A blown film machine is a sophisticated piece of equipment designed to produce plastic film, which is widely used in various industries, including packaging, healthcare, and daily essentials. The machine operates by extruding molten plastic through a circular die, forming a tube of film. This tube is then inflated with air, stretched, and cooled to create a thin, uniform plastic film. The process allows for the production of films with different thicknesses, widths, and properties, making it versatile for a wide range of applications. The machine's precision and technical settings ensure high-quality output, meeting the demands of industries that rely on plastic films for their products.
Key Points Explained:
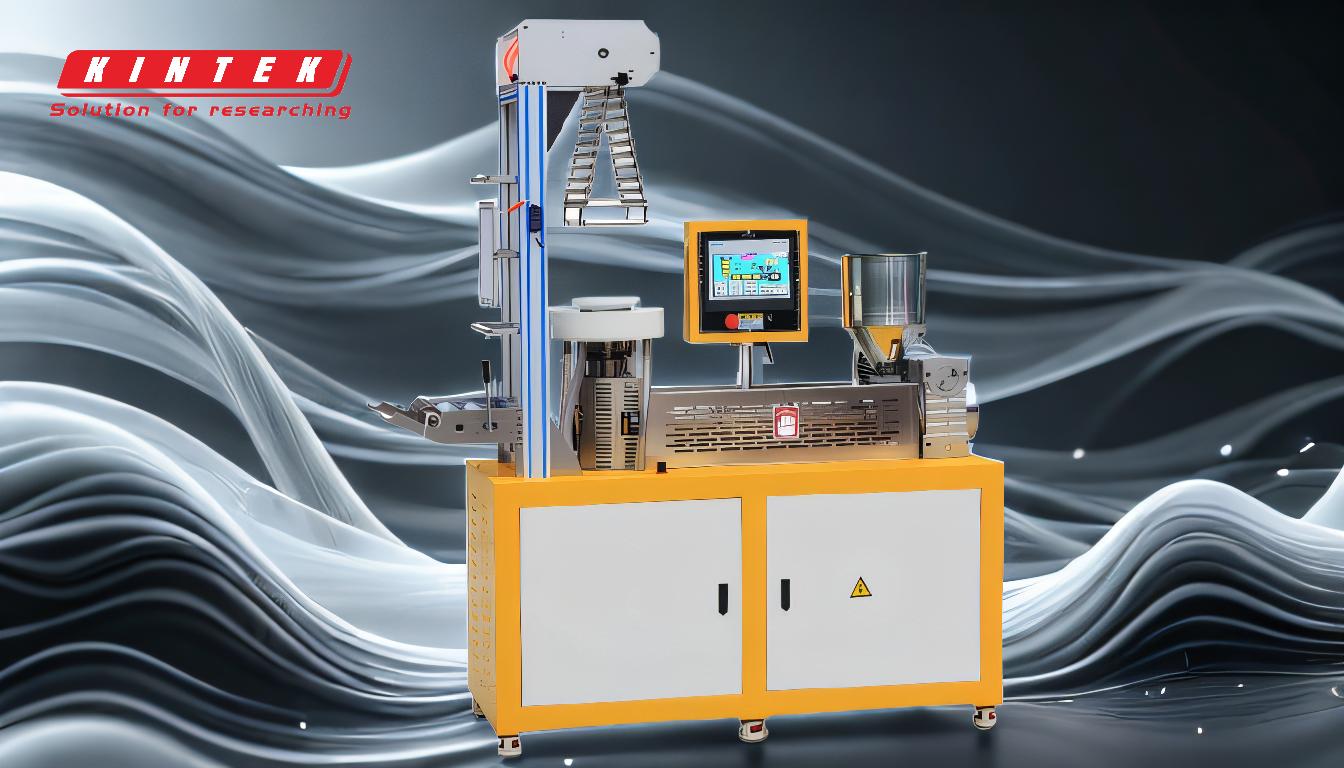
-
Purpose of a Blown Film Machine:
- The primary function of a blown film machine is to produce plastic film. This film is used in various applications, including packaging, agriculture, healthcare, and more. The machine is capable of producing films of different thicknesses, widths, and properties, making it highly versatile.
