When selecting a copper alloy for brazing, it is essential to consider the specific application, the materials being joined, and the desired properties of the joint. Copper alloys are widely used in brazing due to their excellent thermal conductivity, corrosion resistance, and mechanical strength. Common copper alloys for brazing include copper-phosphorus (Cu-P), copper-silver (Cu-Ag), and copper-zinc (Cu-Zn) alloys. Each alloy has unique characteristics that make it suitable for different applications. For instance, Cu-P alloys are self-fluxing and ideal for joining copper and copper alloys, while Cu-Ag alloys offer superior strength and are often used in high-temperature applications. Understanding the properties and limitations of each alloy is crucial for achieving a strong, durable, and reliable brazed joint.
Key Points Explained:
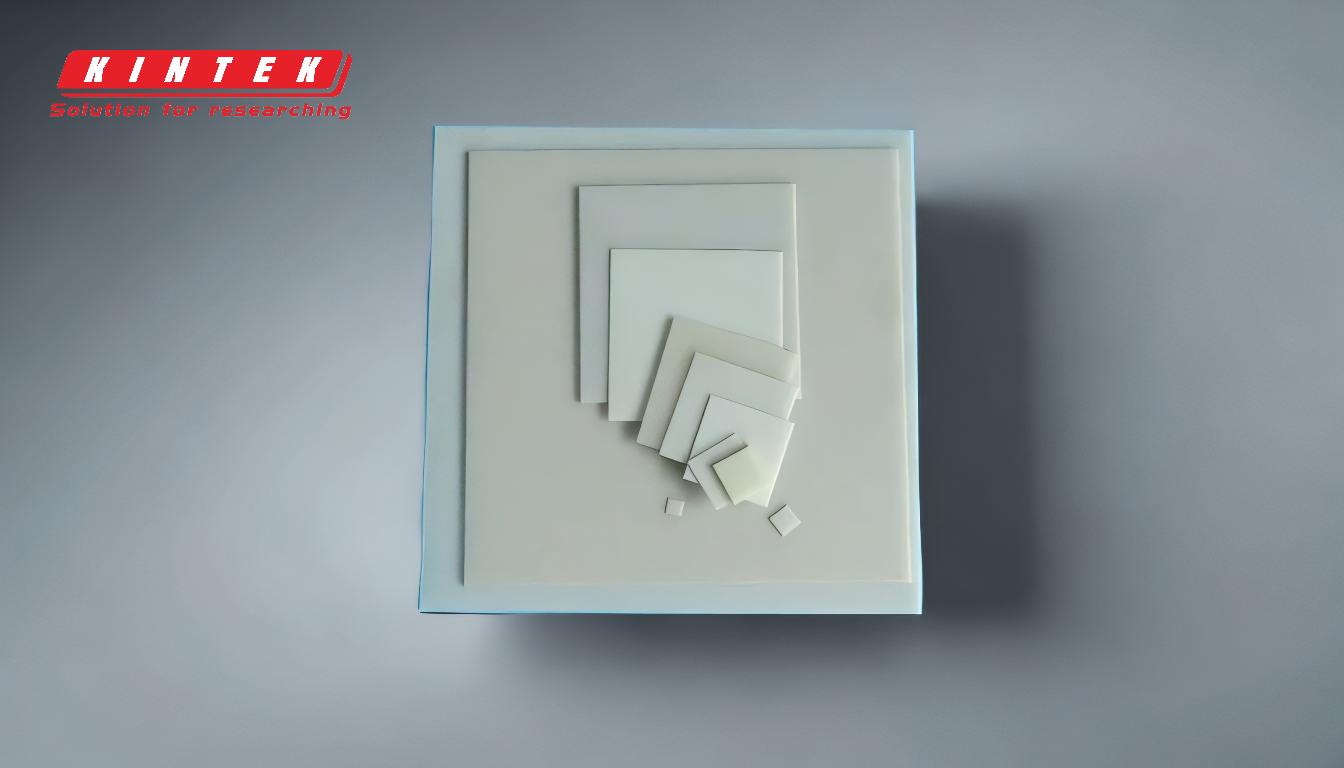
-
Copper-Phosphorus (Cu-P) Alloys:
- Self-Fluxing Properties: Cu-P alloys, such as BCuP-5, contain phosphorus, which acts as a fluxing agent. This eliminates the need for additional flux when brazing copper and copper alloys, simplifying the process.
