A ball mill is a critical piece of equipment used in grinding and blending materials in various industries. Its primary components include the cylinder, grinding media (balls), and liners. The cylinder is a hollow, rotating structure made from durable materials like metal, porcelain, or rubber, and it houses the grinding media. The grinding media, typically steel, stainless steel, ceramic, or rubber balls, occupy 30-50% of the cylinder's volume and are responsible for the grinding action. The inner surface of the cylinder is often lined with abrasion-resistant materials like manganese steel or rubber to protect the cylinder and enhance efficiency. These elements work together to ensure effective grinding and durability.
Key Points Explained:
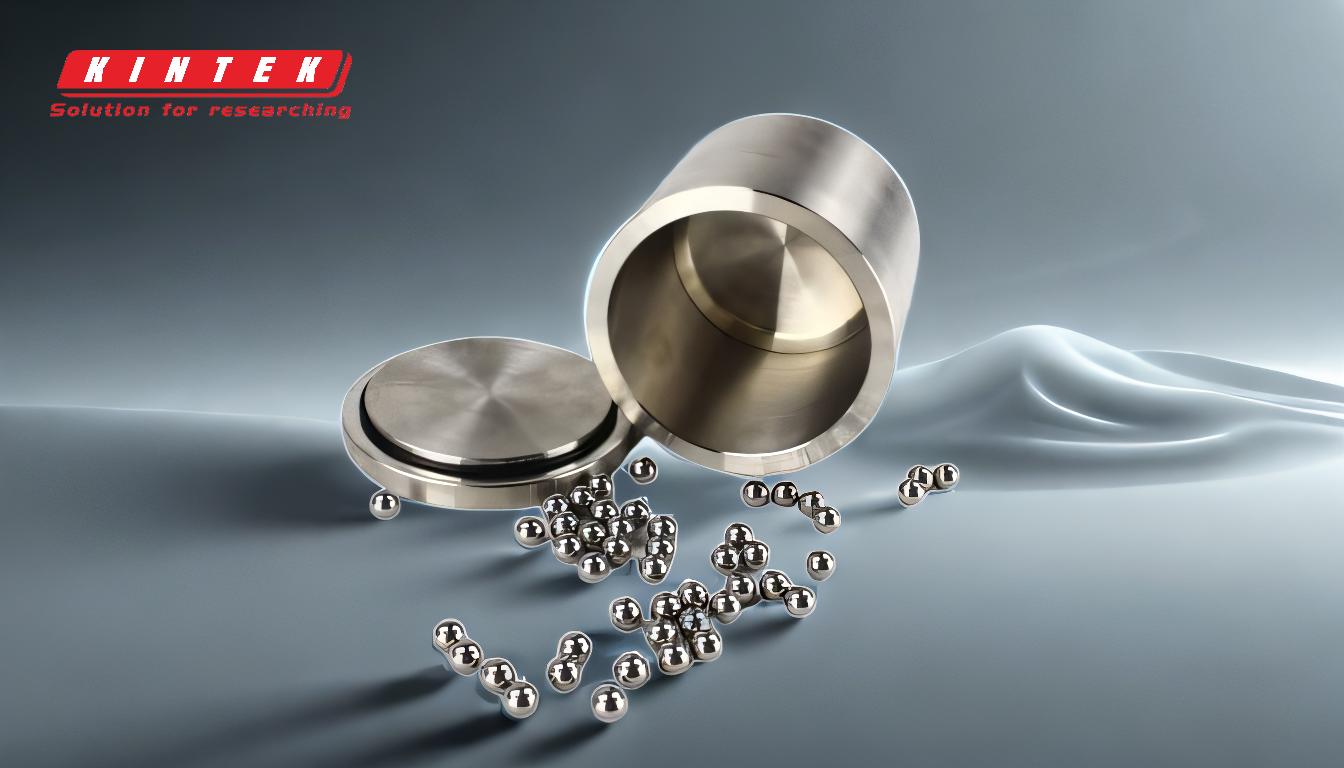
-
Cylinder:
- The cylinder is the primary structure of the ball mill, forming a hollow shell that rotates about its axis.
- It is typically made from durable materials such as metal, porcelain, or rubber, depending on the application and the material being processed.
- The cylinder's rotation is either horizontal or at a slight angle, which facilitates the grinding process by causing the grinding media to cascade and impact the material.
-
Grinding Media (Balls):
- The grinding media, usually in the form of balls, are the key components responsible for the grinding action.
- These balls are made from materials like steel, stainless steel, ceramic, or rubber, chosen based on the hardness and abrasiveness of the material being ground.
- The balls occupy 30-50% of the cylinder's volume, ensuring sufficient contact with the material for effective grinding.
-
Liners:
- The inner surface of the cylinder is lined with abrasion-resistant materials such as manganese steel or rubber.
- Liners protect the cylinder from wear and tear caused by the grinding media and the material being processed.
- They also enhance the efficiency of the grinding process by providing a smooth or textured surface that optimizes the movement of the grinding media.
-
Rotation Mechanism:
- The cylinder rotates about its axis, either horizontally or at a slight angle, driven by a motor or other power source.
- This rotation causes the grinding media to cascade and impact the material, breaking it down into smaller particles.
- The speed of rotation is carefully controlled to ensure optimal grinding efficiency without causing excessive wear or damage to the components.
-
Material Selection:
- The choice of materials for the cylinder, grinding media, and liners depends on the specific application and the properties of the material being processed.
- For example, rubber liners are often used in applications where noise reduction is important, while manganese steel liners are preferred for their durability in high-abrasion environments.
-
Operational Considerations:
- The size and number of grinding balls, as well as the speed of rotation, are critical factors that influence the grinding efficiency and the final particle size of the material.
- Proper maintenance and regular inspection of the cylinder, liners, and grinding media are essential to ensure the longevity and optimal performance of the ball mill.
By understanding these key elements, one can appreciate the complexity and efficiency of a ball mill in various industrial applications. Each component plays a vital role in ensuring the effective grinding and blending of materials, making the ball mill an indispensable tool in many processes.
Summary Table:
Component | Description | Key Features |
---|---|---|
Cylinder | Hollow, rotating structure made of metal, porcelain, or rubber. | Durable, facilitates grinding via rotation. |
Grinding Media (Balls) | Steel, stainless steel, ceramic, or rubber balls for grinding action. | Occupies 30-50% of cylinder volume; ensures effective grinding. |
Liners | Abrasion-resistant materials (e.g., manganese steel, rubber) lining the cylinder. | Protects cylinder, enhances grinding efficiency. |
Rotation Mechanism | Driven by a motor, rotates cylinder horizontally or at a slight angle. | Controls grinding speed for optimal efficiency. |
Material Selection | Depends on application and material properties. | Rubber for noise reduction, manganese steel for durability in high-abrasion. |
Operational Considerations | Size, number of balls, and rotation speed influence grinding efficiency. | Regular maintenance ensures longevity and performance. |
Optimize your grinding process with the right ball mill—contact our experts today for tailored solutions!