Particle size analysis by sieving is a widely used method for determining the size distribution of granular materials. However, several factors can influence the accuracy and reliability of the results. These factors include the material's properties, environmental conditions, equipment specifications, and operational procedures. Understanding these influences is crucial for obtaining consistent and accurate particle size measurements.
Key Points Explained:
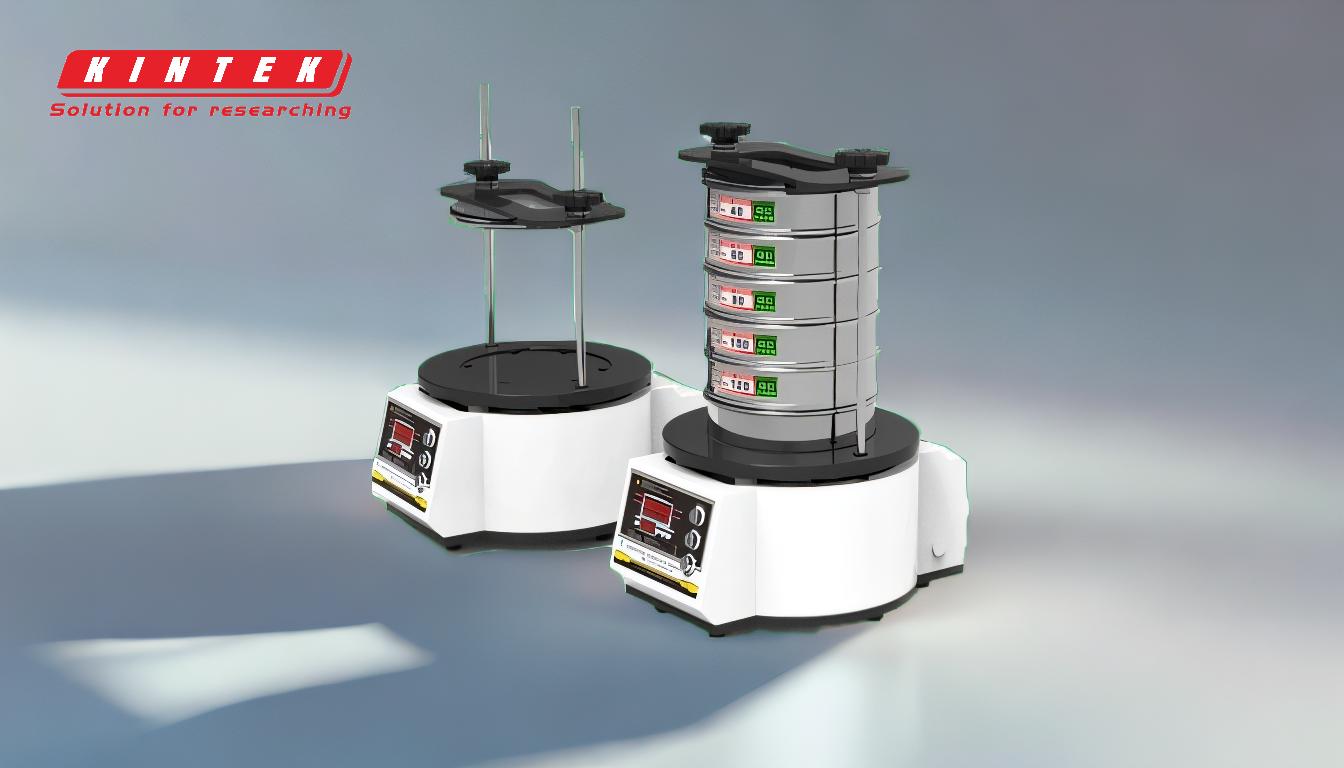
-
Material Properties:
- Particle Shape: Irregularly shaped particles may not pass through sieve openings as easily as spherical particles, leading to inaccurate size distribution.
- Particle Size Distribution: A wide range of particle sizes can cause overloading of the sieve, affecting the sieving efficiency.
- Moisture Content: High moisture content can cause particles to clump together, leading to inaccurate results. Conversely, extremely dry conditions can cause fine powders to adhere to sieve components due to electrostatic charges.
- Particle Density: Denser particles may settle differently during sieving, affecting the distribution.
-
Environmental Conditions:
- Relative Humidity: As mentioned in the reference, extremely dry conditions can cause fine powders to adhere to sieve components and each other due to strong electrostatic charges. High humidity can cause particles to clump together.
- Temperature: Temperature fluctuations can affect the material's properties, such as moisture content and particle adhesion.
-
Equipment Specifications:
- Sieve Mesh Size: The accuracy of the sieve mesh size is critical. Any deviation from the specified mesh size can lead to incorrect particle size analysis.
- Sieve Material: The material of the sieve can affect the sieving process. For example, metal sieves may be more durable but can introduce static charges, while plastic sieves may reduce static but wear out faster.
- Sieve Frame and Mesh Quality: Any damage or wear to the sieve frame or mesh can lead to inaccurate results.
-
Operational Procedures:
- Sieving Time: Insufficient sieving time may not allow all particles to pass through the appropriate sieve openings, while excessive sieving time can cause particle degradation.
- Sample Size: Overloading the sieve with too much sample can prevent proper separation of particles, leading to inaccurate results.
- Agitation Method: The method used to agitate the sieve (e.g., manual shaking, mechanical shaker) can affect the efficiency and consistency of the sieving process.
-
Human Factors:
- Operator Skill: The skill and experience of the operator can influence the accuracy of the sieving process. Inconsistent handling or incorrect interpretation of results can lead to errors.
- Calibration and Maintenance: Regular calibration and maintenance of sieving equipment are essential to ensure accurate and consistent results.
By carefully considering and controlling these factors, one can improve the accuracy and reliability of particle size analysis using the sieving method. Each factor plays a crucial role in the overall outcome, and understanding their interplay is essential for obtaining meaningful data.
Summary Table:
Factors | Key Influences |
---|---|
Material Properties | Particle shape, size distribution, moisture content, density |
Environmental Conditions | Relative humidity, temperature |
Equipment Specifications | Sieve mesh size, material, frame and mesh quality |
Operational Procedures | Sieving time, sample size, agitation method |
Human Factors | Operator skill, calibration, and maintenance |
Need help optimizing your particle size analysis? Contact our experts today for tailored solutions!