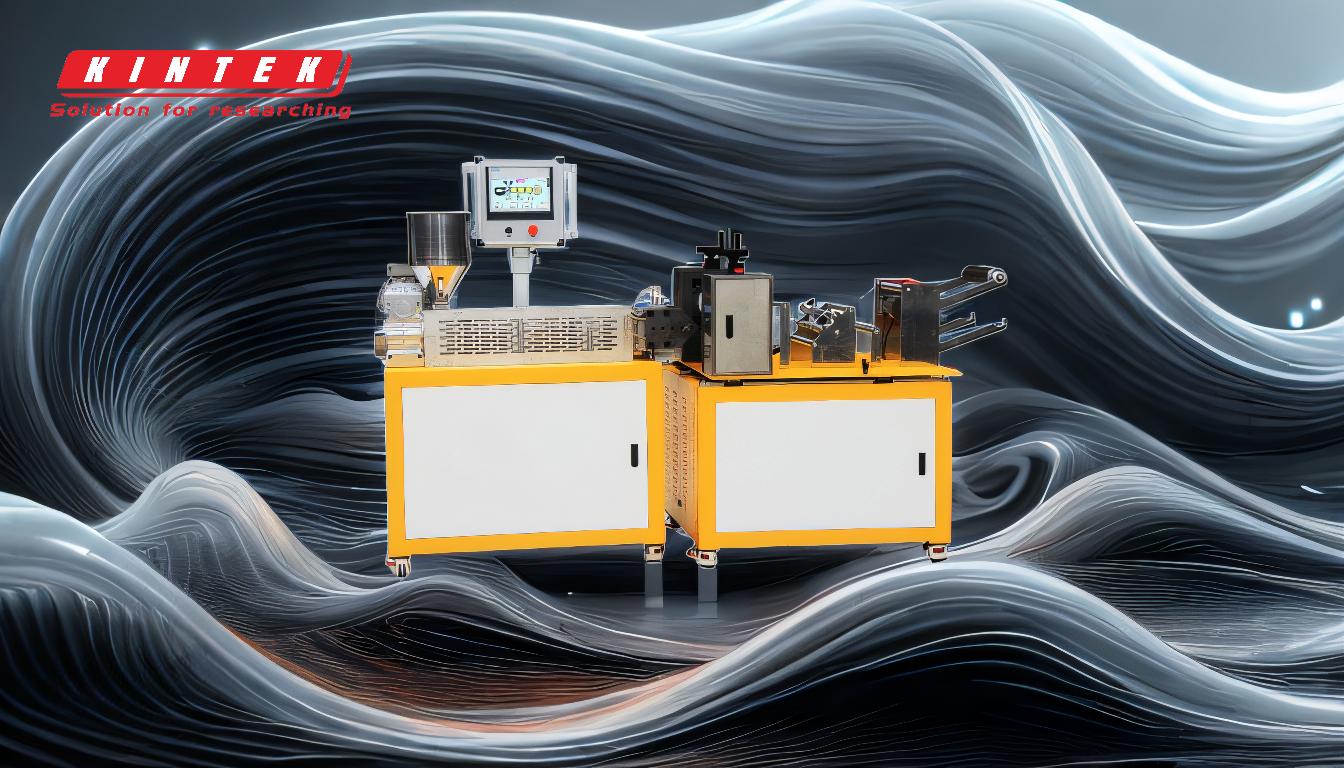
-
Sand Casting
- Process: Sand casting involves creating a mold from a mixture of sand and a binder. The mold is then filled with molten metal, which solidifies to form the desired shape.
-
Advantages:
- Versatile and suitable for a wide range of metals and alloys.
- Cost-effective for both small and large-scale production.
- Allows for complex geometries and large parts.
- Applications: Commonly used in automotive, aerospace, and heavy machinery industries for components like engine blocks, cylinder heads, and gears.
-
Investment Casting
- Process: Also known as lost-wax casting, this method involves creating a wax pattern, coating it with a ceramic shell, and then melting the wax to leave a hollow mold. Molten metal is poured into the mold to form the part.
-
Advantages:
- High precision and excellent surface finish.
- Suitable for intricate designs and thin-walled parts.
- Minimal post-processing required.
- Applications: Widely used in jewelry, dental implants, and aerospace components like turbine blades.
-
Die Casting
- Process: Die casting uses reusable metal molds (dies) into which molten metal is injected under high pressure. The metal solidifies quickly, and the part is ejected from the die.
-
Advantages:
- High production rates and repeatability.
- Excellent dimensional accuracy and surface finish.
- Ideal for mass production of small to medium-sized parts.
- Applications: Commonly used in the automotive industry for parts like engine components, housings, and brackets, as well as in consumer electronics.
-
Evaporative Casting
- Process: Also known as lost foam casting, this method uses a foam pattern coated with a refractory material. The foam is vaporized when molten metal is poured into the mold, leaving the metal to take its shape.
-
Advantages:
- Simple and low-cost tooling.
- Suitable for complex shapes and large parts.
- Minimal waste and no need for cores.
- Applications: Often used in the production of automotive components, such as cylinder heads and engine blocks, as well as in art and sculpture.
By understanding these four main types of casting, manufacturers can choose the most appropriate method based on factors like material, complexity, volume, and cost requirements. Each method offers distinct benefits, making them indispensable in modern manufacturing.
Summary Table:
Type | Process | Advantages | Applications |
---|---|---|---|
Sand Casting | Mold made from sand and binder; molten metal poured into the mold. | Versatile, cost-effective, suitable for complex geometries and large parts. | Automotive, aerospace, heavy machinery (e.g., engine blocks, cylinder heads). |
Investment Casting | Wax pattern coated with ceramic shell; wax melted, leaving a mold for metal. | High precision, excellent surface finish, minimal post-processing. | Jewelry, dental implants, aerospace (e.g., turbine blades). |
Die Casting | Reusable metal molds; molten metal injected under high pressure. | High production rates, excellent dimensional accuracy, ideal for mass production. | Automotive (e.g., engine components), consumer electronics. |
Evaporative Casting | Foam pattern coated with refractory material; foam vaporized by molten metal. | Simple, low-cost tooling, suitable for complex shapes and large parts. | Automotive (e.g., cylinder heads), art, and sculpture. |
Need help selecting the right casting method for your project? Contact our experts today !