Atomic Layer Deposition (ALD) is a highly precise thin film deposition technique, but it faces several challenges that impact its efficiency, scalability, and application range. Key challenges include temperature limitations, stress generation during cooling, and the need to balance deposition rates with material properties. Additionally, issues such as uniformity, contamination, substrate compatibility, and cost-effectiveness further complicate its use. Addressing these challenges requires optimization of process parameters, material selection, and equipment design to enhance performance and expand its industrial applicability.
Key Points Explained:
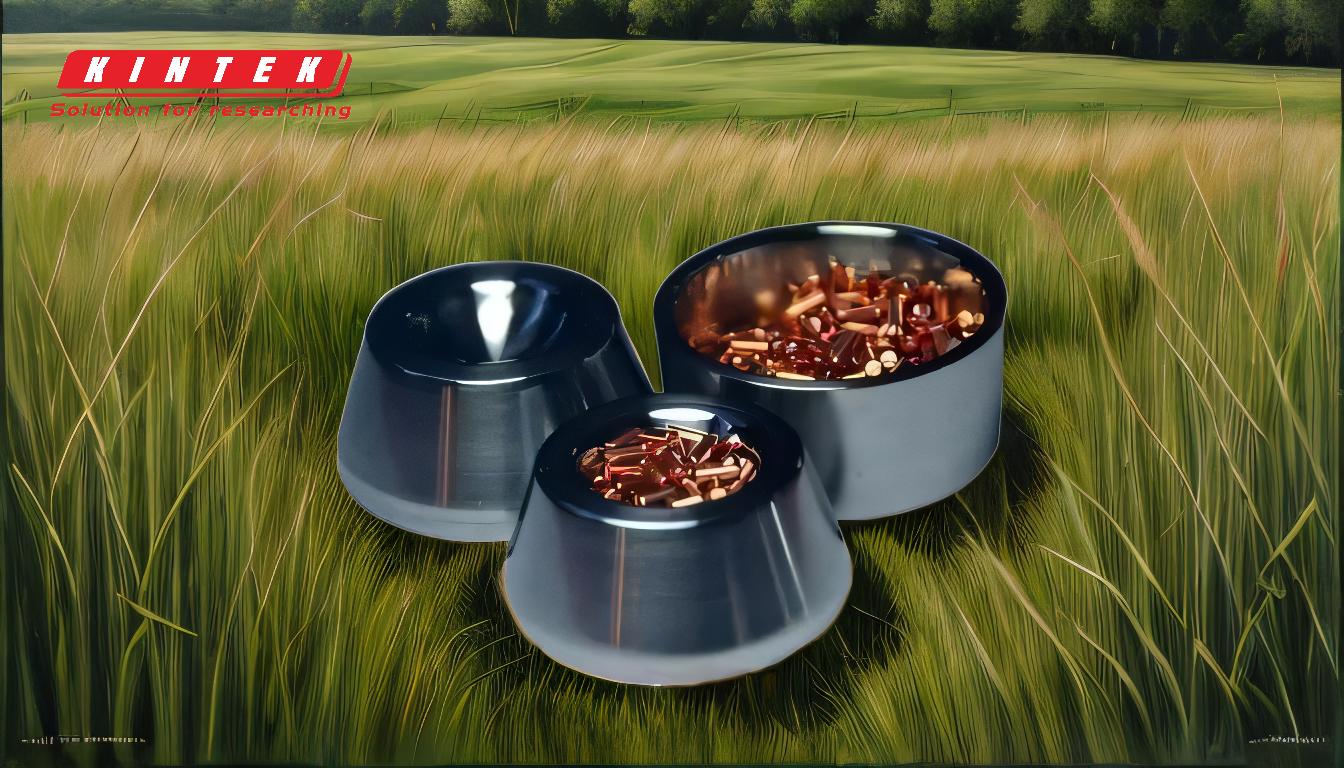
-
Temperature Limitations During Deposition:
- ALD processes often require specific temperature ranges to achieve optimal film quality and adhesion. However, some substrates or materials cannot withstand high temperatures, limiting their compatibility with ALD.
