Wiped film evaporators (WFEs) offer numerous advantages, making them a preferred choice for distillation and purification processes, particularly for heat-sensitive and high-viscosity materials. These systems excel in preserving the quality of the feed liquid by minimizing its exposure to high temperatures, ensuring efficient heat transfer, and enabling continuous operation. They are highly versatile, capable of processing challenging materials like high-solids or dirty feeds, while also being cost-effective due to reduced equipment requirements, space utilization, and processing time. Additionally, WFEs are scalable, customizable, and capable of producing high-quality distillates with improved yields and efficiency.
Key Points Explained:
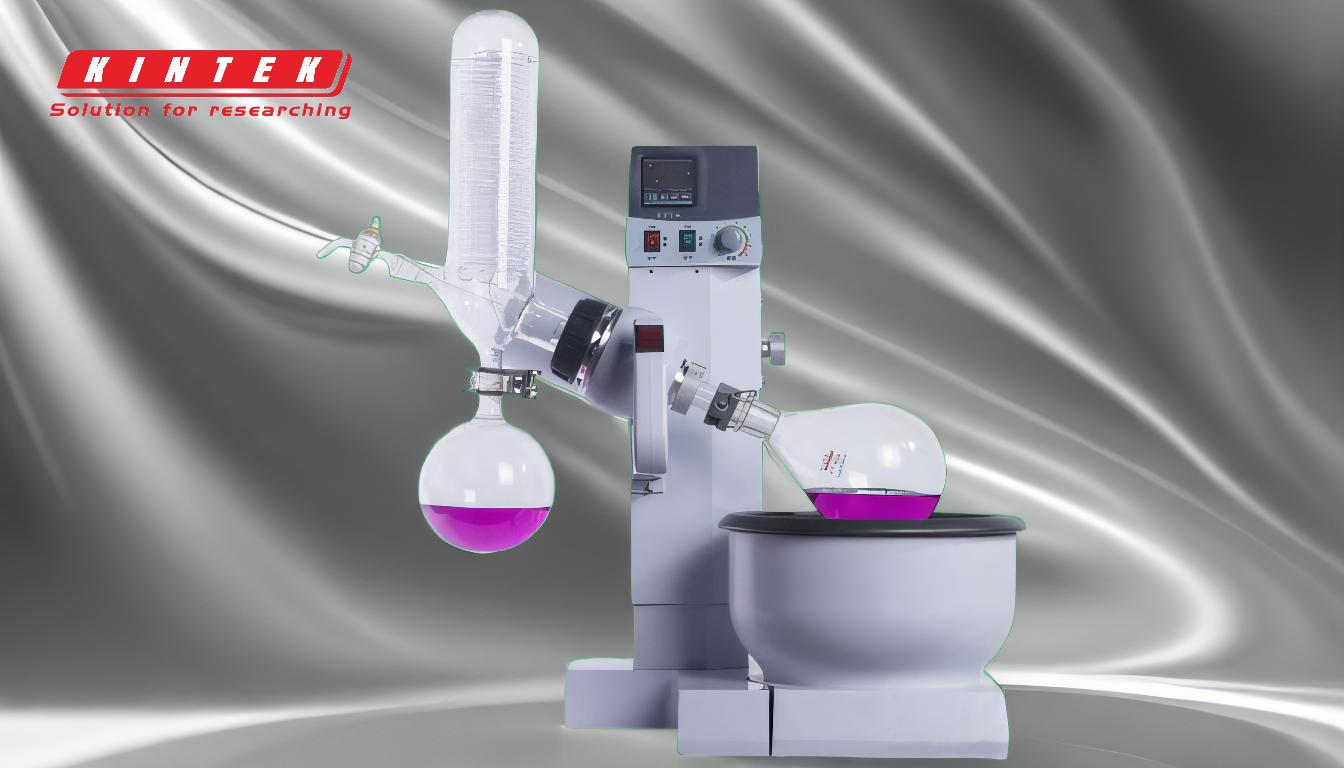
-
Reduced Residence Time:
- Wiped film evaporators significantly shorten the residence time of the feed liquid to just 1-3 minutes. This minimizes the exposure of sensitive components, such as cannabinoids or delicate oils, to high temperatures, preserving their quality and integrity. This is particularly beneficial for heat-sensitive materials.
-
Efficient Heat Transfer:
- The bow wave mechanism in WFEs enhances heat transfer efficiency. This ensures uniform heating of the liquid, reducing the risk of localized overheating or degradation, which is critical for maintaining product quality.
-
Handling High-Viscosity and High-Solids Materials:
- WFEs are designed to process high-viscosity and high-solids materials effectively. The mechanical wiping action prevents fouling and ensures smooth operation, even with challenging feedstocks.
-
Refining Heat-Sensitive and Dirty Materials:
- The use of low evaporation temperatures and vacuums allows WFEs to refine heat-sensitive and dirty materials without compromising their quality. This makes them ideal for applications requiring high-purity outputs.
-
Scalability and Continuous Operation:
- WFEs are capable of processing large batches of liquids, making them suitable for large-scale production. Their continuous operation mode eliminates the need for frequent changeovers, increasing productivity and reducing downtime.
-
Cost Efficiency:
- By minimizing equipment requirements, space utilization, and processing time, WFEs reduce overall operational costs. Their ability to operate continuously further enhances cost-effectiveness.
-
Improved Yields and Efficiency:
- The use of robust turbo molecular pumps in WFEs achieves very low pressures, resulting in higher yields and improved efficiency compared to traditional distillation methods. This is particularly advantageous for industries requiring high-purity distillates.
-
Customization and Control:
- WFEs offer easy-to-use controls that allow operators to optimize material feed rates, vacuum levels, and temperatures. This customization ensures repeatable processes and the ability to achieve desired distillate compositions.
-
High-Quality Final Product:
- Despite requiring two passes through the system for optimal results, WFEs produce an exemplary end product with extremely high quality. This is due to the even and efficient heat transfer, regardless of the viscosity of the feed material.
-
Versatility and Adaptability:
- WFEs are versatile and can be adapted to various applications, from pharmaceutical and chemical processing to food and cannabis industries. Their ability to handle diverse materials and produce consistent results makes them a valuable asset in many sectors.
In summary, wiped film evaporators combine efficiency, scalability, and precision to deliver high-quality outputs while reducing operational costs and preserving the integrity of sensitive materials. Their ability to operate continuously and handle challenging feedstocks makes them a superior choice for modern distillation processes.
Summary Table:
Advantage | Description |
---|---|
Reduced Residence Time | Minimizes exposure of sensitive materials to high temperatures (1-3 minutes). |
Efficient Heat Transfer | Ensures uniform heating, preventing localized overheating or degradation. |
Handles High-Viscosity Materials | Processes challenging feedstocks without fouling. |
Refines Heat-Sensitive Materials | Uses low evaporation temperatures and vacuums for high-purity outputs. |
Scalability and Continuous Operation | Processes large batches continuously, reducing downtime. |
Cost Efficiency | Reduces equipment requirements, space utilization, and processing time. |
Improved Yields and Efficiency | Achieves higher yields with low-pressure turbo molecular pumps. |
Customization and Control | Optimizes feed rates, vacuum levels, and temperatures for repeatable processes. |
High-Quality Final Product | Produces exemplary distillates with even heat transfer. |
Versatility and Adaptability | Suitable for pharmaceutical, chemical, food, and cannabis industries. |
Maximize your distillation efficiency with wiped film evaporators—contact our experts today to learn more!