Selecting a high vacuum pump involves evaluating a range of parameters to ensure the pump meets the specific requirements of the application. Key considerations include the intended use, which dictates the technology, lubrication, and chemical resistance needed. The desired vacuum level and flow rate are critical, as they determine the pump's performance. Other factors such as chemical compatibility, maintenance requirements, noise level, and cost also play a significant role. Additionally, the type of pump, motor speed, horsepower, hose barb size, and net weight are important attributes to consider. Proper selection ensures reliable functionality, longevity, and cost-effectiveness.
Key Points Explained:
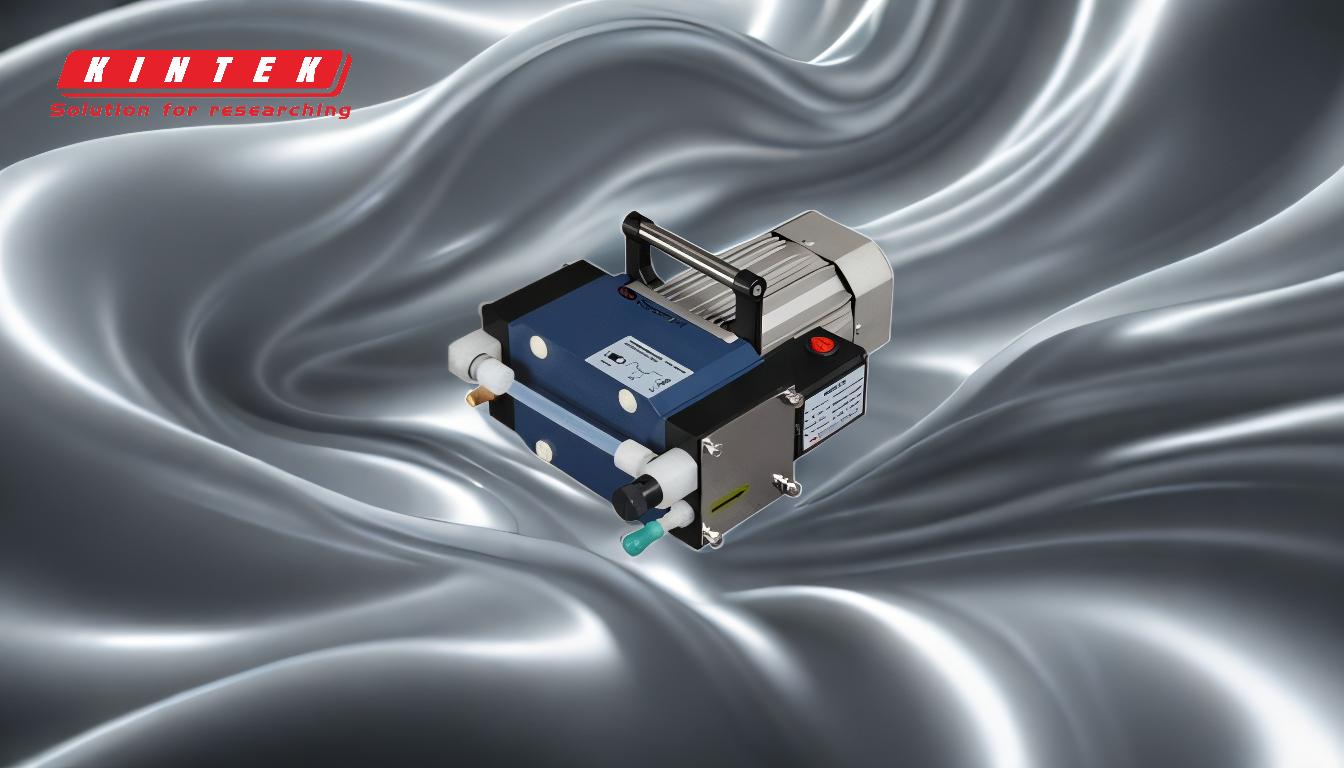
-
Intended Use and Application
- The specific application determines the type of vacuum pump required. For example, industrial applications may demand robust, high-flow pumps, while laboratory settings might require precise, low-noise pumps.
