Grinding in a ball mill is a complex process influenced by multiple factors that determine the efficiency, particle size, and overall performance of the mill. Key factors include the speed of rotation, the size and type of grinding medium, the properties of the material being ground, the filling ratio of the mill, and the design parameters of the mill itself. These factors interact to affect the residence time, energy consumption, and final particle size distribution. Understanding and optimizing these variables is critical for achieving desired grinding outcomes, whether for fine particle production or efficient material processing.
Key Points Explained:
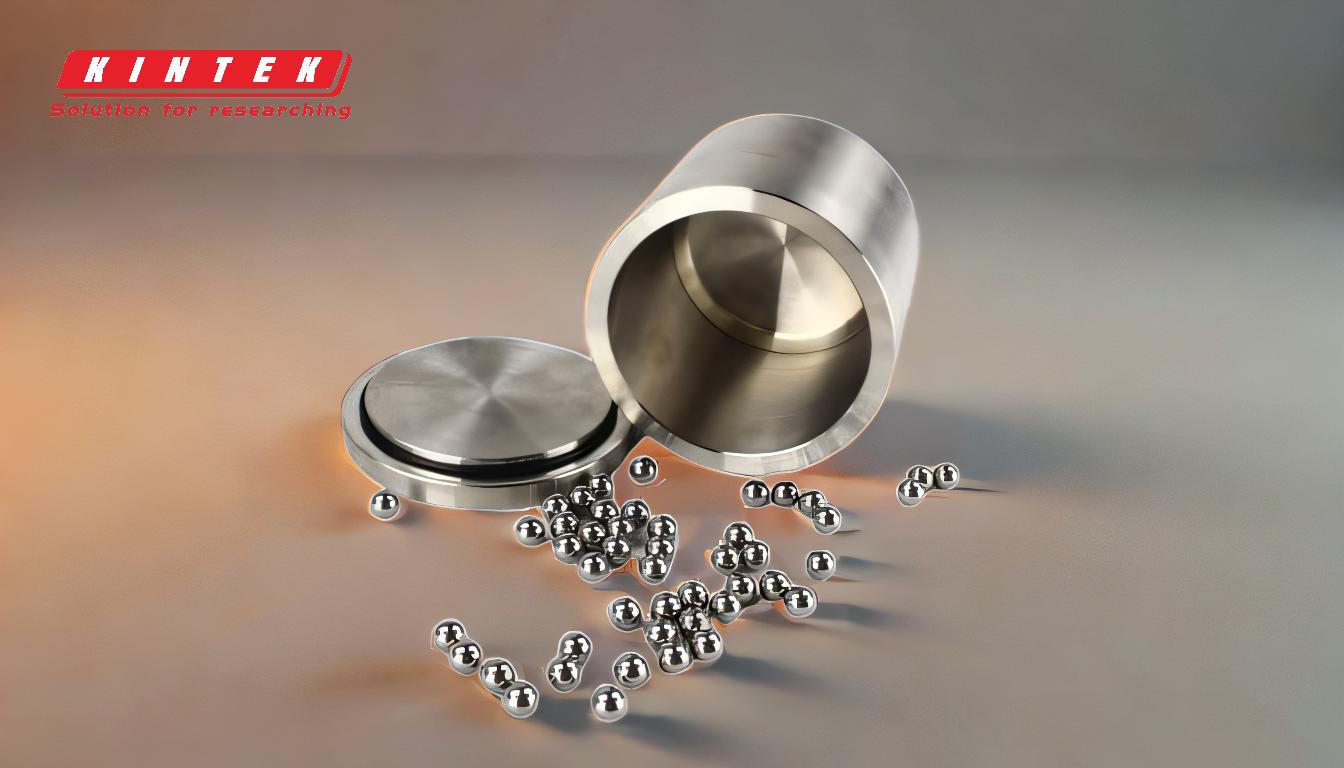
-
Speed of Rotation
- The rotation speed of the ball mill directly impacts the motion of the grinding media and the material.
- At optimal speeds, the balls are lifted to a certain height and then cascade down, creating impact and shear forces for grinding.
- If the speed is too low, the balls may not achieve sufficient height, reducing grinding efficiency.
