The ball mill method of size reduction is a mechanical process that uses grinding media (balls) to reduce the size of materials through impact and attrition. It operates by rotating a cylinder (jar) containing the material and grinding balls, where the balls cascade and collide with the material, breaking it into smaller particles. The efficiency of size reduction depends on the speed of the mill, with optimal grinding achieved at a specific rotational speed where the balls are carried to the top and then fall in a cascade. This method is widely used in industries for grinding and homogenizing materials.
Key Points Explained:
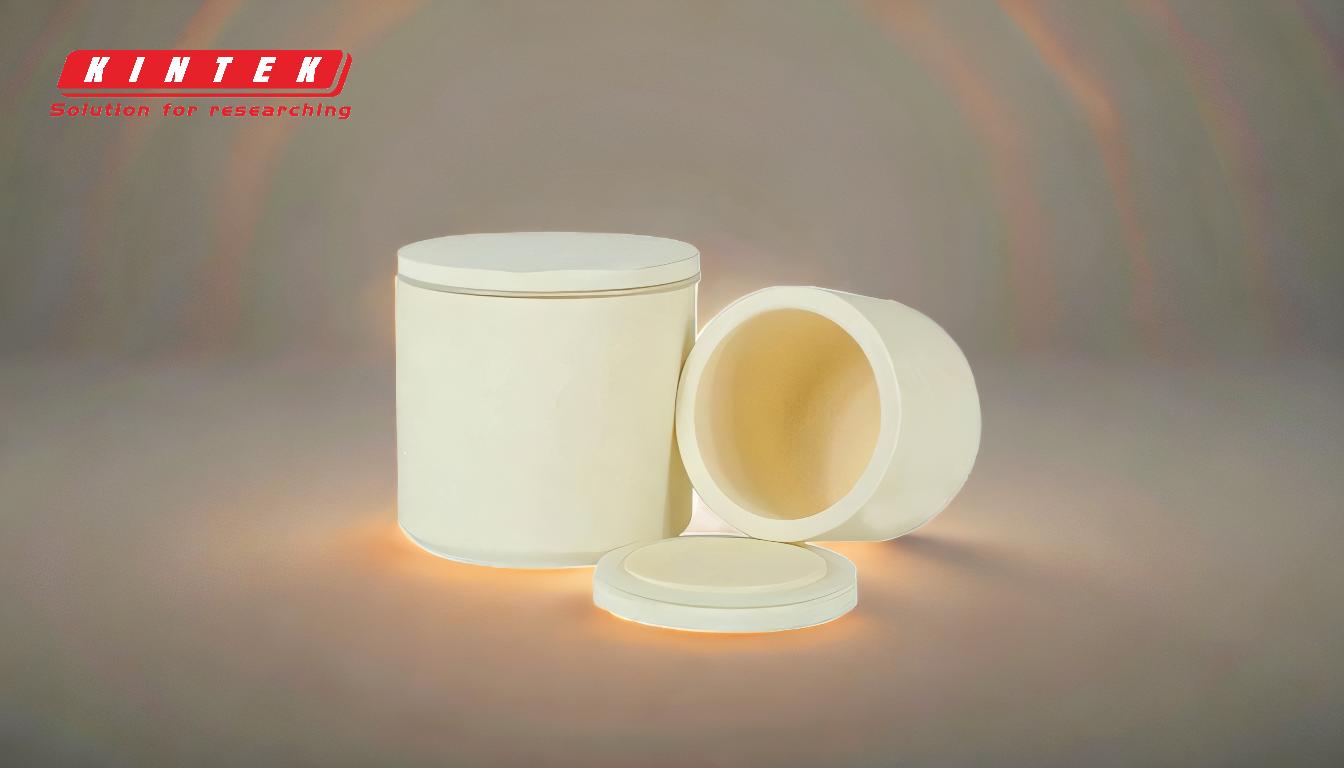
-
Principle of Operation:
- The ball mill operates on two primary principles: Impact and Attrition.
- Impact: This occurs when heavy grinding balls collide with the material, exerting pressure and breaking it into smaller particles.
- Attrition: This involves the reduction of material size through repeated collisions and friction between the material and the grinding balls.
- The ball mill operates on two primary principles: Impact and Attrition.
-
Components of a Ball Mill:
- Grinding Jars: Containers that hold the material and grinding balls. In planetary ball mills, these jars rotate on their own axis while also orbiting around a central axis (sun wheel).
- Grinding Media (Balls): Typically made of steel, ceramic, or other hard materials, these balls are responsible for the size reduction through collisions with the material.
- Sun Wheel: A circular platform that holds the grinding jars and rotates, causing the jars to spin in the opposite direction.
-
Mechanism of Size Reduction:
- The size reduction process is driven by the motion of the grinding balls within the jar. As the jar rotates, the balls are lifted to a certain height and then fall back, creating a cascading effect.
- The cascading motion generates impact forces when the balls strike the material, as well as attrition forces as the material is ground between the balls and the jar walls.
-
Effect of Speed on Size Reduction:
- Low Speed: At low rotational speeds, the balls tend to slide or roll over each other, resulting in minimal size reduction.
- High Speed: At very high speeds, centrifugal force causes the balls to be thrown against the cylinder wall, preventing effective grinding.
- Optimal Speed: At the correct speed, the balls are carried to the top of the jar and then fall in a cascade, maximizing the impact and attrition forces for efficient size reduction.
-
Operational Steps:
- Loading: The material to be ground is loaded into the grinding jar along with a fixed number of grinding balls.
- Sealing: The jar is sealed with a lid to prevent spillage or contamination.
- Running: The ball mill is started, and the speed is adjusted to the optimal level for size reduction.
- Stopping: Once the desired particle size is achieved, the machine is stopped, and the ground material is removed for further processing or use.
-
Applications:
- Ball mills are widely used in various industries for grinding and homogenizing materials, including:
- Pharmaceuticals: For reducing drug particles to a fine powder.
- Mining: For grinding ores to liberate minerals.
- Ceramics: For preparing fine ceramic powders.
- Chemical: For mixing and grinding chemicals to achieve uniform particle size.
- Ball mills are widely used in various industries for grinding and homogenizing materials, including:
-
Advantages:
- Versatility: Can grind a wide range of materials, from soft to very hard.
- Efficiency: Provides a high degree of size reduction with relatively low energy consumption.
- Scalability: Can be used for both laboratory-scale and industrial-scale applications.
-
Limitations:
- Wear and Tear: The grinding balls and jar walls are subject to wear, requiring periodic replacement.
- Heat Generation: Prolonged grinding can generate heat, which may affect heat-sensitive materials.
- Noise: The operation of ball mills can be noisy, especially at high speeds.
In summary, the ball mill method of size reduction is a highly effective and widely used technique for grinding materials into fine particles. Its efficiency is governed by the principles of impact and attrition, and the process is optimized by controlling the rotational speed of the mill. Understanding the components, mechanism, and operational parameters is crucial for achieving the desired particle size and maintaining the quality of the ground material.
Summary Table:
Aspect | Details |
---|---|
Principle of Operation | Impact and attrition for size reduction. |
Components | Grinding jars, grinding balls, and sun wheel. |
Mechanism | Cascading motion of balls generates impact and attrition forces. |
Optimal Speed | Balls carried to the top and fall in a cascade for efficient grinding. |
Applications | Pharmaceuticals, mining, ceramics, and chemical industries. |
Advantages | Versatility, efficiency, and scalability. |
Limitations | Wear and tear, heat generation, and noise. |
Discover how the ball mill method can optimize your grinding process—contact us today for expert guidance!