Coatings for Scanning Electron Microscopy (SEM) are essential for analyzing non-conductive materials. These coatings prevent the accumulation of electrical charges caused by the high-energy electron beam, which can lead to image distortion, thermo-radiative degradation, and even material loss from the specimen. By applying a conductive or semi-conductive coating, the sample's surface becomes more stable, improving image quality and preserving the integrity of the material during analysis. Common coating materials include metals like gold, platinum, and chromium, as well as carbon, each chosen based on the specific requirements of the sample and the desired imaging resolution.
Key Points Explained:
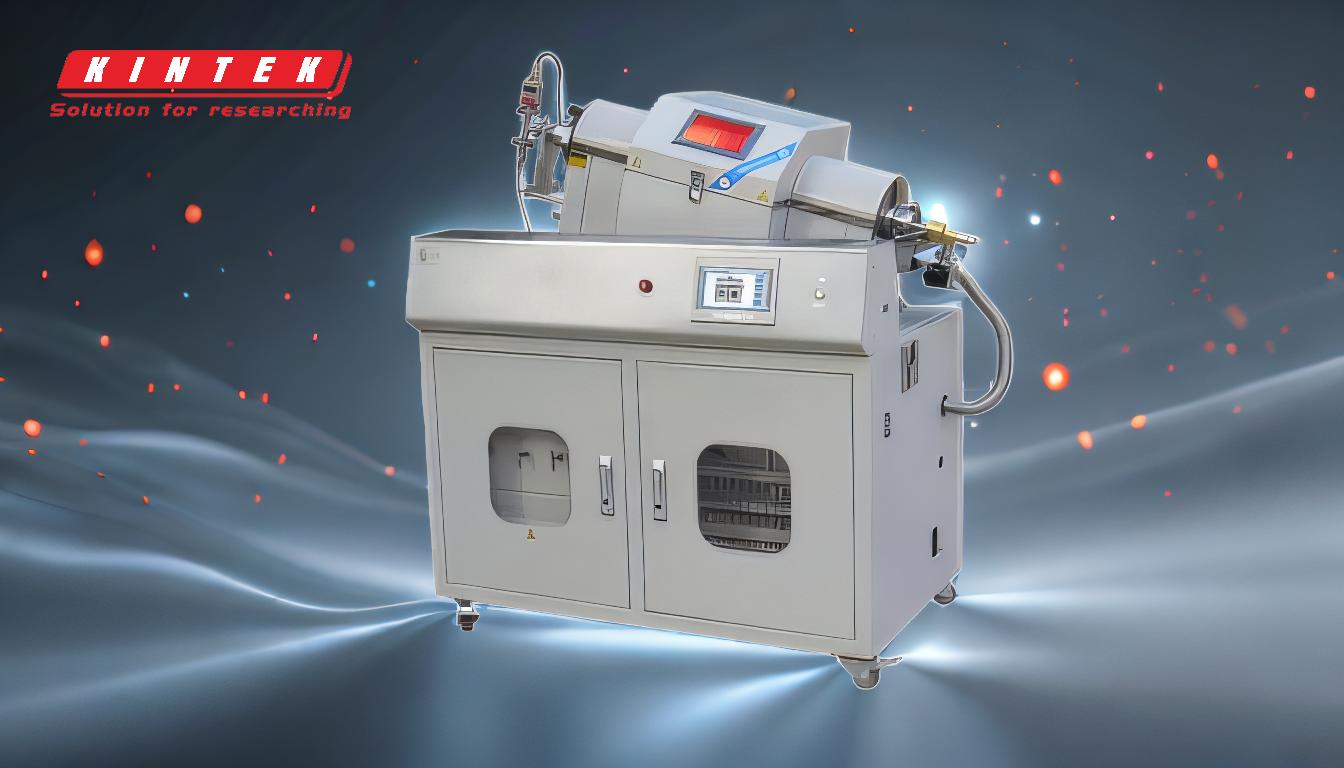
-
Purpose of SEM Coatings:
- SEM coatings are applied to non-conductive or poorly conductive materials to prevent charging effects caused by the electron beam.
- Charging effects can distort images, cause thermo-radiative damage, and lead to material loss, making coatings essential for accurate analysis.
-
Common Coating Materials:
- Gold (Au): A widely used coating material due to its high conductivity and ability to produce high-resolution images. It is ideal for general-purpose SEM imaging.
- Platinum (Pt): Offers finer grain size compared to gold, making it suitable for high-resolution imaging and reducing artifacts in the final image.
- Chromium (Cr): Provides excellent conductivity and is often used for samples requiring high-resolution imaging or energy-dispersive X-ray spectroscopy (EDS) analysis.
- Carbon (C): A semi-conductive coating that is particularly useful for EDS analysis, as it minimizes interference with elemental detection.
-
Coating Techniques:
- Sputter Coating: A common method where a thin layer of metal (e.g., gold or platinum) is deposited onto the sample using a sputtering process. This technique ensures uniform coverage and is suitable for most SEM applications.
- Evaporation Coating: Involves heating the coating material until it evaporates and then depositing it onto the sample. This method is less common but can be used for specific applications.
- Carbon Coating: Achieved through vacuum evaporation or sputtering, carbon coatings are ideal for samples requiring minimal interference with elemental analysis.
-
Factors Influencing Coating Choice:
- Sample Conductivity: Non-conductive samples require thicker or more conductive coatings to prevent charging.
- Imaging Resolution: High-resolution imaging often requires finer-grained coatings like platinum or chromium.
- Analytical Requirements: For EDS or other analytical techniques, carbon coatings are preferred to avoid interference with elemental detection.
- Sample Sensitivity: Some materials may be sensitive to heat or radiation, necessitating careful selection of coating materials and techniques.
-
Benefits of Using Coatings:
- Improved Image Quality: Coatings reduce charging effects, leading to clearer and more accurate SEM images.
- Sample Protection: Coatings minimize thermo-radiative damage and material loss, preserving the sample for further analysis.
- Enhanced Analytical Capabilities: Proper coatings enable better performance in techniques like EDS by reducing interference and improving signal detection.
-
Challenges and Considerations:
- Coating Thickness: Excessive coating can obscure fine details, while insufficient coating may not prevent charging. Optimal thickness depends on the sample and imaging requirements.
- Artifact Introduction: Improper coating techniques can introduce artifacts, such as uneven coating or graininess, which may affect image interpretation.
- Compatibility with Analysis: Some coatings may interfere with specific analytical techniques, requiring careful selection based on the intended use.
By understanding the role of coatings in SEM, selecting appropriate materials, and applying them using suitable techniques, researchers can achieve high-quality imaging and reliable analytical results while preserving sample integrity.
Summary Table:
Coating Material | Key Features | Best Use Cases |
---|---|---|
Gold (Au) | High conductivity, high-resolution imaging | General-purpose SEM imaging |
Platinum (Pt) | Finer grain size, reduces artifacts | High-resolution imaging |
Chromium (Cr) | Excellent conductivity, high-resolution imaging | EDS analysis |
Carbon (C) | Semi-conductive, minimal interference | EDS analysis, sensitive samples |
Coating Technique | Description | Applications |
---|---|---|
Sputter Coating | Uniform metal deposition | Most SEM applications |
Evaporation Coating | Heating and depositing coating material | Specific applications |
Carbon Coating | Vacuum evaporation or sputtering | EDS analysis, sensitive samples |
Need help selecting the right SEM coating for your samples? Contact our experts today for personalized guidance!