Reducing production time in compression molding is crucial for improving efficiency and lowering costs. Three effective methods include avoiding thick sections in the design, using screw-compression equipment, and preheating the material. Avoiding thick sections ensures faster and more uniform curing, while screw-compression equipment enhances material flow and reduces cycle times. Preheating the material minimizes the time required for the material to reach the optimal molding temperature. Additionally, opening the compression mold to allow gases to escape during the molding cycle is known as "degassing" or "breathing," which prevents defects and ensures higher-quality parts.
Key Points Explained:
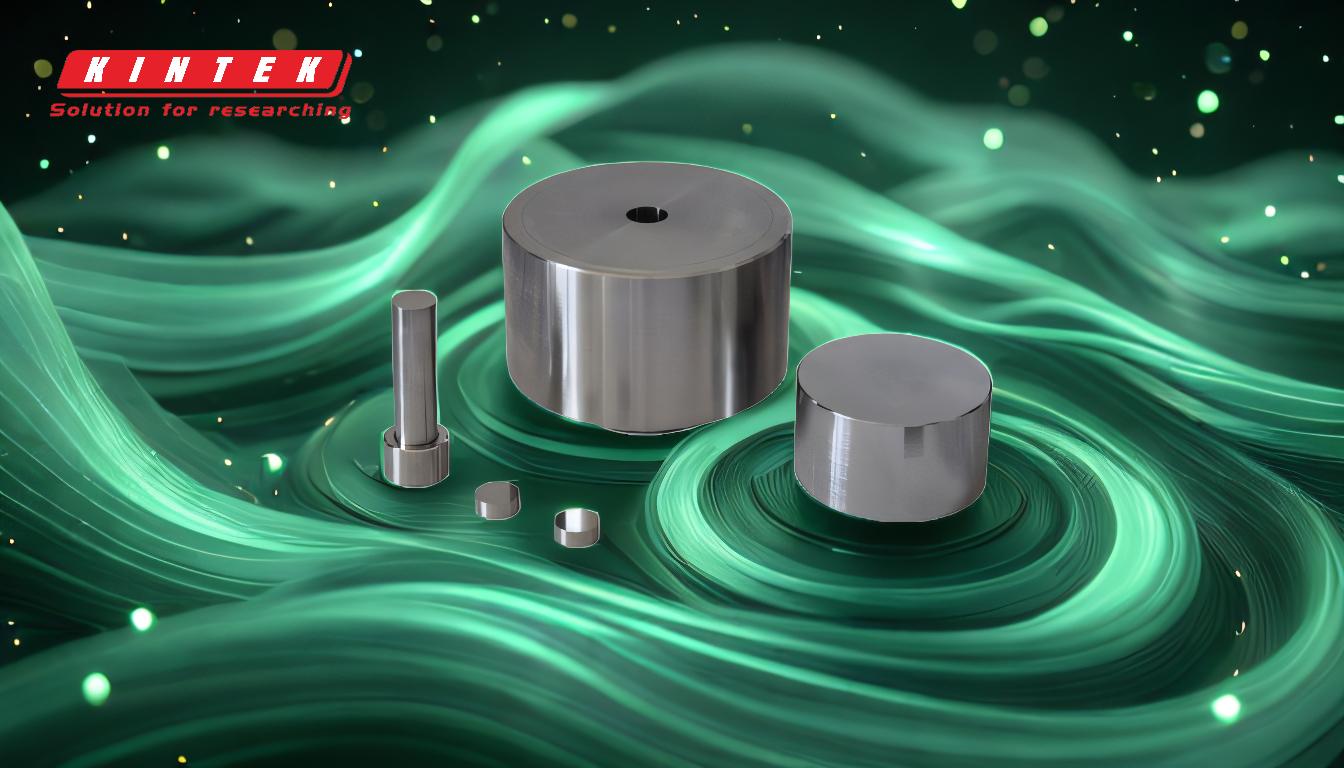
-
Avoid Thick Sections in Design
- Thick sections in a molded part take longer to cure because heat transfer is slower, leading to uneven curing and extended cycle times.
- By designing parts with uniform wall thickness, heat distribution becomes more consistent, reducing the overall production time.
- Thinner sections also reduce material usage, which can lower costs and improve part quality.
-
Use Screw-Compression Equipment
- Screw-compression equipment combines the benefits of injection and compression molding, allowing for better material flow and faster cycle times.
- The screw mechanism pre-plasticizes the material, ensuring it is uniformly heated and ready for molding, which reduces the time required for the material to reach the optimal temperature.
- This method also improves part consistency and reduces waste, further enhancing production efficiency.
-
Preheat the Material
- Preheating the material before it enters the mold reduces the time needed for the material to reach the molding temperature, speeding up the overall cycle.
- Preheating can be done using external heaters or by incorporating heating elements into the molding equipment.
- This step also improves material flow and reduces the risk of defects, such as voids or incomplete fills, which can further save time by minimizing rework.
-
Degassing (Breathing) During the Molding Cycle
- Opening the mold slightly during the molding cycle to allow trapped gases to escape is known as degassing or breathing.
- This step prevents defects like blisters, voids, or surface imperfections caused by trapped air or gases.
- While degassing adds a brief pause to the cycle, it ultimately saves time by reducing the need for post-molding corrections or part rejections.
By implementing these strategies, manufacturers can significantly reduce production time in compression molding while maintaining or even improving part quality.
Summary Table:
Method | Benefits |
---|---|
Avoid Thick Sections in Design | Faster curing, uniform heat distribution, reduced material usage, lower costs |
Use Screw-Compression Equipment | Faster cycle times, improved material flow, consistent part quality |
Preheat the Material | Reduced heating time, better material flow, fewer defects |
Degassing (Breathing) | Prevents defects, reduces rework, ensures higher-quality parts |
Optimize your compression molding process today—contact our experts for tailored solutions!