Ceramic powders are classified based on their composition, particle size, and intended application. The primary classifications include oxides, non-oxides, and composite ceramics. Oxides like alumina and zirconia are widely used for their thermal and mechanical properties. Non-oxides, such as silicon carbide and boron nitride, are valued for their hardness and thermal conductivity. Composite ceramics combine different materials to achieve specific properties. Additionally, ceramic powders can be categorized by particle size, ranging from nano-sized to micro-sized powders, which influence the sintering behavior and final product characteristics. Understanding these classifications helps in selecting the right ceramic powder for specific industrial or research applications.
Key Points Explained:
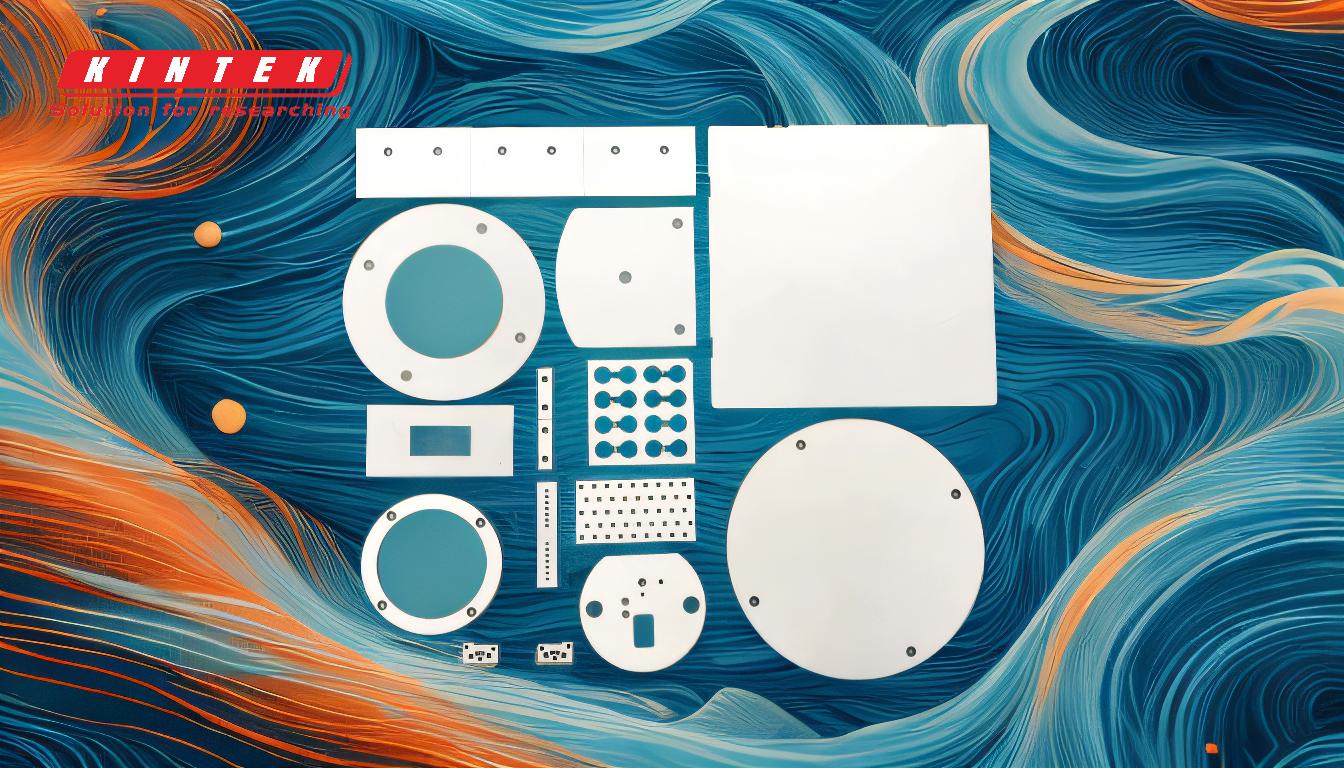
-
Classification by Composition:
- Oxides: These include materials like alumina (Al₂O₃) and zirconia (ZrO₂). Oxides are known for their high thermal stability, mechanical strength, and resistance to corrosion. They are commonly used in applications requiring durability and thermal insulation.
