A 2-plate mold is a fundamental tool in injection molding, designed with two primary plates that form the core and cavity of the mold. These molds are widely used due to their simplicity and efficiency in producing plastic parts. The key components of a 2-plate mold include the return pin, sprues, ejector guide pin, and the core and cavity plates. Each component plays a critical role in ensuring the mold functions properly, from guiding the molten material into the cavity to ejecting the finished part accurately. Below, the components and their functions are explained in detail.
Key Points Explained:
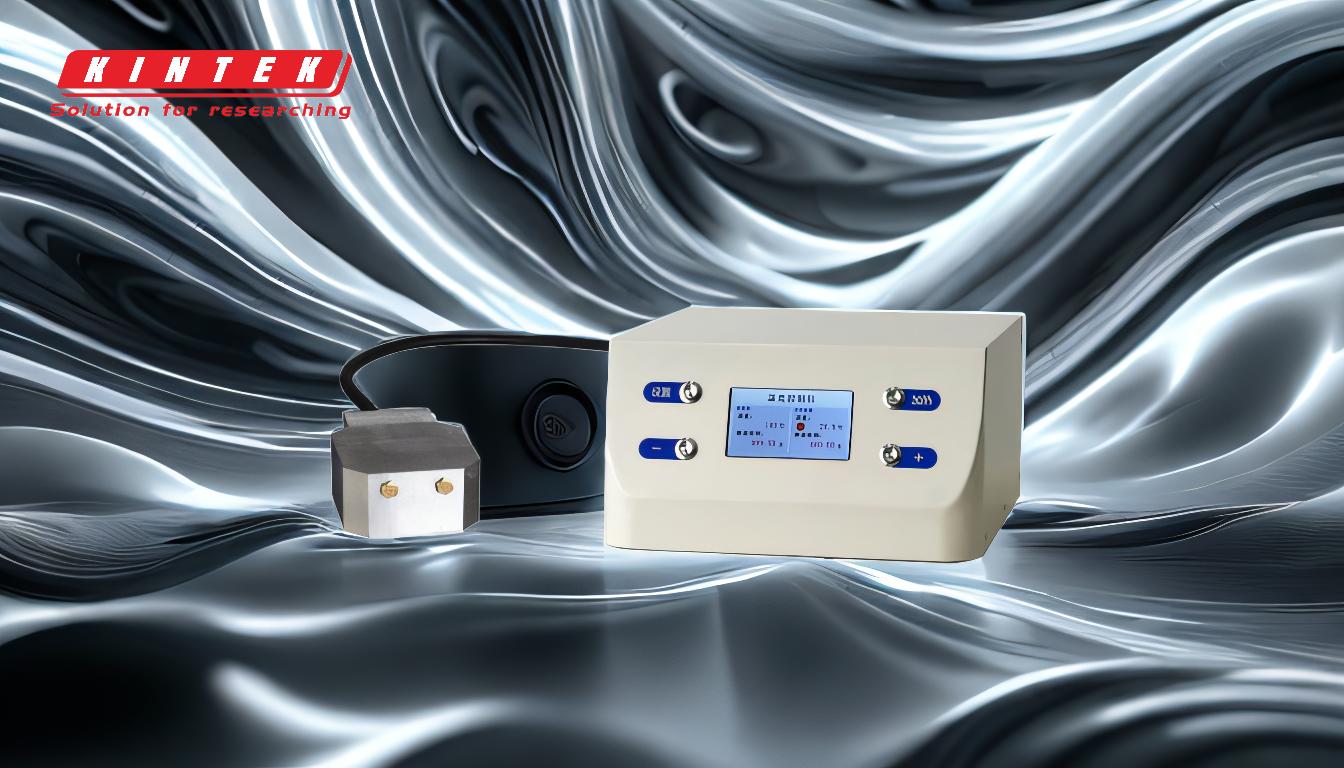
-
Core and Cavity Plates:
- These are the primary components of a 2-plate mold. The cavity plate holds the shape of the outer surface of the part, while the core plate forms the inner surface.
- The molten material is injected into the cavity, where it cools and solidifies to form the final product.
- These plates are precision-machined to ensure the part's dimensional accuracy and surface finish.
-
Return Pin:
- The return pin ensures that the ejector pins retract before the mold closes for the next cycle.
- This prevents damage to the mold and ensures smooth operation during repeated cycles.
- It is a critical safety feature that maintains the integrity of the mold and the ejection system.
-
Sprues:
- Sprues are channels that allow the molten material to flow from the injection molding machine into the mold cavity.
- They act as the entry point for the material and are designed to minimize pressure loss and ensure even filling of the cavity.
- After the part is ejected, the sprue is often trimmed away as part of the finishing process.
-
Ejector Guide Pin:
- The ejector guide pin ensures the accuracy of the ejection process by guiding the ejector pins.
- It helps maintain alignment during the ejection phase, preventing misalignment that could damage the part or the mold.
- This component is essential for maintaining consistent part quality and mold longevity.
-
Ejector Pins:
- Ejector pins are used to push the finished part out of the mold once it has cooled and solidified.
- They are strategically placed to apply even force and avoid distortion or damage to the part.
- The ejector pins work in conjunction with the ejector guide pin to ensure precise ejection.
-
Runner System:
- The runner system is a network of channels that distribute the molten material from the sprue to the cavities.
- It ensures that the material reaches all parts of the mold evenly, reducing the risk of defects like air pockets or incomplete filling.
- The design of the runner system is critical for optimizing material flow and minimizing waste.
-
Cooling Channels:
- Cooling channels are integrated into the mold to regulate the temperature during the molding process.
- They help solidify the molten material quickly and uniformly, reducing cycle time and improving part quality.
- Proper cooling is essential to prevent warping, shrinkage, or other defects in the final product.
-
Mold Base:
- The mold base is the structural framework that holds all the components of the mold together.
- It provides stability and alignment for the core and cavity plates, as well as other moving parts like the ejector system.
- The mold base is typically made from durable materials to withstand the high pressures and temperatures of the molding process.
-
Clamping Plate:
- The clamping plate secures the mold to the injection molding machine.
- It ensures that the mold remains firmly in place during the injection and cooling phases.
- Proper clamping is essential to prevent leaks or misalignment during the molding process.
-
Alignment Pins:
- Alignment pins ensure that the core and cavity plates are perfectly aligned when the mold closes.
- They prevent misalignment that could result in defects or damage to the mold.
- These pins are crucial for maintaining the precision and consistency of the molded parts.
By understanding these components and their functions, a purchaser can make informed decisions when selecting or evaluating a 2-plate mold for their specific application. Each component contributes to the mold's overall performance, ensuring high-quality production and efficient operation.
Summary Table:
Component | Function |
---|---|
Core and Cavity Plates | Forms the inner and outer surfaces of the molded part. |
Return Pin | Ensures ejector pins retract before the mold closes for the next cycle. |
Sprues | Channels molten material into the mold cavity. |
Ejector Guide Pin | Guides ejector pins for accurate part ejection. |
Ejector Pins | Pushes the finished part out of the mold. |
Runner System | Distributes molten material evenly to the cavities. |
Cooling Channels | Regulates mold temperature for uniform cooling and faster cycle times. |
Mold Base | Provides structural support and alignment for all mold components. |
Clamping Plate | Secures the mold to the injection molding machine. |
Alignment Pins | Ensures perfect alignment of core and cavity plates. |
Ready to optimize your injection molding process? Contact us today for expert advice on 2-plate molds!