A ball mill is a versatile grinding machine used to grind and blend materials for use in mineral dressing processes, paints, pyrotechnics, ceramics, and selective laser sintering. Its primary components include a hollow cylindrical shell that rotates about its axis, grinding media (balls), and a metallic frame. The cylinder is typically lined with abrasion-resistant materials, and the grinding media can vary in composition, such as steel, stainless steel, ceramic, or rubber. These components work together to break down coarse materials into fine particles through impact and attrition. Below, the key components and their roles are explained in detail.
Key Points Explained:
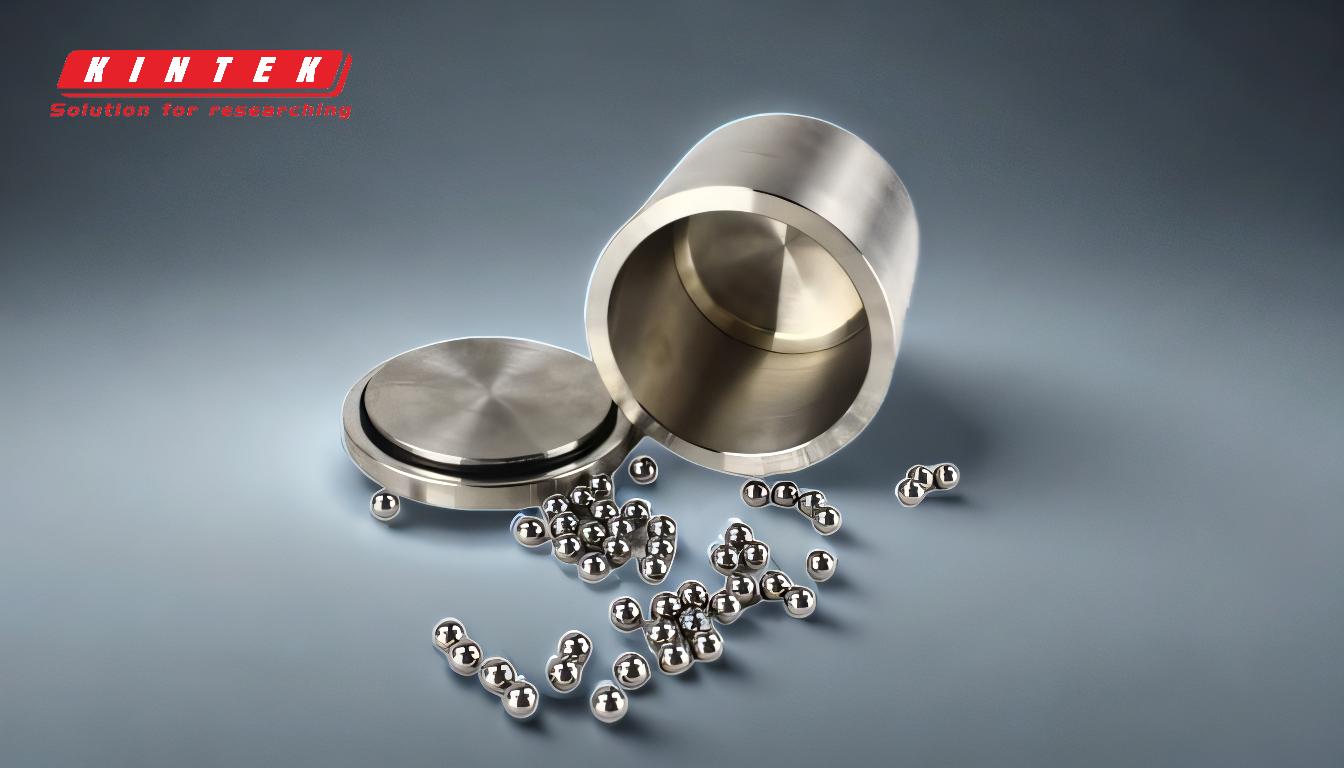
-
Cylindrical Shell:
- The cylindrical shell is the main body of the ball mill, typically made of hollow metal. It rotates about its horizontal or slightly inclined axis.
- Materials used for the shell include steel, porcelain, or rubber, depending on the application and the type of material being ground.
- The shell is often lined with abrasion-resistant materials like manganese steel or rubber to protect it from wear and tear caused by the grinding process.
-
Grinding Media (Balls):
- The grinding media are the balls inside the cylinder, which perform the actual grinding by impacting and crushing the material.
- These balls can be made of various materials, including steel, stainless steel, ceramic, or rubber, depending on the hardness and abrasiveness of the material being processed.
- The balls typically occupy 30 to 50% of the cylinder's volume, ensuring efficient grinding and reducing void spaces.
-
Metallic Frame:
- The metallic frame supports the cylindrical shell and allows it to rotate along its longitudinal axis.
- The frame must be robust and durable to withstand the rotational forces and the weight of the cylinder and grinding media.
-
Abrasion-Resistant Lining:
- The inner surface of the cylindrical shell is lined with abrasion-resistant materials to prolong the life of the mill.
- Common lining materials include manganese steel and rubber, chosen for their durability and resistance to wear.
-
Rotational Mechanism:
- The ball mill operates by rotating the cylindrical shell, which causes the grinding media to cascade and impact the material inside.
- The rotation can be horizontal or at a slight angle, depending on the design and application of the mill.
-
Feed and Discharge Mechanisms:
- The ball mill includes mechanisms for feeding material into the cylinder and discharging the ground product.
- These mechanisms ensure a continuous and efficient grinding process, allowing for the consistent production of fine particles.
-
Drive System:
- The drive system powers the rotation of the cylindrical shell.
- It typically consists of a motor, gearbox, and coupling, designed to provide the necessary torque and speed for effective grinding.
By understanding these components, a purchaser can make informed decisions about the type of ball mill required for specific applications, ensuring optimal performance and longevity of the equipment.
Summary Table:
Component | Description |
---|---|
Cylindrical Shell | Main body of the mill, made of steel, porcelain, or rubber, lined for durability. |
Grinding Media (Balls) | Balls made of steel, ceramic, or rubber for crushing and grinding materials. |
Metallic Frame | Supports the shell and handles rotational forces and weight. |
Abrasion-Resistant Lining | Protects the shell from wear, made of materials like manganese steel or rubber. |
Rotational Mechanism | Powers the shell's rotation for efficient grinding. |
Feed and Discharge | Ensures continuous material input and output for consistent grinding. |
Drive System | Includes motor, gearbox, and coupling to provide torque and speed. |
Need help choosing the right ball mill for your needs? Contact us today for expert advice!