Sputtering is a widely used physical vapor deposition (PVD) technique with several advantages, such as the ability to deposit a wide range of materials, excellent film adhesion, high purity, and uniform thickness over large areas. However, it also has notable disadvantages, including high capital costs, relatively low deposition rates for certain materials, potential material degradation, and a tendency to introduce impurities. The choice between DC sputtering, RF sputtering, and other methods depends on the specific application, material properties, and desired outcomes. Each method has its unique pros and cons, making sputtering a versatile but complex process.
Key Points Explained:
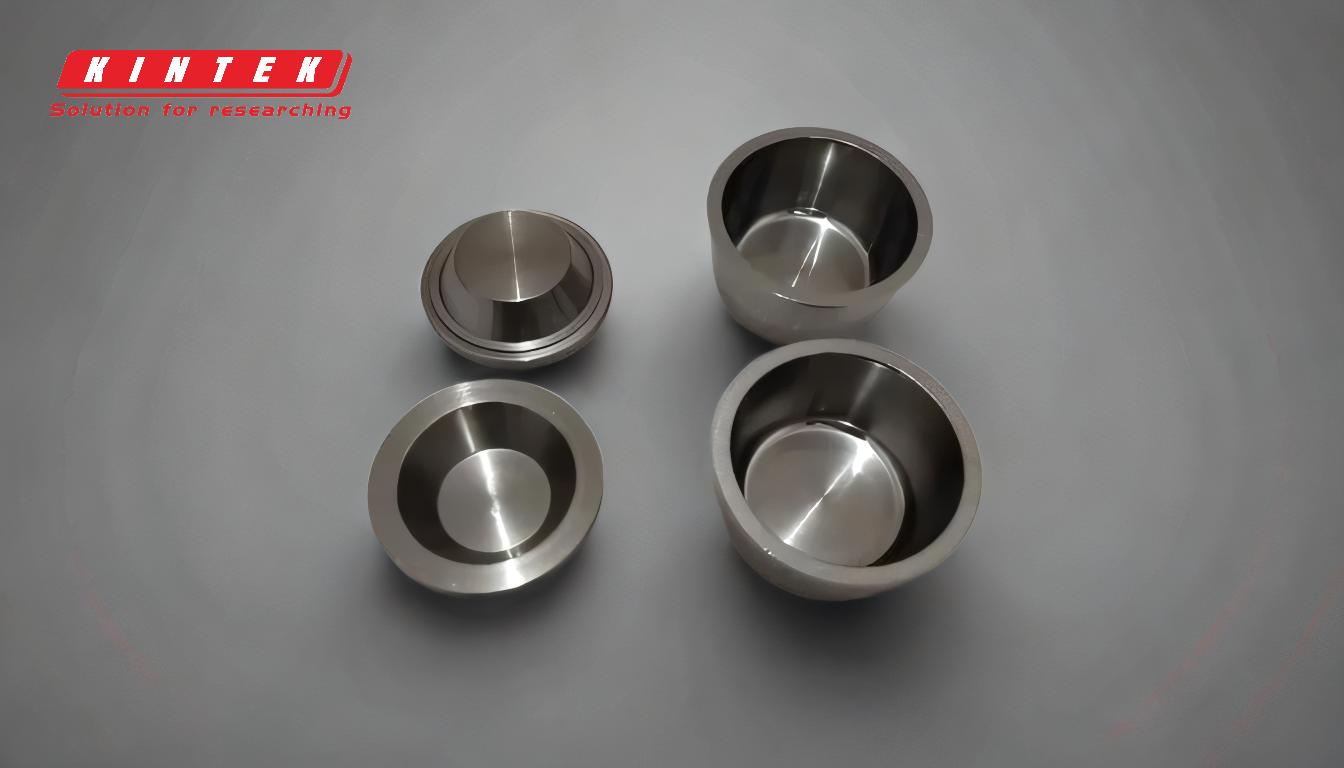
-
Advantages of Sputtering:
-
Versatility in Material Deposition:
- Sputtering can deposit a wide range of materials, including metals, semiconductors, insulators, and compounds, even those with high melting points and low vapor pressure. This makes it suitable for diverse applications.
-
Strong Film Adhesion:
- The high energy of sputtered atoms ensures excellent adhesion between the film and substrate, often forming a diffusion layer that enhances bonding.
-
High Film Purity and Density:
- Sputtering avoids contamination from evaporation sources, resulting in high-density films with fewer pinholes and high purity.
-
Controlled Film Thickness:
- Film thickness can be precisely controlled by adjusting the target current, ensuring reproducibility and uniformity across large areas.
-
Uniform Coating:
- Sputtering produces highly uniform coatings, making it ideal for precision applications.
-
Versatility in Material Deposition:
-
Disadvantages of Sputtering:
-
High Capital Costs:
- Sputtering equipment, especially for advanced methods like RF sputtering, requires significant investment in power supplies, impedance matching networks, and specialized components.
-
Low Deposition Rates:
- For certain materials, such as SiO2, sputtering has relatively low deposition rates compared to other PVD methods like thermal evaporation.
-
Material Degradation:
- Some materials, particularly organic solids, are susceptible to degradation due to ionic bombardment during the sputtering process.
-
Impurity Introduction:
- Sputtering operates under a lower vacuum range compared to evaporation, increasing the likelihood of introducing impurities into the substrate.
-
Complex Equipment:
- Dipole sputtering, for example, requires high-pressure devices and can lead to high substrate temperatures and susceptibility to impurity gases.
-
High Capital Costs:
-
Comparison of Sputtering Methods:
-
DC Sputtering:
- Pros: Effective for metal deposition, maintains anode conductivity.
- Cons: Low deposition rates in low argon ion density environments.
-
RF Sputtering:
- Pros: Suitable for insulating oxide films, avoids charge build-up on insulating targets.
- Cons: Requires expensive RF power supplies and impedance matching networks; stray magnetic fields from ferromagnetic targets can disrupt the process.
-
Thermal Deposition:
- Pros: Higher throughput and mineral utilization efficiency compared to sputtering.
- Cons: May require additional tools like sample rotation to achieve uniform coatings.
-
DC Sputtering:
-
Applications and Trade-offs:
- Sputtering is ideal for applications requiring high precision, uniformity, and strong film adhesion, such as semiconductor manufacturing and optical coatings.
- However, its slower deposition rates and higher costs make it less suitable for high-throughput industrial processes where speed and cost-efficiency are prioritized.
In summary, sputtering offers significant advantages in terms of material versatility, film quality, and precision, but its high costs, low deposition rates, and complexity must be carefully considered when selecting a deposition method.
Summary Table:
Aspect | Advantages | Disadvantages |
---|---|---|
Material Versatility | Deposits metals, semiconductors, insulators, and compounds with high precision | High capital costs, especially for advanced methods like RF sputtering |
Film Adhesion | Strong bonding due to high-energy sputtered atoms | Low deposition rates for certain materials (e.g., SiO2) |
Film Purity | High-density films with fewer pinholes and minimal contamination | Potential material degradation, especially for organic solids |
Film Thickness | Precise control and uniformity across large areas | Introduction of impurities due to lower vacuum range |
Equipment | Suitable for precision applications like semiconductor manufacturing | Complex equipment requirements, e.g., high-pressure devices for dipole sputtering |
Need help choosing the right sputtering method for your application? Contact our experts today!