A leak in a vacuum system refers to the unintended entry of air or gas into the system, which compromises its ability to maintain a vacuum. This can occur due to imperfections in sealing surfaces, manufacturing defects, or wear and tear over time. Preventing leaks involves ensuring the flatness of sealing surfaces, testing the airtightness of gas flow systems, and purging with inert gases. Additionally, precise manufacturing and regular maintenance are essential to maintain the integrity of the vacuum system.
Key Points Explained:
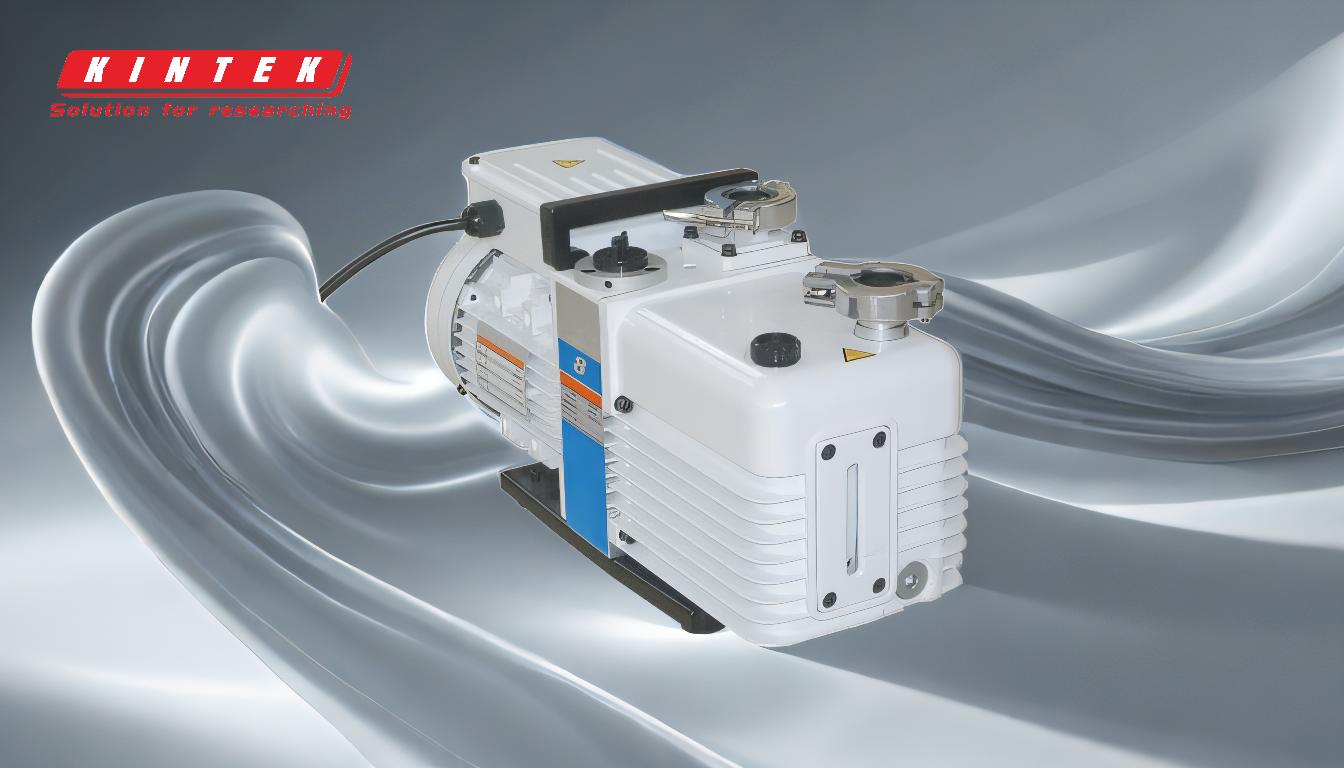
-
Definition of a Leak in a Vacuum System:
- A leak in a vacuum system is the unintended entry of air or gas into the system, which disrupts its ability to maintain a vacuum. This can lead to reduced efficiency, contamination, or failure of the system.
-
Causes of Leaks:
- Imperfect Sealing Surfaces: If the sealing surfaces are not perfectly flat, gaps can form, allowing air or gas to enter.
- Manufacturing Defects: Inaccurate dimensions or shapes of vacuum chambers can create weak points where leaks may occur.
- Wear and Tear: Over time, seals and gaskets can degrade, leading to leaks.
-
Prevention Measures:
- Ensuring Flatness of Sealing Surfaces: Proper machining and finishing of sealing surfaces can prevent gaps and ensure a tight seal.
- Testing Airtightness: Regular testing of the gas flow systems using methods like pressure decay testing or helium leak detection can identify potential leaks before they become problematic.
- Purging with Inert Gases: Purging the system with inert gases like nitrogen can help remove any residual air or moisture, reducing the risk of leaks.
-
Manufacturing Precision:
- Strict Measurement of Shapes and Dimensions: During the manufacturing process, ensuring that vacuum chambers are made to precise specifications can prevent weak points that might lead to leaks.
- Quality Control: Implementing rigorous quality control measures can catch defects early, ensuring that only components that meet strict standards are used in the vacuum system.
-
Maintenance and Monitoring:
- Regular Inspections: Periodic inspections of seals, gaskets, and other components can help identify and address wear and tear before leaks occur.
- Proactive Replacement: Replacing seals and gaskets at regular intervals, even if they appear to be in good condition, can prevent unexpected leaks.
By understanding the causes of leaks and implementing these prevention measures, the integrity and efficiency of a vacuum system can be maintained, ensuring its reliable operation over time.
Summary Table:
Aspect | Details |
---|---|
Definition | Unintended entry of air/gas, disrupting vacuum integrity. |
Causes | Imperfect seals, manufacturing defects, wear and tear. |
Prevention Measures | Flat sealing surfaces, airtightness testing, inert gas purging. |
Manufacturing Precision | Strict measurement, quality control to avoid weak points. |
Maintenance | Regular inspections, proactive replacement of seals and gaskets. |
Ensure your vacuum system operates flawlessly—contact our experts today for tailored solutions!