- Non-oxides: Examples are silicon carbide (SiC) and boron nitride (BN). Non-oxides are characterized by their exceptional hardness, thermal conductivity, and resistance to wear. They are often used in cutting tools, abrasives, and high-temperature applications.
- Composite Ceramics: These are engineered by combining different ceramic materials to achieve a balance of properties. For instance, a composite of alumina and zirconia can offer enhanced toughness and thermal shock resistance.
-
Classification by Particle Size:
- Nano-sized Powders: These powders have particles in the nanometer range (1-100 nm). They are used in applications requiring high surface area and reactivity, such as catalysts and advanced coatings.
- Micro-sized Powders: With particle sizes ranging from micrometers to millimeters, these powders are used in traditional ceramic manufacturing processes like pressing and sintering. The particle size affects the density and mechanical properties of the final product.
-
Classification by Application:
- Structural Ceramics: Used in applications where mechanical strength and durability are paramount, such as in engine components and cutting tools.
- Functional Ceramics: These are designed for specific functions like electrical insulation (e.g., alumina), piezoelectricity (e.g., lead zirconate titanate), or thermal management (e.g., silicon carbide).
- Bioceramics: Specifically designed for medical applications, such as dental implants and bone substitutes. Examples include hydroxyapatite and zirconia.
-
Influence of Particle Size on Sintering:
- Nano-sized Powders: Due to their high surface area, they sinter at lower temperatures, leading to finer microstructures and improved mechanical properties.
- Micro-sized Powders: Require higher sintering temperatures and can result in coarser microstructures, but they are easier to handle and process in traditional manufacturing setups.
-
Selection Criteria:
- Thermal Properties: Important for applications involving high temperatures, such as thermal barriers and heat exchangers.
- Mechanical Properties: Critical for structural applications where strength, hardness, and wear resistance are needed.
- Electrical Properties: Essential for electronic and electrical applications, including insulators and semiconductors.
- Biocompatibility: A key factor for medical applications, ensuring that the ceramic material is compatible with biological tissues.
Understanding these classifications and criteria is crucial for selecting the appropriate ceramic powder for specific applications, ensuring optimal performance and cost-effectiveness.
Summary Table:
Classification | Examples | Key Properties | Applications |
---|---|---|---|
By Composition | |||
- Oxides | Alumina (Al₂O₃), Zirconia | High thermal stability, mechanical strength, corrosion resistance | Thermal insulation, durable components |
- Non-oxides | Silicon Carbide (SiC), BN | Exceptional hardness, thermal conductivity, wear resistance | Cutting tools, abrasives, high-temperature applications |
- Composite Ceramics | Alumina-Zirconia | Enhanced toughness, thermal shock resistance | Engineered components requiring balanced properties |
By Particle Size | |||
- Nano-sized Powders | 1-100 nm | High surface area, reactivity, lower sintering temperatures | Catalysts, advanced coatings |
- Micro-sized Powders | Micrometers to millimeters | Easier handling, higher sintering temperatures, coarser microstructures | Traditional ceramic manufacturing |
By Application | |||
- Structural Ceramics | Alumina, Zirconia | Mechanical strength, durability | Engine components, cutting tools |
- Functional Ceramics | Alumina, SiC | Electrical insulation, piezoelectricity, thermal management | Electronics, thermal barriers |
- Bioceramics | Hydroxyapatite, Zirconia | Biocompatibility, bioinertness | Dental implants, bone substitutes |
Need help selecting the right ceramic powder for your application? Contact our experts today for personalized guidance!