-
Basic Operation Process:
- Extrusion: The process begins with the extrusion of molten plastic through a circular die. The plastic material, usually in the form of pellets, is melted and forced through the die to form a continuous tube of film.
- Inflation: Once the plastic tube exits the die, it is inflated with air, causing it to expand into a bubble. This inflation process stretches the plastic, thinning it out and increasing its surface area.
- Cooling: The inflated bubble is then cooled, typically using air rings or water cooling systems. Cooling solidifies the plastic, locking in the desired thickness and dimensions.
- Flattening and Winding: After cooling, the bubble is flattened into a double-layered film and wound onto rolls for further processing or direct use.
-
Components of a Blown Film Machine:
- Extruder: The extruder is the core component where plastic pellets are melted and homogenized before being pushed through the die.
- Die: The die shapes the molten plastic into a tube. The design of the die can influence the thickness and uniformity of the film.
- Air Ring: The air ring is used to cool the plastic bubble as it exits the die. It ensures even cooling, which is crucial for maintaining the film's quality.
- Nip Rolls: These rolls flatten the bubble into a double-layered film and guide it towards the winding station.
- Winder: The winder collects the finished film onto rolls, making it ready for storage or further processing.
-
Types of Films Produced:
- Monolayer Films: These are single-layer films, typically used for simple packaging applications. They are easy to produce and cost-effective.
- Multilayer Films: These films consist of multiple layers, each with different properties. Multilayer films are used in more demanding applications, such as food packaging, where barrier properties (e.g., oxygen or moisture resistance) are required.
- Co-extruded Films: These are a type of multilayer film where different materials are extruded simultaneously to create a film with combined properties, such as strength and flexibility.
-
Advantages of Blown Film Technology:
- Versatility: Blown film machines can produce a wide range of film types, from thin, flexible films to thicker, more rigid ones.
- Cost-Effectiveness: The process is efficient and can produce large quantities of film at a relatively low cost.
- High-Quality Output: The precision of the machine ensures that the film produced is uniform in thickness and free from defects.
- Scalability: Blown film machines can be scaled to meet different production needs, from small-scale operations to large industrial setups.
-
Applications of Blown Film:
- Packaging: Blown film is widely used in packaging applications, including food packaging, shrink wrap, and stretch film.
- Agriculture: Agricultural films, such as greenhouse covers and mulch films, are produced using blown film technology.
- Healthcare: Blown film is used in the production of medical packaging, such as sterile wraps and IV bags.
- Consumer Goods: Everyday items like plastic bags, garbage bags, and cling film are made using blown film machines.
-
Considerations for Purchasing a Blown Film Machine:
- Production Capacity: The machine's output capacity should match the buyer's production needs. This includes considering the width and thickness of the films to be produced.
- Material Compatibility: The machine should be compatible with the types of plastic materials the buyer intends to use, such as polyethylene (PE), polypropylene (PP), or other specialized resins.
- Energy Efficiency: Energy consumption is a significant factor in the operational cost of a blown film machine. Buyers should look for machines with energy-efficient components.
- Ease of Maintenance: The machine should be easy to maintain, with accessible components and a design that minimizes downtime.
- Technical Support: Reliable technical support and after-sales service are crucial, especially for buyers who may not have in-house expertise in blown film technology.
In summary, a blown film machine is an essential piece of equipment for producing plastic films used in a wide range of industries. Its ability to produce high-quality, versatile films efficiently makes it a valuable asset for manufacturers. When purchasing a blown film machine, buyers should consider factors such as production capacity, material compatibility, energy efficiency, ease of maintenance, and technical support to ensure they select the right machine for their needs.
Summary Table:
Aspect | Details |
---|---|
Purpose | Produces plastic films for packaging, agriculture, healthcare, and more. |
Operation Process | Extrusion → Inflation → Cooling → Flattening & Winding |
Key Components | Extruder, Die, Air Ring, Nip Rolls, Winder |
Types of Films | Monolayer, Multilayer, Co-extruded |
Advantages | Versatile, cost-effective, high-quality output, scalable |
Applications | Packaging, agriculture, healthcare, consumer goods |
Purchase Considerations | Production capacity, material compatibility, energy efficiency, maintenance, technical support |
Ready to enhance your production with a blown film machine? Contact us today for expert advice and solutions!