A high-pressure high-temperature (HPHT) autoclave reactor is a specialized piece of equipment designed to conduct chemical reactions or sterilization processes under extreme pressure and temperature conditions. It is widely used in industries such as chemical manufacturing, pharmaceuticals, petrochemicals, and wastewater treatment, as well as in research and education. The reactor operates at pressures ranging from 50 to 350 bar and temperatures up to 500 °C, making it ideal for processes like hydrogenation, oxidation, polymerization, and sterilization. Its robust construction, which includes materials like stainless steel, Hastelloy, and titanium, ensures safety and durability. The reactor's design features, such as magnetic drive couplings, safety interlocks, and precise temperature control, make it highly efficient and reliable for demanding applications.
Key Points Explained:
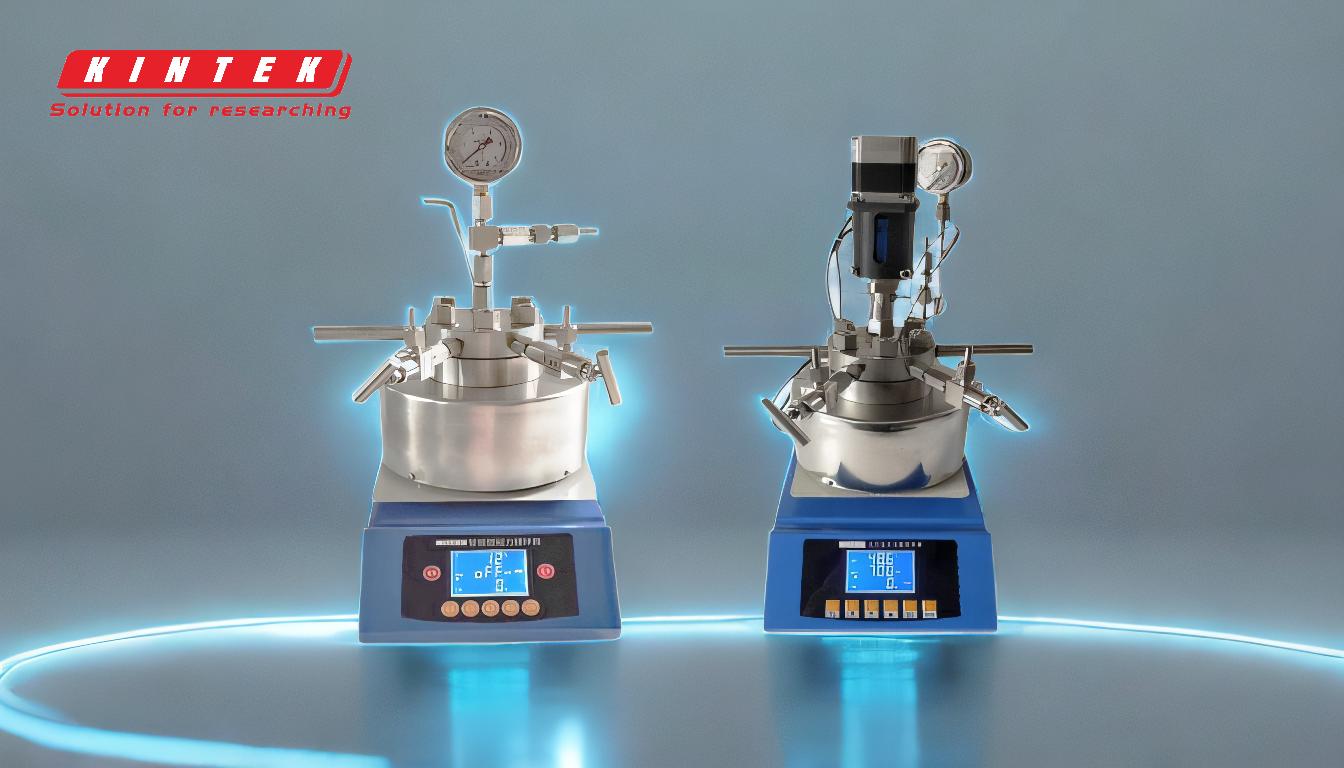
-
Definition and Purpose:
- A high-pressure high-temperature autoclave reactor is a device used to perform chemical reactions or sterilization under elevated pressure and temperature conditions.
