Sputtering in business refers to a physical vapor deposition (PVD) process used to deposit thin films of material onto a substrate. This technique is widely employed in industries such as semiconductor manufacturing, precision optics, and surface finishing. The process involves creating a vacuum environment, introducing an inert gas (typically argon), and applying high voltage to generate a plasma. Positively charged ions from the plasma collide with a target material, causing atoms or molecules to be ejected and deposited onto a substrate, forming a thin, uniform, and adherent film. This method is valued for its ability to produce high-quality coatings with excellent uniformity, density, and adhesion, making it essential for various high-tech applications.
Key Points Explained:
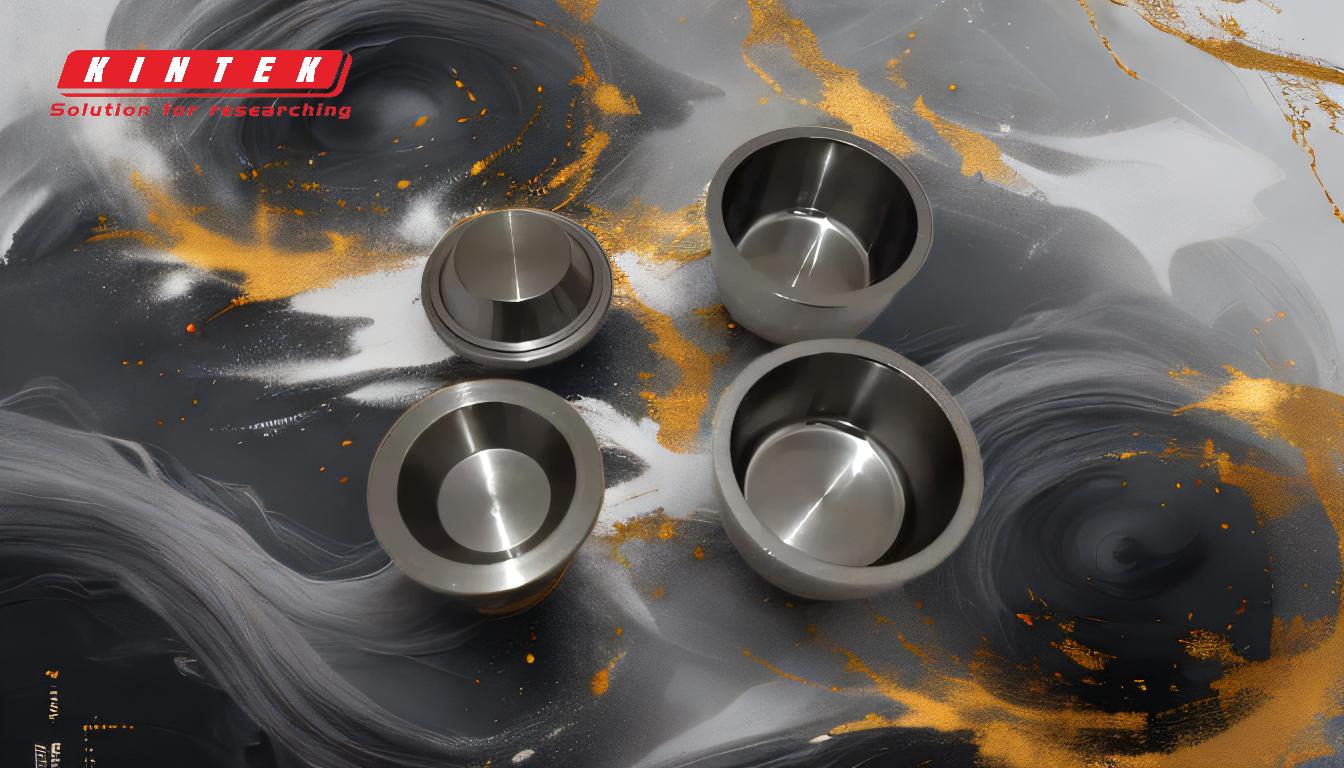
-
Definition of Sputtering:
- Sputtering is a thin-film deposition technique that falls under the category of Physical Vapor Deposition (PVD).
- It involves the use of a vacuum chamber, a target material, and a substrate to be coated.
-
Process Overview:
- Vacuum Chamber: The process begins by creating a vacuum environment to eliminate contaminants and ensure a controlled atmosphere.
- Inert Gas Introduction: An inert gas, usually argon, is introduced into the chamber.
- Plasma Generation: High voltage is applied to ionize the argon gas, creating a plasma consisting of positively charged argon ions.
- Target Erosion: The positively charged ions are accelerated towards a negatively charged target material (cathode). Upon collision, atoms or molecules are ejected from the target.
- Film Deposition: The ejected particles travel in a straight line and deposit onto the substrate, forming a thin film.
-
Key Components:
- Target Material: The material to be deposited, which can be metals, alloys, or compounds.
- Substrate: The surface to be coated, such as glass, silicon wafers, or other materials.
- Inert Gas: Typically argon, used to create the plasma.
- High Voltage Power Supply: Essential for generating the plasma and accelerating ions.
-
Advantages of Sputtering:
- Uniformity: Produces films with excellent thickness uniformity across the substrate.
- Density: Films are dense and free from voids, enhancing their mechanical and optical properties.
- Adhesion: Strong adhesion to the substrate, ensuring durability and performance.
- Versatility: Can deposit a wide range of materials, including metals, semiconductors, and insulators.
-
Applications:
- Semiconductor Industry: Used for depositing thin films in the fabrication of integrated circuits and microelectronics.
- Precision Optics: Coating lenses and mirrors to enhance optical properties.
- Surface Finishing: Applying decorative or protective coatings on various materials.
- Solar Panels: Depositing thin films for photovoltaic cells.
-
Business Implications:
- Cost-Effectiveness: Despite the initial setup costs, sputtering is cost-effective for high-volume production due to its efficiency and material utilization.
- Quality Control: Ensures consistent quality of coatings, which is critical for high-performance applications.
- Innovation: Enables the development of new materials and technologies, driving innovation in various industries.
In summary, sputtering is a critical process in modern manufacturing, offering precise control over thin-film deposition. Its applications span across multiple industries, contributing to advancements in technology and product quality. Understanding the intricacies of sputtering can help businesses optimize their production processes and maintain a competitive edge in the market.
Summary Table:
Aspect | Details |
---|---|
Definition | Thin-film deposition technique under Physical Vapor Deposition (PVD). |
Process | Vacuum chamber, inert gas (argon), plasma generation, target erosion, deposition. |
Key Components | Target material, substrate, inert gas, high voltage power supply. |
Advantages | Uniformity, density, adhesion, versatility. |
Applications | Semiconductors, precision optics, surface finishing, solar panels. |
Business Implications | Cost-effective, quality control, innovation in materials and technologies. |
Ready to enhance your production with sputtering technology? Contact us today to learn more!