Sieve shakers are widely used in particle size analysis, but they come with certain hazards and limitations that can affect the accuracy and reliability of results. These include issues with handling fine materials, assumptions about particle shape, potential errors with elongated or flat particles, unsuitability for very small particles, and risks of sieve clogging or distortion. Proper handling and maintenance are crucial to mitigate these risks and ensure consistent performance.
Key Points Explained:
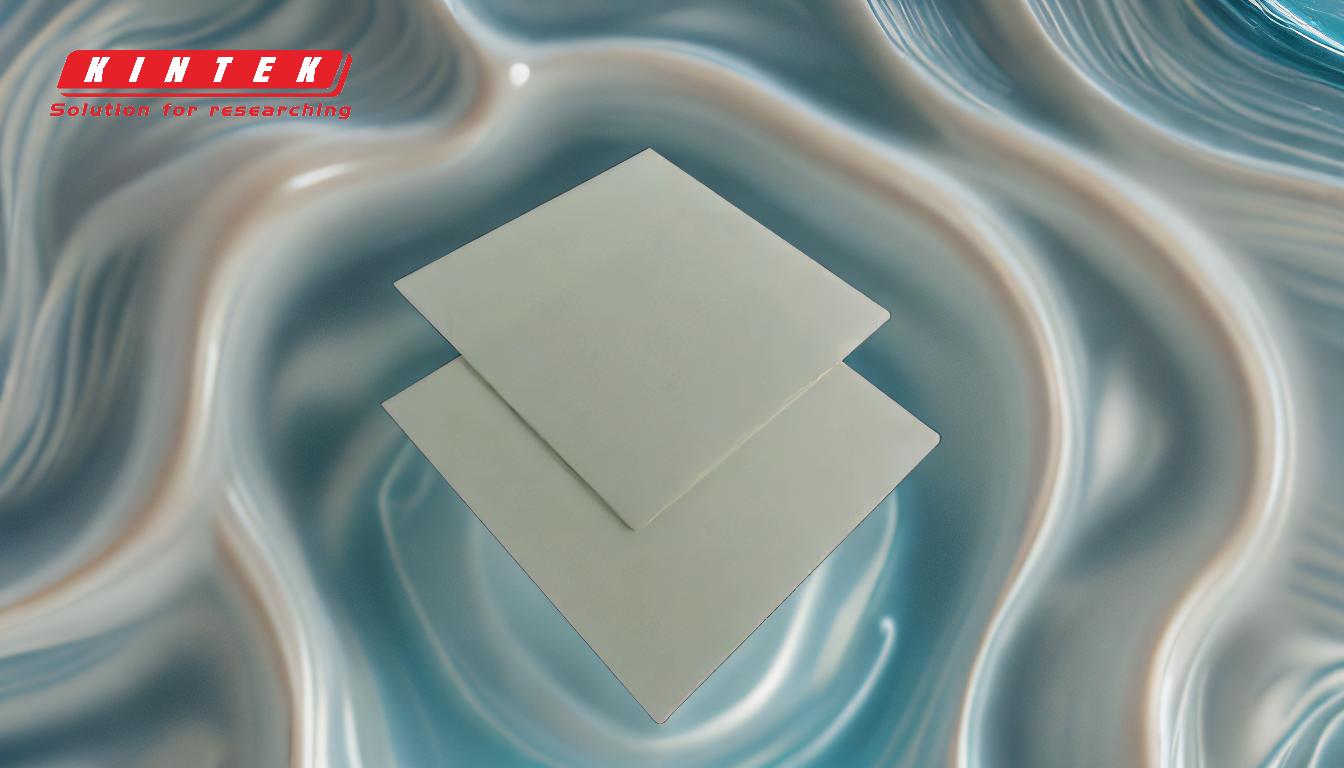
-
Reduced Accuracy for Fine Materials:
- Sieve shakers are less accurate for materials finer than 100 mesh (approximately 150 µm). This is because finer particles can clump together or adhere to the sieve mesh, leading to inaccurate size distribution measurements.
- For such materials, alternative methods like laser diffraction or sedimentation analysis may provide more reliable results.
-
Assumption of Particle Shape:
- Sieve analysis assumes that all particles are round or nearly spherical. However, many materials, such as elongated or flat particles, do not conform to this assumption. This can lead to errors in size classification, as non-spherical particles may pass through sieve openings differently than spherical ones.
-
Unreliable Results for Elongated and Flat Particles:
- Elongated or flat particles can cause mass-based results to be unreliable. These particles may align in a way that allows them to pass through sieve openings that would otherwise retain spherical particles of the same size, skewing the size distribution data.
-
Unsuitability for Very Small Particles (<50 µm):
- Sieve shakers are generally unsuitable for particles smaller than 50 µm. At this scale, factors like static electricity and particle adhesion can interfere with the sieving process, making it difficult to achieve accurate results.
-
Potential Particle Size Reduction:
- During the sieving process, particles may undergo further size reduction due to mechanical agitation. This can lead to errors in particle size analysis, as the measured size distribution may not reflect the original state of the material.
-
Sieve Clogging and Distortion:
- Improper handling or maintenance of sieves can lead to clogging or distortion of the mesh. Clogged sieves can result in inaccurate measurements, while distorted sieves can alter the effective opening size, further compromising results.
- Regular cleaning and inspection of sieves are essential to maintain their accuracy and longevity.
By understanding these hazards and limitations, users can take appropriate measures to minimize errors and ensure the reliability of sieve shaker results. This includes selecting the right equipment for the material being analyzed, adhering to proper maintenance protocols, and considering alternative methods when necessary.
Summary Table:
Hazard/Limitation | Description |
---|---|
Reduced Accuracy for Fine Materials | Less accurate for particles finer than 100 mesh (150 µm); clumping and adhesion can skew results. Alternative methods like laser diffraction recommended. |
Assumption of Particle Shape | Assumes particles are spherical; elongated or flat particles may pass through sieves differently, leading to errors in size classification. |
Unreliable Results for Flat Particles | Flat or elongated particles may align to pass through sieve openings, skewing mass-based results. |
Unsuitability for Very Small Particles | Not ideal for particles <50 µm; static electricity and adhesion can interfere with accuracy. |
Potential Particle Size Reduction | Mechanical agitation during sieving may reduce particle size, altering the original size distribution. |
Sieve Clogging and Distortion | Improper handling can lead to clogging or mesh distortion, compromising accuracy. Regular cleaning and inspection are essential. |
Ensure accurate particle size analysis—contact us today to learn how to optimize your sieve shaker performance!