A three-plate mold is a specialized type of injection molding tool designed to separate the runner system from the finished part during the molding process. It consists of three main plates: the stationary plate, the intermediate plate, and the moving plate. This design allows for the automatic separation of the runner (the channel through which molten plastic flows) from the molded part, enabling more efficient production and reducing waste. The three-plate mold is particularly useful for multi-cavity molds or when the runner system needs to be removed separately from the final product. Below, we’ll break down the key aspects of a three-plate mold and its advantages.
Key Points Explained:
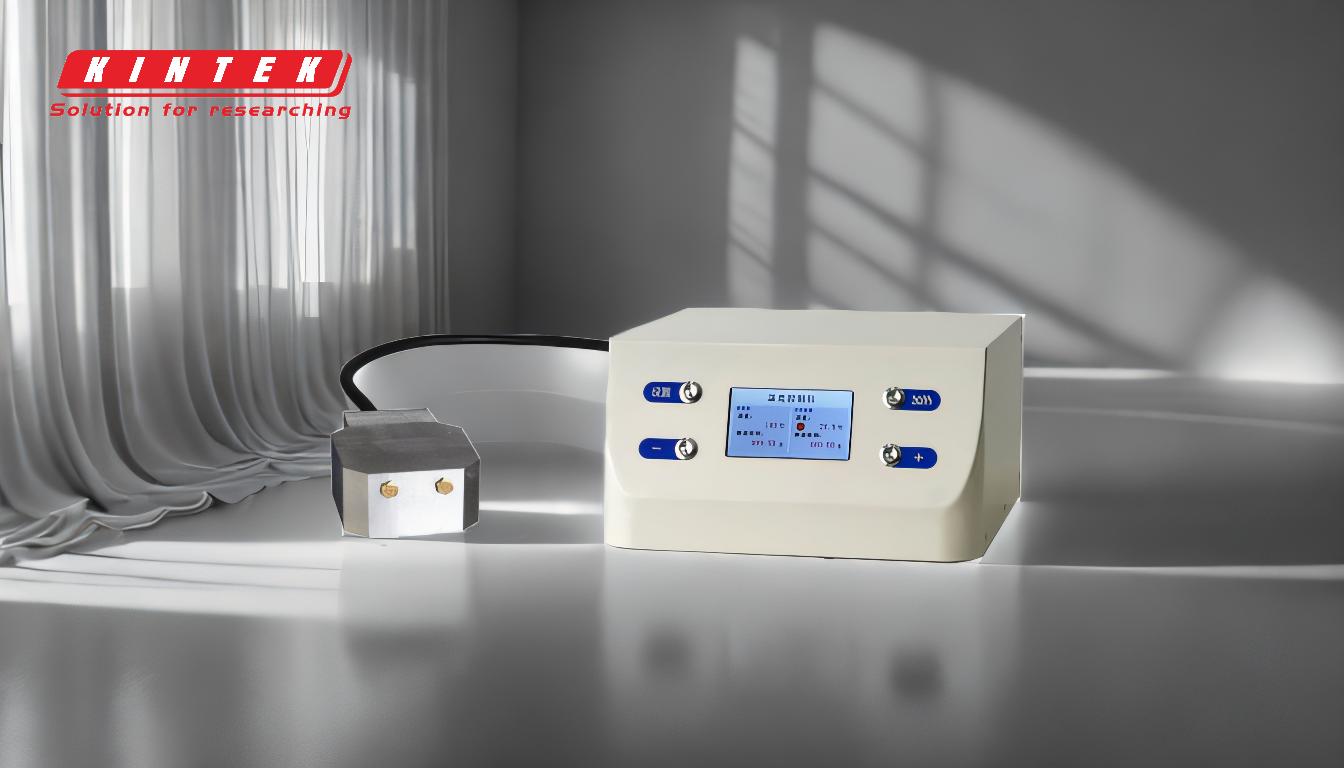
-
Definition and Structure of a Three-Plate Mold:
- A three-plate mold consists of three main plates: the stationary plate (closest to the injection unit), the intermediate plate (middle section), and the moving plate (attached to the ejector system).
- The runner system is located between the stationary and intermediate plates, while the molded part is formed between the intermediate and moving plates.
- This design allows for two distinct parting lines: one for the runner system and one for the finished part.
-
How It Works:
- During the injection molding process, molten plastic is injected into the mold cavity through the runner system.
- When the mold opens, the three plates separate in a specific sequence:
- First, the stationary and intermediate plates separate, allowing the runner system to be ejected.
- Next, the intermediate and moving plates separate, enabling the finished part to be ejected.
- This sequential separation ensures that the runner and the part are removed independently.
-
Advantages of a Three-Plate Mold:
- Automatic Runner Separation: The runner system is automatically separated from the finished part, reducing manual labor and improving efficiency.
- Reduced Waste: Since the runner can be collected and recycled separately, material waste is minimized.
- Flexibility in Design: Three-plate molds are ideal for multi-cavity molds or complex parts where the gate (the entry point of molten plastic) needs to be located away from the parting line.
- Improved Part Quality: The design allows for better control over gate placement, reducing defects such as weld lines or sink marks.
-
Applications:
- Three-plate molds are commonly used in industries where high precision and efficiency are required, such as automotive, electronics, and consumer goods.
- They are particularly useful for producing small, intricate parts or when using materials that are expensive or difficult to process.
-
Comparison with Two-Plate Molds:
- Unlike two-plate molds, which have a single parting line and require manual removal of the runner, three-plate molds offer automated runner separation.
- Three-plate molds are more complex and expensive to manufacture but provide greater flexibility and efficiency in production.
-
Considerations for Purchasers:
- Cost: Three-plate molds are more expensive than two-plate molds due to their complexity and additional components.
- Maintenance: The additional moving parts in a three-plate mold require regular maintenance to ensure smooth operation.
- Material Compatibility: Ensure the mold design is compatible with the specific material being used, as some materials may require adjustments to the runner system or gate design.
By understanding the structure, functionality, and advantages of a three-plate mold, purchasers can make informed decisions about whether this type of mold is suitable for their specific production needs. Its ability to automate runner separation and improve part quality makes it a valuable tool for high-volume or precision manufacturing processes.
Summary Table:
Aspect | Details |
---|---|
Structure | Three plates: stationary, intermediate, and moving plates. |
Key Feature | Automatic separation of runner system from the finished part. |
Advantages | - Automatic runner separation - Reduced waste - Improved part quality |
Applications | Automotive, electronics, consumer goods, and precision manufacturing. |
Comparison | More complex and expensive than two-plate molds but offers greater efficiency. |
Considerations | - Higher cost - Regular maintenance - Material compatibility |
Ready to optimize your injection molding process? Contact us today to learn more about three-plate molds!