- If the speed is too high, the balls may centrifuge, sticking to the walls and reducing grinding action.
- The critical speed (the speed at which centrifugation occurs) is a key parameter to avoid.
-
Size and Type of Grinding Medium
- The size of the grinding balls affects the energy transfer and particle size reduction.
- Larger balls are more effective for coarse grinding, while smaller balls are better for fine grinding.
- The density and hardness of the grinding media influence wear rates and grinding efficiency.
- Harder materials like steel or ceramic are preferred for longer lifespans and consistent performance.
- The number of balls also plays a role; too few balls reduce grinding efficiency, while too many can lead to overcrowding and reduced impact energy.
- The size of the grinding balls affects the energy transfer and particle size reduction.
-
Size and Type of Material to be Ground
- The initial particle size and hardness of the material significantly affect grinding performance.
- Harder materials require more energy and time to grind, while softer materials are easier to process.
- The feed rate and particle size distribution of the material must be optimized to avoid overloading the mill or creating uneven grinding.
- Materials with high moisture content or sticky properties may require adjustments to prevent clogging or reduced grinding efficiency.
- The initial particle size and hardness of the material significantly affect grinding performance.
-
Filling Ratio of the Mill
- The filling ratio refers to the percentage of the mill volume occupied by the grinding medium.
- An optimal filling ratio ensures efficient grinding without excessive energy consumption.
- Too low a filling ratio reduces the number of grinding impacts, lowering efficiency.
- Too high a filling ratio can lead to excessive collisions between balls, reducing their effectiveness.
- The filling ratio also affects the residence time of the material in the mill, influencing the final particle size.
-
Residence Time and Feed Rate
- Residence time is the duration the material spends inside the mill, which directly affects the degree of grinding.
- Longer residence times generally result in finer particles but may reduce throughput.
- The feed rate must be balanced with the mill's capacity to ensure consistent grinding and avoid overloading.
- Continuous monitoring and adjustment of feed rates are necessary to maintain optimal grinding conditions.
- Residence time is the duration the material spends inside the mill, which directly affects the degree of grinding.
-
Design Parameters of the Mill
- The drum diameter and length-to-diameter (L:D) ratio are critical design factors.
- An optimal L:D ratio (typically 1.56–1.64) ensures efficient grinding and energy utilization.
- The shape and texture of the mill's interior (armor surface) influence the motion of the grinding media and material.
- Proper ventilation and timely removal of ground product are essential to prevent overheating and maintain grinding efficiency.
- The drum diameter and length-to-diameter (L:D) ratio are critical design factors.
-
Physical-Chemical Properties of Feed Material
- The chemical composition, hardness, and abrasiveness of the material affect grinding performance.
- Abrasive materials may wear down grinding media faster, requiring more frequent replacements.
- The specific surface area and particle size distribution of the ground material are influenced by the material's properties.
- The chemical composition, hardness, and abrasiveness of the material affect grinding performance.
-
Number of Grinding Cycles
- Multiple grinding cycles may be required to achieve the desired particle size, especially for fine grinding.
- Each cycle increases the residence time and energy consumption but improves the uniformity of the final product.
-
Environmental and Operational Factors
- Temperature and humidity can affect grinding efficiency, particularly for materials sensitive to moisture.
- Proper maintenance and alignment of the mill ensure consistent performance and reduce downtime.
By carefully controlling and optimizing these factors, operators can achieve efficient grinding processes, reduce energy consumption, and produce high-quality ground materials with the desired particle size distribution.
Summary Table:
Factor | Impact |
---|---|
Speed of Rotation | Affects grinding media motion; optimal speed ensures efficient grinding. |
Grinding Medium Size/Type | Larger balls for coarse grinding, smaller for fine grinding; material hardness matters. |
Material Properties | Hardness, moisture, and feed rate influence grinding efficiency. |
Filling Ratio | Optimal ratio ensures efficient grinding without excessive energy use. |
Residence Time & Feed Rate | Longer residence time = finer particles; balanced feed rate avoids overloading. |
Mill Design Parameters | Drum diameter, L:D ratio, and interior texture impact grinding efficiency. |
Environmental Factors | Temperature, humidity, and maintenance affect performance and downtime. |
Optimize your ball mill process today—contact our experts for tailored solutions!