- It is often compared to a "pressure cooker" but operates at much higher pressures (50–350 bar) and temperatures (up to 500 °C).
- Applications include curing coatings, vulcanizing rubber, hydrothermal synthesis, producing composites, sterilizing medical equipment, and conducting research in pharmaceuticals and biomedicine.
-
Working Principle:
- The reactor generates high pressure and temperature to initiate and sustain chemical reactions or sterilization processes.
- High pressure and temperature break down molecular structures, enabling chemical reactions or destroying pathogens.
- High-pressure steam, a by-product, can power turbines within the reactor, improving energy efficiency.
-
Design and Construction:
- The reactor has a cylindrical shell with Tori spherical or ellipsoidal ends for structural integrity.
- It features a heating jacket on the outer side, stiffener rings for strength, and a heat exchanger to minimize heat loss.
- Materials like SS-316, Hastelloy, Monel, Nickel, Titanium, and Zirconium are used to withstand extreme conditions.
- Key components include a magnetic drive coupling for sealing, an automatically locking detachable lid with a safety interlock, and PID-controlled electrical heating for precise temperature regulation.
-
Applications:
- Industrial: Used in the production of fine chemicals, pharmaceuticals, dyes, coatings, and petrochemicals.
- Medical: Sterilization of medical equipment and lab tools.
- Research: Biomedical and pharmaceutical studies, as well as educational purposes.
- Environmental: Wastewater treatment for sludge disinfection and carbonization.
-
Operational Features:
- The reactor can handle volumes ranging from 50 mL to 500 liters.
- It operates at pressures up to 350 bar and temperatures up to 500 °C.
- Designed for safety, it includes features like automatic locking lids, safety interlocks, and robust materials to prevent leaks or failures.
-
Chemical Processes:
- The reactor is suitable for a wide range of chemical reactions, including hydrogenation, oxidation, alkylation, chlorination, carboxylation, nitration, polymerization, amination, bromination, ethoxylation, esterification, and sulphonation.
- These processes are essential in industries like pharmaceuticals, petrochemicals, and specialty chemicals.
-
Advantages:
- High efficiency due to precise temperature and pressure control.
- Versatility in handling various chemical reactions and sterilization processes.
- Safety features ensure reliable operation under extreme conditions.
- Durable construction with high-quality materials extends the lifespan of the equipment.
-
Considerations for Purchasers:
- Material Compatibility: Ensure the reactor material is compatible with the chemicals and processes involved.
- Volume and Capacity: Choose a reactor size that matches the required volume for your applications.
- Pressure and Temperature Range: Verify that the reactor can handle the specific pressure and temperature requirements of your processes.
- Safety Features: Look for features like safety interlocks, automatic locking lids, and robust sealing mechanisms.
- Energy Efficiency: Consider reactors with heat exchangers or steam turbines to improve energy efficiency.
By understanding these key points, purchasers can make informed decisions when selecting a high-pressure high-temperature autoclave reactor for their specific needs.
Summary Table:
Feature | Details |
---|---|
Pressure Range | 50–350 bar |
Temperature Range | Up to 500 °C |
Materials | Stainless steel, Hastelloy, Titanium, Nickel, Zirconium |
Applications | Chemical manufacturing, pharmaceuticals, petrochemicals, wastewater treatment |
Key Processes | Hydrogenation, oxidation, polymerization, sterilization |
Safety Features | Magnetic drive couplings, safety interlocks, automatic locking lids |
Volume Capacity | 50 mL to 500 liters |
Ready to enhance your chemical processes? Contact us today to find the perfect HPHT autoclave reactor for your needs!