Powder metallurgy (PM) is a versatile manufacturing process with a wide range of applications across various industries. It is particularly valued for its ability to produce small, complex parts with high precision, cost efficiency, and minimal waste. PM is used in industries such as automotive, aerospace, food equipment, and industrial tooling, where it enables the creation of durable, high-performance components. Its advantages include energy efficiency, material versatility, and the ability to produce parts with unique material combinations. PM is also increasingly being adopted in advanced applications like electric vehicle engines, where affordability and high production rates are critical.
Key Points Explained:
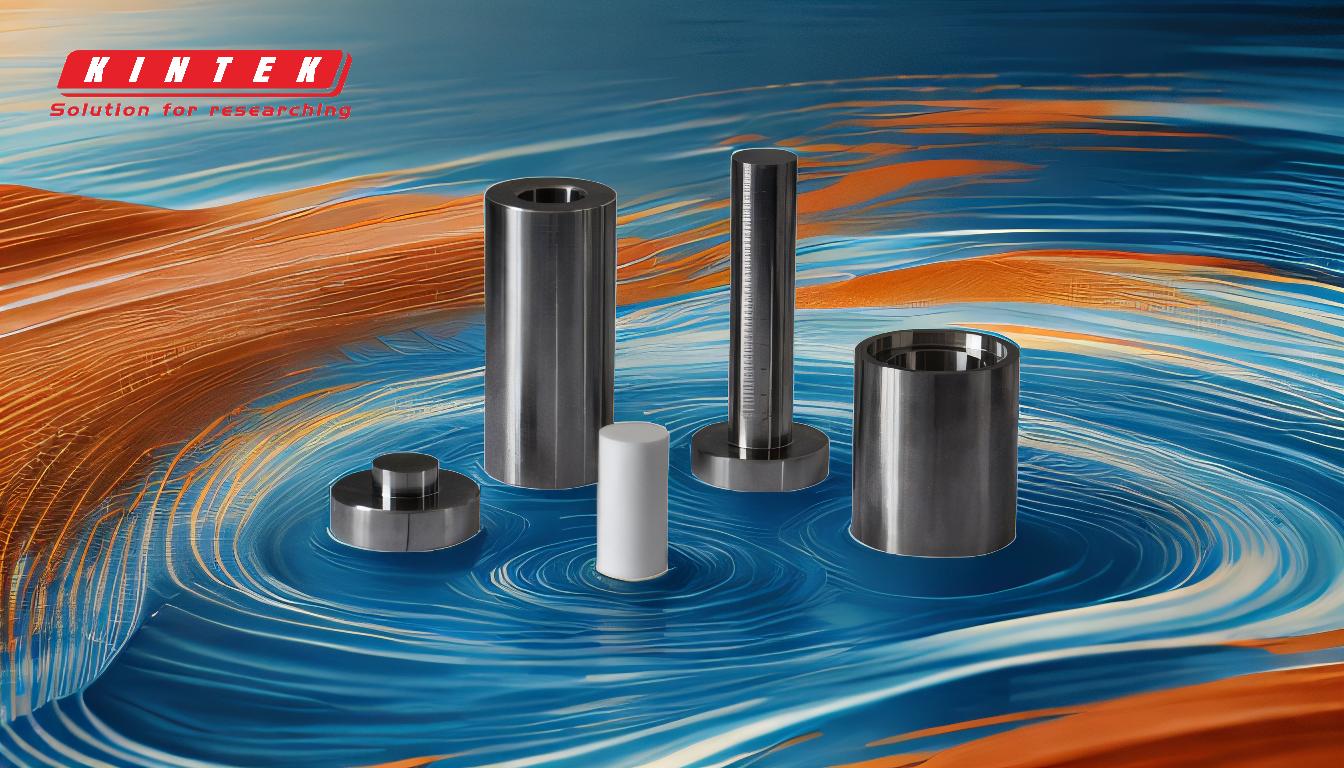
-
Automotive Industry:
- Exhaust Systems: PM is ideal for producing stainless steel components used in exhaust systems due to their high-temperature resistance and durability.
- Electric Engines: The technology is increasingly used in electric vehicle engines, where affordability, high production rates, and unique metal combinations are essential.
- General Components: PM is widely used to manufacture intricate parts like gears, bearings, and filters, which require high precision and cost efficiency.
-
Aerospace Industry:
- High-Performance Parts: PM is used to produce lightweight, high-strength components for aircraft, such as turbine blades and structural parts, which require exceptional tolerances and durability.
- Material Versatility: The ability to combine different metals and alloys makes PM suitable for aerospace applications where specific material properties are critical.
-
Industrial Tooling:
- Tungsten Carbide: PM is used to produce tungsten carbide, a material widely used in cutting and forming tools. Approximately 50,000 tonnes of tungsten carbide are produced annually using PM.
- Diamond Tools: PM is also used to manufacture diamond tools, which are essential for cutting and grinding applications in various industries.
-
Filters and Bearings:
- Sintered Filters: PM is used to produce porous filters for applications like hot polymer filtration and fluid purification.
- Oil-Impregnated Bearings: These bearings, made using PM, are self-lubricating and widely used in machinery and automotive applications.
-
Electrical and Electronic Components:
- Electrical Contacts: PM is used to manufacture electrical contacts, which require high conductivity and durability.
- Magnetic Materials: PM is also used to produce magnetic components for electronic devices.
-
Food Equipment:
- Surface Coatings: PM is used to apply hard coatings on food processing equipment to enhance durability and resistance to wear and corrosion.
- Custom Parts: The ability to produce complex, custom parts makes PM suitable for food equipment manufacturing.
-
Pressure Vessels:
- High-Strength Components: PM is used to produce components for pressure vessels, which require high strength and resistance to extreme conditions.
-
Environmental and Economic Benefits:
- Energy Efficiency: PM is a green manufacturing technology with a short process, low energy consumption, and minimal waste (97% of the material is used in the final product).
- Cost Efficiency: The process is economical for high-volume production, making it suitable for industries like automotive and aerospace.
-
Material Customization:
- Unique Combinations: PM allows for the creation of materials with tailored properties, such as specific hardness, conductivity, or thermal resistance, making it suitable for advanced applications.
-
Emerging Applications:
- Additive Manufacturing: PM is increasingly being integrated with additive manufacturing techniques to produce complex, custom parts with high precision.
- Green Technology: As a sustainable manufacturing method, PM is gaining traction in industries focused on reducing environmental impact.
In summary, powder metallurgy is a highly adaptable and efficient manufacturing process with applications ranging from automotive and aerospace to industrial tooling and food equipment. Its ability to produce complex, high-performance parts with minimal waste and energy consumption makes it a key technology in modern manufacturing.
Summary Table:
Industry | Key Applications |
---|---|
Automotive | Exhaust systems, electric engines, gears, bearings, filters |
Aerospace | Turbine blades, structural parts, lightweight high-strength components |
Industrial Tooling | Tungsten carbide, diamond tools, cutting and forming tools |
Filters & Bearings | Sintered filters, oil-impregnated bearings |
Electrical | Electrical contacts, magnetic materials |
Food Equipment | Surface coatings, custom parts for food processing |
Pressure Vessels | High-strength components for extreme conditions |
Emerging Trends | Additive manufacturing, green technology integration |
Learn how powder metallurgy can transform your manufacturing process—contact us today!