The sieve method, while widely used for particle size analysis, has several notable disadvantages. These include limited resolution due to the restricted number of size fractions (typically up to 8 sieves), inefficiency with wet or cohesive particles, and a lower measurement limit of 50 µm. Additionally, sieve analysis can be time-consuming, and variations in mesh weave can lead to reproducibility issues. These limitations make the method less suitable for fine particle analysis or applications requiring high precision and consistency.
Key Points Explained:
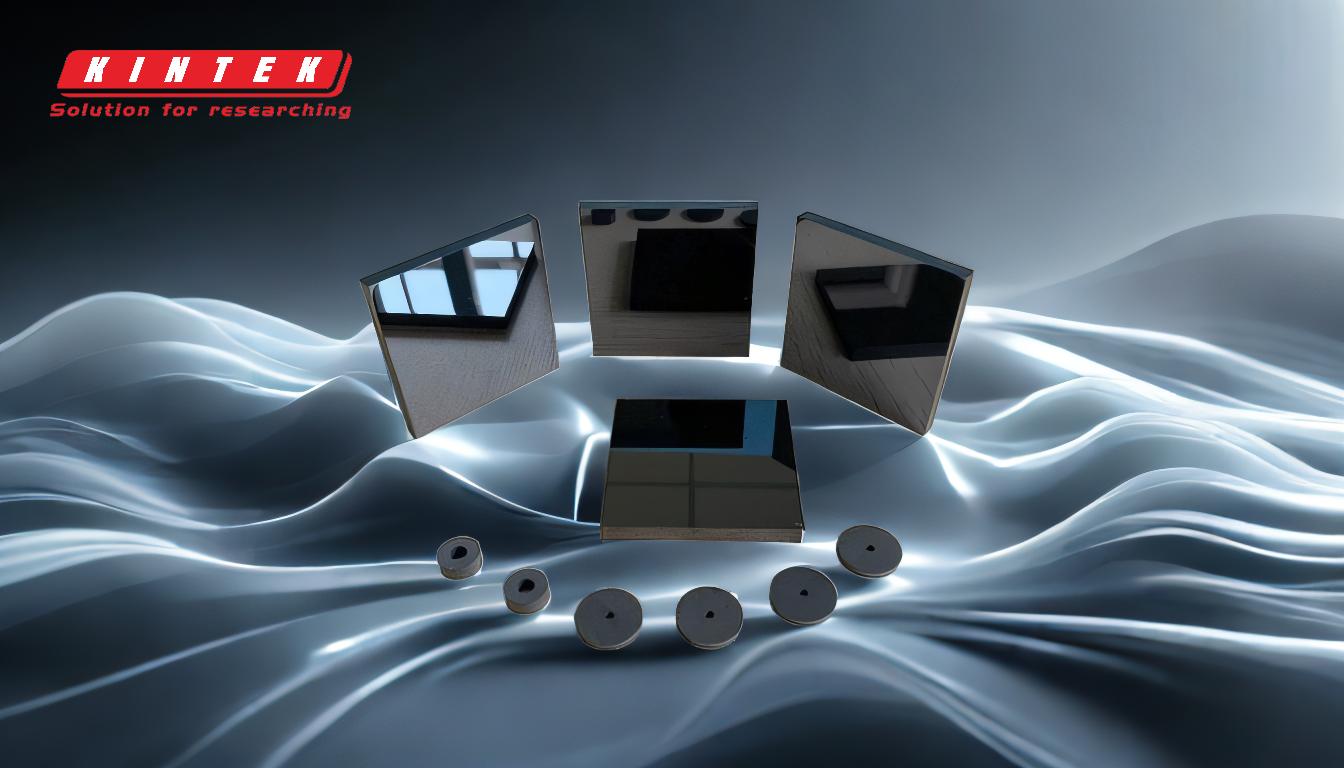
-
Limited Number of Size Fractions:
- The sieve method typically uses up to 8 sieves, which restricts the resolution of particle size distribution. This limitation means that the method cannot provide detailed information about the size distribution within each fraction, making it less suitable for applications requiring high granularity.
-
Ineffectiveness with Wet or Cohesive Particles:
- Sieve analysis is only effective with dry particles. Wet or cohesive particles can clog the sieve openings, leading to inaccurate results. This limitation makes the method unsuitable for materials that are naturally moist or sticky.
-
Minimum Measurement Limit:
- The sieve method has a lower measurement limit of 50 µm. Particles smaller than this size cannot be accurately measured using this technique. This limitation makes the method inadequate for analyzing fine powders or nanomaterials.
-
Time-Consuming Process:
- Sieve analysis can be a time-consuming process, especially when dealing with large sample sizes or materials that require extended shaking to achieve accurate separation. This inefficiency can be a significant drawback in high-throughput or time-sensitive applications.
-
Reproducibility Issues Due to Mesh Variations:
- Variations in the weave of the mesh material can affect the reproducibility of test results. These inconsistencies can lead to discrepancies in data, requiring careful calibration and adjustment in data presentation and analysis to account for these variations.
-
Limited Applicability for Fine Particle Analysis:
- Due to the minimum measurement limit and the limited number of size fractions, the sieve method is not well-suited for fine particle analysis. Other techniques, such as laser diffraction or dynamic light scattering, may be more appropriate for these applications.
-
Potential for Human Error:
- The manual nature of sieve analysis can introduce human error, particularly in the handling and shaking of sieves. This can lead to variations in results, further complicating data interpretation and analysis.
-
Maintenance and Calibration Requirements:
- Sieves require regular maintenance and calibration to ensure accurate results. Over time, the mesh can become worn or damaged, affecting the precision of the analysis. This ongoing requirement adds to the overall cost and effort associated with using the sieve method.
In summary, while the sieve method is a straightforward and widely used technique for particle size analysis, its limitations—such as restricted resolution, inefficiency with certain materials, and reproducibility issues—make it less suitable for applications requiring high precision or fine particle analysis. Understanding these disadvantages is crucial for selecting the appropriate method for specific analytical needs.
Summary Table:
Disadvantage | Description |
---|---|
Limited Number of Size Fractions | Up to 8 sieves restrict resolution, making it unsuitable for high granularity. |
Ineffectiveness with Wet or Cohesive Particles | Clogging of sieve openings leads to inaccurate results for moist or sticky materials. |
Minimum Measurement Limit (50 µm) | Particles smaller than 50 µm cannot be accurately measured. |
Time-Consuming Process | Extended shaking and large sample sizes increase analysis time. |
Reproducibility Issues | Mesh weave variations cause discrepancies in test results. |
Limited Applicability for Fine Particles | Not suitable for fine powders or nanomaterials. |
Potential for Human Error | Manual handling introduces variability in results. |
Maintenance and Calibration Requirements | Regular upkeep is needed to ensure accuracy, adding to costs. |
Need a more precise particle size analysis method? Contact our experts today to find the right solution for your needs!