Ball milling is a complex process influenced by a variety of factors that determine the efficiency, productivity, and quality of the grinding process. These factors include the physical and chemical properties of the material being ground, the design and operational parameters of the ball mill, and the characteristics of the grinding media. Understanding these factors is crucial for optimizing the milling process to achieve desired particle sizes and improve overall productivity. Key factors include drum dimensions, ball size and filling ratio, rotation speed, material properties, feed rate, and residence time.
Key Points Explained:
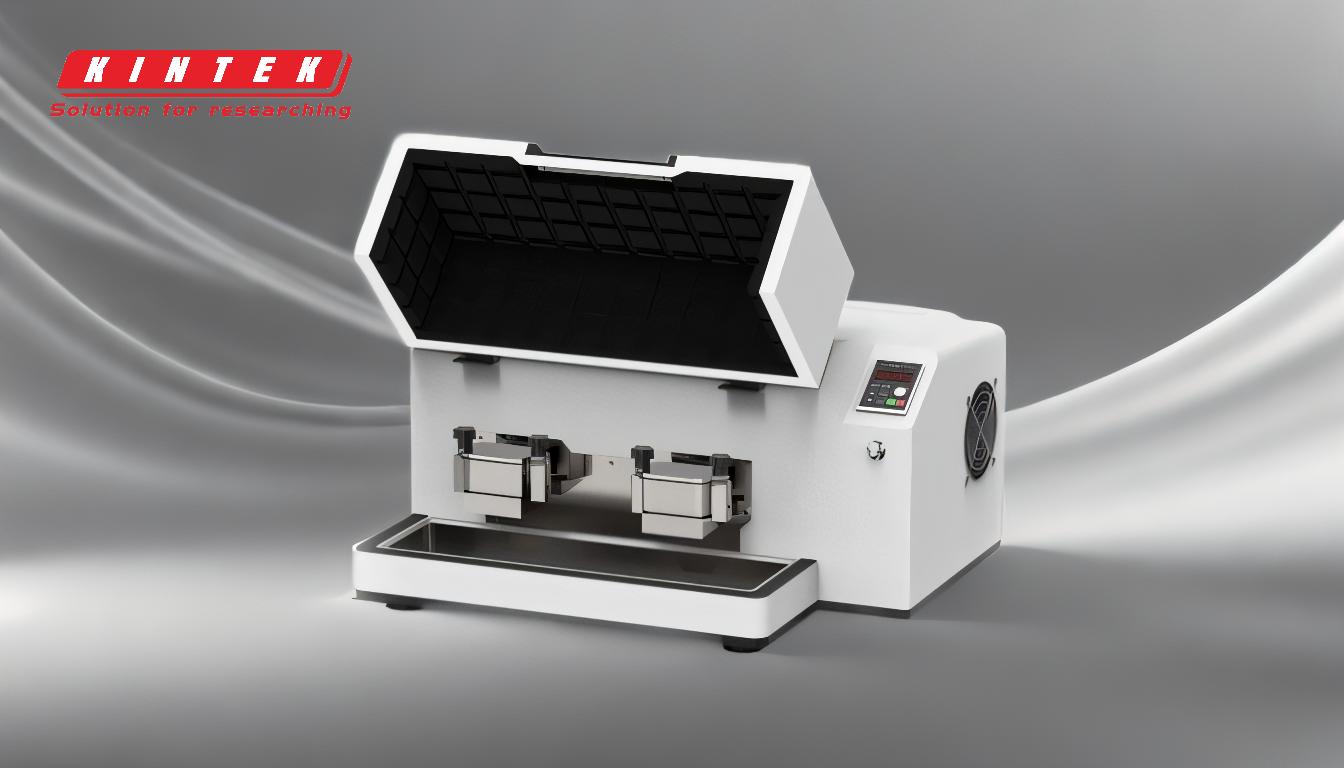
-
Drum Dimensions and Design:
-
Drum Diameter and Length-to-Diameter Ratio (L:D):
- The productivity of ball mills is significantly influenced by the drum diameter and the ratio of drum length to diameter. An optimal L:D ratio of 1.56–1.64 is recommended for efficient grinding. This ratio ensures a balance between the grinding action and the material's residence time in the mill.
