The sputtering technique offers several advantages over other deposition methods, making it a preferred choice for various applications. These advantages include the ability to coat a wide range of materials at reduced temperatures, molecular-level precision, reproducibility, and simpler process automation. Sputtering is relatively inexpensive and can deposit materials with very high melting points, which are difficult to evaporate. The composition of sputtered films closely matches the source material, and these films typically have better adhesion to substrates. Additionally, sputtering is maintenance-free, suitable for ultrahigh vacuum applications, and supports advanced processes like epitaxial growth. The technique also allows for pure and accurate atomic-level film deposition, more uniform films, and higher packing densities even at low temperatures.
Key Points Explained:
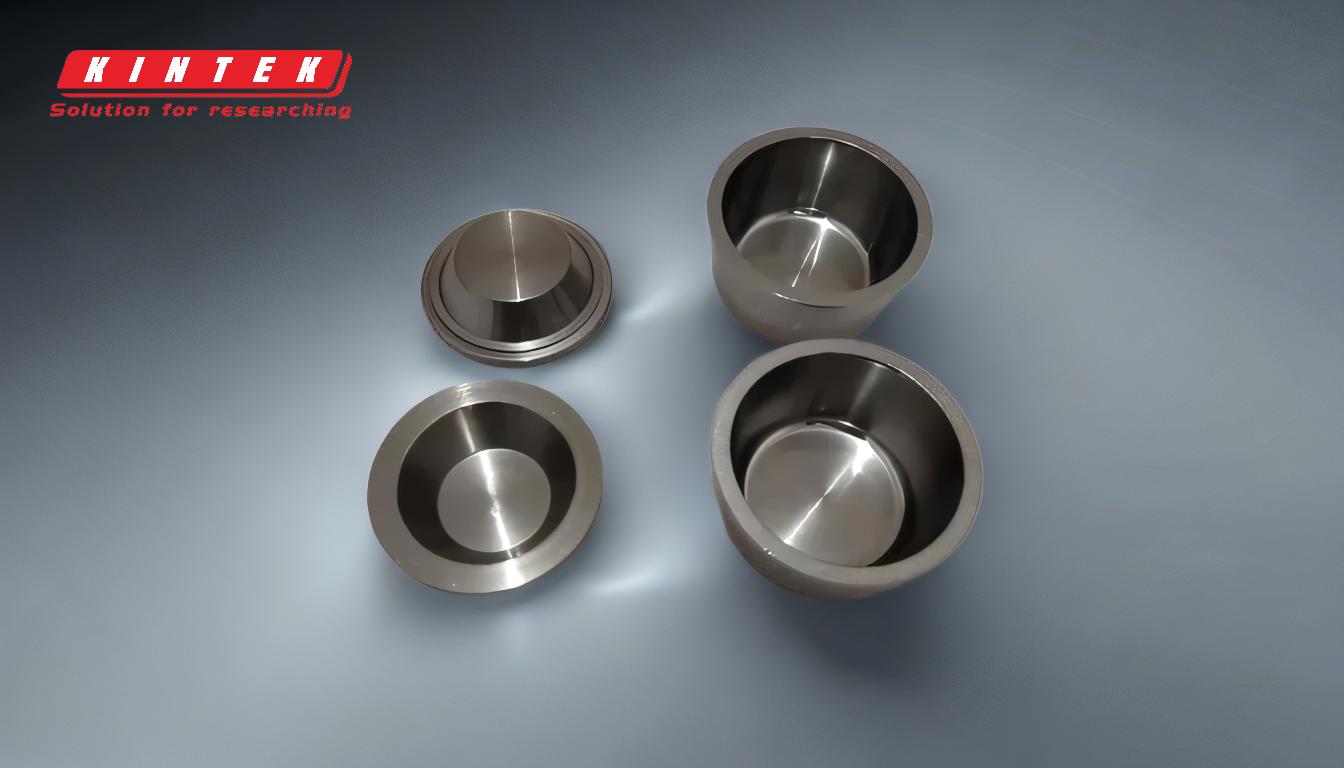
-
Versatility in Material Coating:
- Wide Range of Materials: Sputtering can coat a variety of materials, including plastics, organics, glass, and metals, at reduced temperatures. This versatility makes it suitable for diverse applications.
- High Melting Point Materials: Sputtering can deposit materials with very high melting points that are difficult or impossible to evaporate using other methods.
-
Precision and Control:
- Molecular-Level Precision: Sputtering provides molecular-level precision, enabling the creation of pristine interfaces between materials and allowing for the tuning of film properties through precise control of process parameters.
- Atomic-Level Film Deposition: The technique allows for pure and accurate atomic-level film deposition, resulting in high-quality films.
-
Reproducibility and Automation:
- Reproducibility: Sputter deposition offers high reproducibility, which is crucial for consistent film quality across multiple batches.
- Simpler Process Automation: Compared to methods like E-Beam or thermal evaporation, sputtering is easier to automate, reducing the complexity and potential for human error in the deposition process.
-
Cost-Effectiveness:
- Relatively Inexpensive: Sputter deposition is relatively inexpensive compared to other deposition processes, making it a cost-effective choice for many applications.
-
Film Quality and Adhesion:
- Better Adhesion: Sputter-ejected atoms have higher kinetic energies than evaporated materials, resulting in better adhesion of the films to the substrate.
- Uniform Films: Sputtering produces more uniform films with higher packing densities, even at low temperatures.
-
Compatibility with Reactive Gases:
- Reactive Deposition: Sputtering can easily incorporate reactive gaseous species activated in plasma, allowing for the formation of oxide or nitride film layers of desired composition.
-
Low Maintenance and High Vacuum Compatibility:
- Maintenance-Free: Sputtering is a maintenance-free process, reducing downtime and operational costs.
- Ultrahigh Vacuum Applications: The technique is suitable for ultrahigh vacuum applications, which is essential for certain high-precision processes.
-
Advanced Processes:
- Epitaxial Growth: Sputtering supports advanced processes like epitaxial growth, which is crucial for creating high-quality crystalline films.
-
Kinetic Energy and Deposition Direction:
- Higher Kinetic Energy: Sputter-ejected atoms have significantly higher kinetic energies compared to evaporated materials, enhancing film adhesion and quality.
- Flexible Deposition Direction: Sputtering can be performed both bottom-up and top-down, providing flexibility in the deposition process.
-
Small Chamber Volume:
- Compact Setup: The sputter deposition chamber can have a small volume, which is advantageous for certain applications and can reduce the overall footprint of the deposition system.
In summary, the sputtering technique offers a comprehensive set of advantages that make it superior to other deposition methods in many scenarios. Its versatility, precision, cost-effectiveness, and ability to produce high-quality films with excellent adhesion and uniformity are key factors that contribute to its widespread use in various industries.
Summary Table:
Advantage | Description |
---|---|
Versatility | Coats a wide range of materials, including high-melting-point substances. |
Precision | Molecular-level accuracy for pristine interfaces and atomic-level deposition. |
Reproducibility | Ensures consistent film quality across multiple batches. |
Cost-Effectiveness | Relatively inexpensive compared to other deposition methods. |
Film Quality | Better adhesion, uniform films, and higher packing densities. |
Low Maintenance | Maintenance-free process, reducing operational costs. |
Advanced Processes | Supports epitaxial growth and reactive deposition for high-quality films. |
Flexible Deposition | Can be performed in both bottom-up and top-down directions. |
Compact Setup | Small chamber volume reduces system footprint. |
Ready to leverage the benefits of sputtering for your applications? Contact us today to learn more!