Ceramic sintering is a critical manufacturing process used to transform powdered ceramic materials into dense, durable, and strong solid objects. This process involves heating the ceramic powder to a temperature below its melting point, allowing the particles to bond tightly through atomic diffusion. The result is a reduction in porosity, increased strength, and improved structural integrity. Sintering is widely used in the production of ceramics, pottery, and other high-performance materials. The process typically involves several steps, including preparing the ceramic slurry, forming a green body, binder removal, and high-temperature sintering. This method is essential for creating components with precise mechanical and thermal properties.
Key Points Explained:
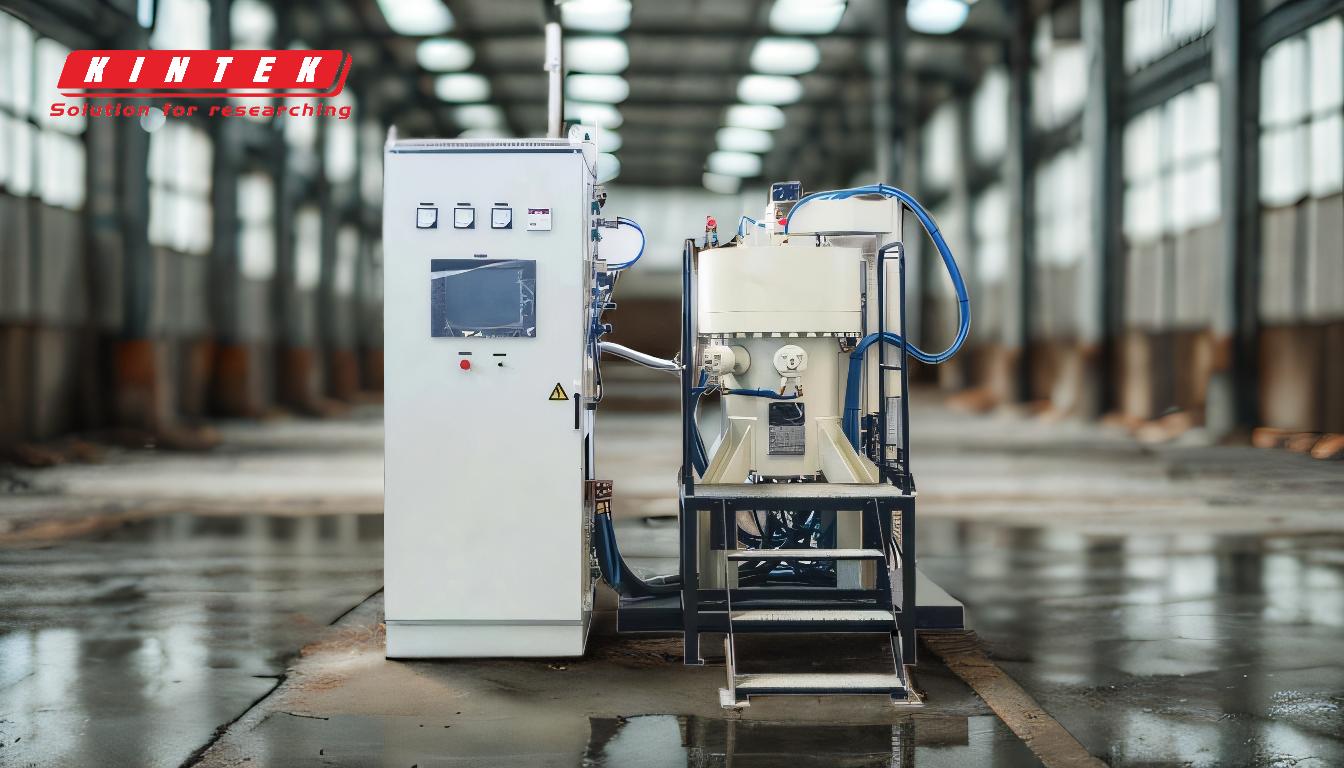
-
Definition of Ceramic Sintering:
- Ceramic sintering is a process that compacts and solidifies powdered ceramic materials by applying heat and sometimes pressure, without melting the material. This results in a dense, strong, and durable final product.
-
Purpose of Sintering:
- Densification: Reduces porosity, making the material more compact and less permeable.
- Strength Enhancement: Forces atoms to bond more tightly, increasing mechanical strength.
- Durability: Creates a harder and more wear-resistant material.
- Shape Retention: Maintains the desired shape and dimensions of the ceramic object.
-
Mechanism of Sintering:
- Atomic Diffusion: Atoms diffuse across particle boundaries, fusing particles together.
- Temperature Control: Heating is done below the material’s melting point to prevent liquefaction.
- Pressure Application: In some cases, pressure is applied to enhance particle bonding.
-
Steps in the Ceramic Sintering Process:
- Slurry Preparation: Mixing ceramic powder with water, binders, and deflocculants to form a slurry.
- Spray Drying: Converting the slurry into a free-flowing powder.
- Green Body Formation: Pressing the powder into a mold to create a preliminary shape (green body).
- Binder Removal: Heating the green body at low temperatures to burn off binders.
- High-Temperature Sintering: Heating the green body at high temperatures to fuse ceramic particles and achieve final properties.
-
Applications of Ceramic Sintering:
- Pottery and Ceramics: Used in the production of pottery, tiles, and other ceramic objects.
- Advanced Ceramics: Essential for manufacturing high-performance ceramics used in electronics, aerospace, and medical devices.
- Powder Metallurgy: Applied in the production of metal-ceramic composites and other specialized materials.
-
Benefits of Ceramic Sintering:
- Improved Material Properties: Enhanced strength, hardness, and thermal stability.
- Precision Manufacturing: Allows for the creation of complex shapes with tight tolerances.
- Cost-Effective: Reduces material waste and energy consumption compared to melting processes.
-
Challenges and Considerations:
- Shrinkage: The material may shrink during sintering, requiring careful design and process control.
- Temperature Management: Precise temperature control is necessary to avoid defects like warping or cracking.
- Material Selection: Different ceramic materials require specific sintering conditions to achieve optimal results.
-
Comparison with Other Processes:
- Melting: Unlike melting, sintering does not liquefy the material, preserving its original composition and structure.
- Compaction: Sintering involves both heat and pressure, whereas compaction typically relies solely on mechanical pressure.
By understanding these key points, equipment and consumable purchasers can better evaluate the sintering process for their specific needs, ensuring they select the right materials and methods for their applications.
Summary Table:
Aspect | Details |
---|---|
Definition | Compacts and solidifies powdered ceramics using heat and sometimes pressure. |
Purpose | Densification, strength enhancement, durability, and shape retention. |
Mechanism | Atomic diffusion, temperature control, and pressure application. |
Steps | Slurry prep, spray drying, green body formation, binder removal, sintering. |
Applications | Pottery, advanced ceramics, powder metallurgy. |
Benefits | Improved strength, precision manufacturing, cost-effectiveness. |
Challenges | Shrinkage, temperature management, material selection. |
Comparison | Unlike melting, sintering preserves material structure without liquefaction. |
Discover how ceramic sintering can enhance your manufacturing process—contact our experts today!