- A larger drum diameter increases the grinding capacity, while the L:D ratio affects the distribution of grinding energy and the material's exposure to grinding media.
-
Drum Diameter and Length-to-Diameter Ratio (L:D):
-
Grinding Media (Balls):
-
Size and Density of Balls:
- The size and density of the grinding balls play a critical role in determining the grinding efficiency. Smaller balls are generally used for finer grinding, as they provide more contact points and higher surface area for grinding.
- The density of the balls affects the impact force during grinding. Higher density balls can deliver more energy to the material, leading to faster grinding.
-
Ball Filling Ratio:
- The filling ratio, or the percentage of the mill volume filled with grinding media, affects the grinding performance. An optimal filling ratio ensures sufficient grinding action without overloading the mill, which can reduce efficiency.
-
Size and Density of Balls:
-
Rotation Speed:
- The rotation speed of the drum is a critical factor in determining the grinding efficiency. At optimal speeds, the balls are lifted to a certain height before cascading down, creating a grinding action. If the speed is too low, the balls may not achieve the necessary height, reducing grinding efficiency. If the speed is too high, the balls may centrifuge, leading to ineffective grinding.
-
Material Properties:
-
Physical-Chemical Properties of Feed Material:
- The hardness, brittleness, and chemical composition of the material being ground influence the grinding process. Harder materials require more energy and time to grind, while brittle materials may fracture more easily.
-
Feed Rate and Level:
- The rate at which material is fed into the mill and the level of material in the vessel affect the residence time and grinding efficiency. Overloading the mill can reduce grinding efficiency, while underloading may lead to insufficient grinding.
-
Physical-Chemical Properties of Feed Material:
-
Residence Time:
- The residence time of the material in the mill chamber is crucial for achieving the desired fineness. Longer residence times allow for more grinding action, but excessive residence times can lead to over-grinding and energy inefficiency.
-
Armor Surface Shape:
- The shape and design of the mill's internal armor surface can influence the grinding process. Smooth surfaces may reduce wear on the mill but can also reduce grinding efficiency. Textured or lined surfaces can enhance grinding action by increasing friction and ball movement.
-
Milling Fineness and Product Removal:
- The desired fineness of the ground product affects the grinding time and energy consumption. Finer particles generally require longer grinding times and smaller grinding media.
- Timely removal of the ground product is essential to prevent over-grinding and to maintain optimal grinding conditions. Efficient product removal systems ensure continuous operation and consistent product quality.
By carefully controlling these factors, operators can optimize the ball milling process to achieve the desired particle size distribution, improve productivity, and reduce energy consumption. Each factor interacts with the others, so a holistic approach to process optimization is essential.
Summary Table:
Factor | Impact on Ball Milling |
---|---|
Drum Dimensions | Larger diameter increases capacity; optimal L:D ratio (1.56–1.64) ensures efficient grinding. |
Ball Size & Density | Smaller balls for finer grinding; higher density balls deliver more energy for faster grinding. |
Ball Filling Ratio | Optimal ratio ensures sufficient grinding action without overloading the mill. |
Rotation Speed | Optimal speed ensures effective grinding; too low or high speeds reduce efficiency. |
Material Properties | Hardness, brittleness, and chemical composition influence grinding time and energy. |
Feed Rate & Level | Affects residence time and grinding efficiency; overloading or underloading reduces performance. |
Residence Time | Longer times improve fineness but may lead to over-grinding and energy inefficiency. |
Armor Surface Shape | Textured or lined surfaces enhance grinding action by increasing friction and ball movement. |
Milling Fineness | Finer particles require longer grinding times and smaller grinding media. |
Product Removal | Timely removal prevents over-grinding and maintains consistent product quality. |
Ready to optimize your ball milling process? Contact our experts today for tailored solutions!