Tungsten carbide is a highly versatile material known for its exceptional hardness, strength, wear resistance, and heat resistance. It is widely used in industrial applications such as cutting tools, mining equipment, and wear-resistant parts. However, despite its numerous advantages, tungsten carbide has certain drawbacks that limit its use in specific scenarios. These include its brittleness, high cost, difficulty in machining, and susceptibility to corrosion in certain environments. Understanding these limitations is crucial for making informed decisions when selecting materials for industrial or manufacturing purposes.
Key Points Explained:
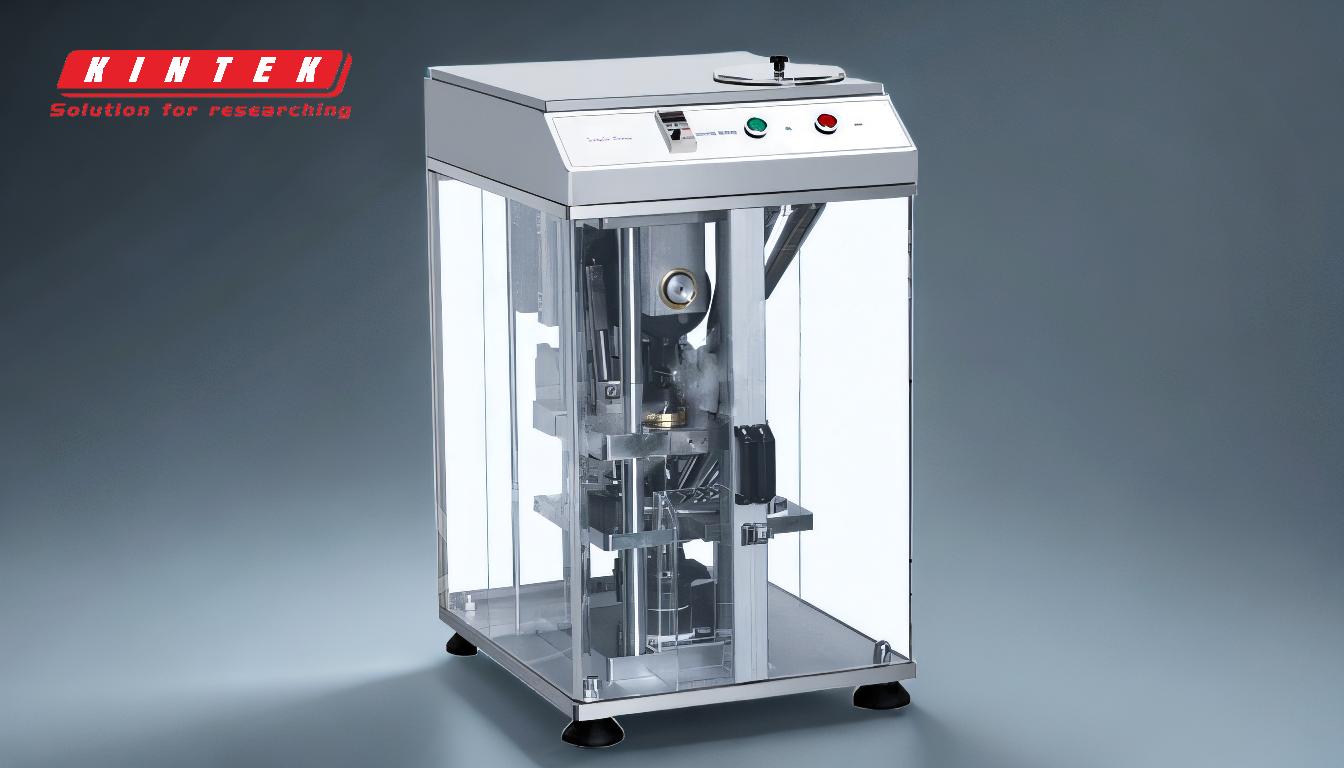
-
Brittleness:
- Tungsten carbide is extremely hard, but this hardness comes at the cost of brittleness. It is prone to cracking or chipping under high impact or stress, especially in applications involving sudden force or vibration.
- This makes it less suitable for dynamic or high-impact environments, where materials with higher toughness are preferred.
-
High Cost:
- The production of tungsten carbide involves complex processes, including the sintering of tungsten and carbon at high temperatures. This results in a higher cost compared to other materials like steel or ceramics.
- The expense of raw materials and manufacturing can make tungsten carbide less economical for large-scale applications or projects with tight budgets.
-
Difficulty in Machining:
- Due to its extreme hardness, tungsten carbide is challenging to machine or shape once it has been sintered. Specialized tools and techniques, such as grinding with diamond or cubic boron nitride abrasives, are required.
- This increases production time and costs, making it less practical for custom or intricate designs.
-
Susceptibility to Corrosion:
- While tungsten carbide is generally resistant to corrosion, it can degrade in certain environments, such as those containing strong acids or alkalis. This limits its use in chemical processing or marine applications.
- Protective coatings or alternative materials may be necessary in corrosive environments.
-
Limited Thermal Conductivity:
- Tungsten carbide has relatively low thermal conductivity compared to metals like copper or aluminum. This can lead to heat buildup in high-temperature applications, potentially affecting performance and durability.
- In applications requiring efficient heat dissipation, this limitation must be carefully considered.
-
Environmental and Health Concerns:
- The production and disposal of tungsten carbide can have environmental impacts, particularly due to the use of cobalt as a binding agent, which can pose health risks if inhaled or ingested.
- Proper handling and recycling practices are essential to mitigate these concerns.
-
Weight:
- Tungsten carbide is denser than many other materials, which can result in heavier components. This may be a disadvantage in applications where weight reduction is critical, such as aerospace or automotive industries.
By understanding these drawbacks, purchasers and engineers can make more informed decisions about when and where to use tungsten carbide, ensuring optimal performance and cost-effectiveness in their applications. For more information on related materials, you can explore the topic of tungsten coil.
Summary Table:
Drawback | Description |
---|---|
Brittleness | Prone to cracking or chipping under high impact or stress. |
High Cost | Expensive due to complex production processes and raw materials. |
Difficulty in Machining | Requires specialized tools and techniques, increasing production time and costs. |
Susceptibility to Corrosion | Degrades in environments with strong acids or alkalis. |
Limited Thermal Conductivity | Low heat dissipation, leading to potential heat buildup. |
Environmental Concerns | Cobalt binding agent poses health risks; requires proper handling and recycling. |
Weight | Denser material, making components heavier. |
Need help selecting the right material for your application? Contact our experts today for personalized advice!