- Applications: These alloys are commonly used in HVAC systems, refrigeration, and electrical applications. They are particularly effective for joining copper pipes and fittings.
- Limitations: Cu-P alloys are not suitable for brazing ferrous metals or nickel-based alloys due to the formation of brittle phosphides at the joint.
-
Copper-Silver (Cu-Ag) Alloys:
- High Strength and Durability: Cu-Ag alloys, such as BAg-1 and BAg-8, contain silver, which enhances the strength and ductility of the brazed joint. These alloys are ideal for applications requiring high mechanical strength and thermal conductivity.
- Applications: They are widely used in aerospace, automotive, and electronics industries, where high-performance joints are critical. Cu-Ag alloys are also suitable for brazing stainless steel, nickel alloys, and other high-temperature materials.
- Limitations: The higher cost of silver makes these alloys more expensive than other copper-based brazing materials.
-
Copper-Zinc (Cu-Zn) Alloys:
- Cost-Effective Option: Cu-Zn alloys, such as RBCuZn-D, are a more economical choice for brazing. They provide good strength and corrosion resistance, making them suitable for a variety of industrial applications.
- Applications: These alloys are often used in plumbing, HVAC, and general metal fabrication. They are effective for joining brass, bronze, and other copper alloys.
- Limitations: Cu-Zn alloys have lower thermal conductivity compared to Cu-P and Cu-Ag alloys, and they require the use of a flux to achieve proper wetting and bonding.
-
Selection Criteria:
- Material Compatibility: The choice of copper alloy depends on the materials being joined. For example, Cu-P alloys are best for copper-to-copper joints, while Cu-Ag alloys are more versatile and can join a wider range of materials.
- Operating Conditions: Consider the temperature, mechanical stress, and corrosion resistance required for the application. High-temperature applications may require Cu-Ag alloys, while cost-sensitive projects may benefit from Cu-Zn alloys.
- Joint Design and Process Requirements: The design of the joint and the brazing process (e.g., furnace brazing, torch brazing) will influence the selection of the alloy. Some alloys may require specific heating methods or post-brazing treatments.
-
Advantages of Copper Alloys in Brazing:
- Excellent Thermal Conductivity: Copper alloys provide efficient heat transfer, which is crucial in applications like heat exchangers and electronic components.
- Corrosion Resistance: Copper alloys are resistant to corrosion, ensuring the longevity of the brazed joint in harsh environments.
- Ease of Use: Many copper alloys, such as Cu-P, are easy to work with due to their self-fluxing properties, reducing the complexity of the brazing process.
-
Challenges and Considerations:
- Brittle Intermetallic Compounds: Some copper alloys, particularly those with phosphorus, can form brittle intermetallic compounds when brazing certain metals, leading to joint failure.
- Cost: The cost of the alloy, especially those containing silver, can be a significant factor in material selection.
- Process Control: Achieving a high-quality brazed joint requires careful control of temperature, heating rate, and cooling rate to avoid defects such as voids or incomplete wetting.
In conclusion, selecting the right copper alloy for brazing involves a thorough understanding of the application requirements, material compatibility, and the properties of the alloy. By carefully considering these factors, you can ensure a strong, durable, and reliable brazed joint that meets the demands of your specific application.
Summary Table:
Copper Alloy | Key Properties | Applications | Limitations |
---|---|---|---|
Copper-Phosphorus (Cu-P) | Self-fluxing, excellent for copper-to-copper joints | HVAC, refrigeration, electrical | Not suitable for ferrous metals or nickel alloys |
Copper-Silver (Cu-Ag) | High strength, ideal for high-temperature applications | Aerospace, automotive, electronics | Higher cost due to silver content |
Copper-Zinc (Cu-Zn) | Cost-effective, good strength and corrosion resistance | Plumbing, HVAC, metal fabrication | Lower thermal conductivity, requires flux |
Need help selecting the right copper alloy for your brazing project? Contact our experts today for personalized advice!