- High temperatures can also lead to undesirable chemical reactions or degradation of sensitive substrates, necessitating precise temperature control and the development of low-temperature ALD processes.
-
Undesirable Stresses Generated During Cooling:
- Thermal stresses can develop in thin films as they cool after deposition, leading to cracking, delamination, or other mechanical failures.
- These stresses are influenced by differences in thermal expansion coefficients between the film and substrate, as well as the cooling rate. Mitigating these stresses requires careful material selection and process optimization.
-
Optimizing Deposition Rates While Improving Material Properties:
- ALD is known for its slow deposition rates due to its layer-by-layer growth mechanism. Balancing the need for faster deposition with maintaining high-quality films is a significant challenge.
- Improving mechanical and tribological properties (e.g., hardness, wear resistance) without compromising deposition efficiency requires advanced precursor chemistry and process tuning.
-
Uniformity and Thickness Control:
- Achieving uniform film thickness across large or complex substrates is critical for consistent performance. Variations in thickness can lead to defects or performance degradation.
- Precise control over precursor dosing, purge times, and reactor design is essential to ensure uniformity.
-
Adhesion and Delamination Prevention:
- Proper adhesion between the film and substrate is crucial to prevent delamination, which can occur due to poor surface preparation, incompatible materials, or residual stresses.
- Surface treatments, such as plasma activation or the use of adhesion-promoting layers, can improve film-substrate bonding.
-
Minimizing Contamination:
- Contaminants from precursors, reactors, or the environment can degrade film quality and performance. Maintaining a clean deposition environment and using high-purity precursors are essential.
- In-situ monitoring and cleaning techniques can help reduce contamination risks.
-
Substrate Compatibility:
- Not all substrates are suitable for ALD due to their thermal, chemical, or mechanical properties. Developing ALD processes for a wider range of substrates, including flexible or sensitive materials, is an ongoing challenge.
- Surface modification or intermediate layers can sometimes improve compatibility.
-
Managing Stress and Strain:
- In addition to thermal stresses, intrinsic stresses from film growth can affect film integrity. Compressive or tensile stresses can lead to cracking, buckling, or other defects.
- Stress management techniques include adjusting deposition parameters, using stress-relieving layers, or post-deposition annealing.
-
Maintaining Film Purity and Composition:
- Achieving the desired chemical composition and purity is critical for functional films. Impurities or deviations from stoichiometry can alter electrical, optical, or mechanical properties.
- Precursor selection, reaction kinetics, and process conditions must be carefully controlled to ensure compositional accuracy.
-
Balancing Cost and Scalability:
- ALD is often more expensive than other deposition techniques due to its slow deposition rates, high-purity precursors, and specialized equipment.
- Scaling up ALD for industrial applications while reducing costs requires innovations in reactor design, precursor delivery systems, and process automation.
By addressing these challenges through research and development, ALD can continue to advance as a versatile and reliable thin film deposition technique for a wide range of applications, from microelectronics to energy storage and beyond.
Summary Table:
Challenge | Key Considerations |
---|---|
Temperature Limitations | Precise control, low-temperature processes, substrate compatibility |
Stress Generation During Cooling | Thermal expansion differences, cooling rate, material selection |
Deposition Rate vs. Material Quality | Advanced precursor chemistry, process tuning, mechanical properties |
Uniformity and Thickness Control | Precursor dosing, purge times, reactor design |
Adhesion and Delamination | Surface treatments, adhesion-promoting layers, substrate preparation |
Minimizing Contamination | High-purity precursors, in-situ monitoring, clean deposition environment |
Substrate Compatibility | Surface modification, intermediate layers, flexible material adaptation |
Managing Stress and Strain | Deposition parameter adjustments, stress-relieving layers, post-deposition annealing |
Film Purity and Composition | Precursor selection, reaction kinetics, process conditions |
Cost and Scalability | Reactor design innovations, precursor delivery systems, process automation |
Ready to optimize your ALD processes? Contact our experts today for tailored solutions!