- Consider the environment (e.g., cleanroom, corrosive atmosphere) and the type of gas being pumped (e.g., inert, reactive, or hazardous).
-
Vacuum Level
- The desired vacuum level is a critical parameter. High vacuum pumps are designed to achieve lower pressures, so understanding the required ultimate vacuum (the lowest pressure the pump can achieve) is essential.
- Applications like semiconductor manufacturing or analytical instrumentation often require ultra-high vacuum levels.
-
Flow Rate (Pumping Speed)
- The flow rate, or pumping speed, determines how quickly the pump can evacuate a system. It is measured in liters per minute (L/min) or cubic meters per hour (m³/h).
- Match the flow rate to the volume of the system and the desired evacuation time.
-
Chemical Compatibility
- The pump must be compatible with the gases or vapors it will handle. For example, corrosive gases may require pumps made of chemically resistant materials like stainless steel or PTFE.
- Oil-sealed pumps may not be suitable for applications involving reactive gases, as the oil can degrade.
-
Lubrication (Oil-Free vs. Oil-Sealed)
- Oil-sealed pumps are common but require regular maintenance and oil changes. They are suitable for applications where contamination is not a concern.
- Oil-free pumps are ideal for cleanroom environments or applications where contamination must be minimized, such as in food processing or pharmaceuticals.
-
Maintenance Requirements
- Consider the ease of maintenance, including the frequency of oil changes, filter replacements, and other servicing needs.
- Low-maintenance pumps reduce downtime and operational costs.
-
Cost and Life Expectancy
- Evaluate the initial purchase cost, operational costs (e.g., energy consumption, maintenance), and the expected lifespan of the pump.
- High-quality pumps may have a higher upfront cost but can offer better long-term value due to reduced maintenance and longer life.
-
Motor Speed and Horsepower
- Motor speed (measured in RPM) and horsepower determine the pump's power and efficiency. Higher horsepower pumps can handle larger systems or achieve faster evacuation times.
- Ensure the motor is compatible with the available power supply.
-
Noise Level
- Noise level is an important consideration, especially in laboratory or office environments. Oil-free pumps tend to be quieter than oil-sealed pumps.
- Noise levels are typically measured in decibels (dB).
-
Hose Barb Size and Net Weight
- The hose barb size must match the tubing or piping used in the system to ensure a proper seal and efficient operation.
- Net weight is important for portability and installation, especially in applications where the pump may need to be moved frequently.
-
Pumping Pressure and Speed Ranges
- The pump's operating pressure range and speed should align with the application's requirements. For example, high-speed pumps are needed for rapid evacuation, while low-speed pumps may be sufficient for steady-state operations.
-
System Location and Environmental Factors
- Consider the physical location of the pump, including space constraints, ventilation, and ambient temperature.
- Environmental factors such as humidity, dust, and vibration can affect pump performance and longevity.
By carefully evaluating these parameters, you can select a high vacuum pump that meets your specific needs, ensuring optimal performance, reliability, and cost-effectiveness.
Summary Table:
Parameter | Key Considerations |
---|---|
Intended Use | Industrial or lab use, environment, type of gas pumped |
Vacuum Level | Required ultimate vacuum for applications like semiconductor manufacturing |
Flow Rate | Pumping speed (L/min or m³/h) to match system volume and evacuation time |
Chemical Compatibility | Material resistance to gases (e.g., stainless steel, PTFE) |
Lubrication | Oil-sealed vs. oil-free pumps for contamination control |
Maintenance | Frequency of oil changes, filter replacements, and servicing needs |
Cost and Life Expectancy | Initial cost, operational expenses, and expected lifespan |
Motor Speed and Power | RPM and horsepower for system compatibility and efficiency |
Noise Level | Decibel (dB) rating for quiet operation in labs or offices |
Hose Barb Size/Weight | Compatibility with tubing and portability for installation |
Environmental Factors | Space, ventilation, humidity, dust, and vibration considerations |
Need help selecting the perfect high vacuum pump? Contact our experts today for personalized guidance!