A high-pressure reactor is a specialized piece of equipment designed to conduct chemical reactions or processes under elevated pressure and temperature conditions. It is a robust, purpose-built pressure vessel made from sturdy materials to withstand internal stresses and ensure safety. These reactors are widely used in industries such as chemical, petrochemical, pharmaceutical, and materials science for applications like hydrogenation, polymerization, hydrothermal synthesis, and corrosion testing. Key features include precise pressure and temperature control, safety mechanisms, and mixing systems to ensure uniform reactions. High-pressure reactors enable faster reaction rates and altered thermodynamic outcomes, making them essential for advanced chemical processes and research.
Key Points Explained:
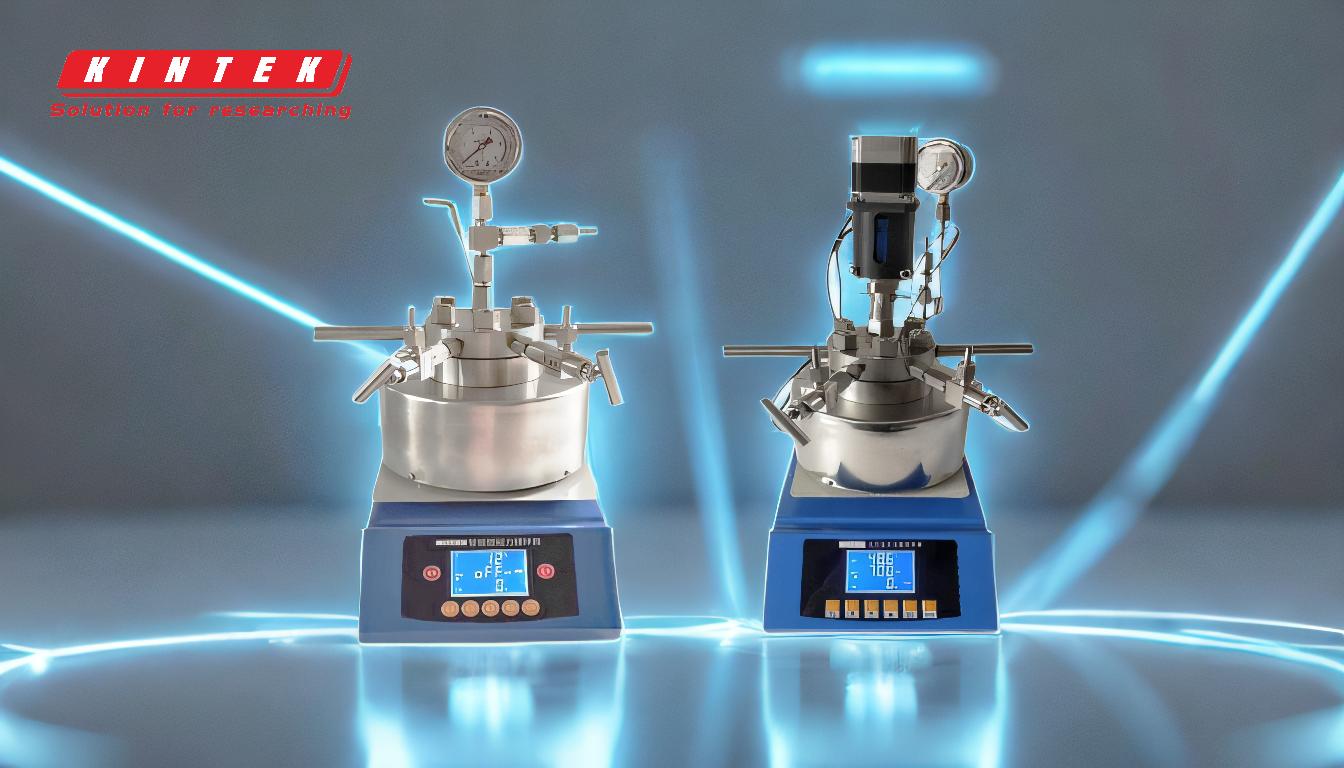
-
Definition and Purpose of High-Pressure Reactors:
- A high-pressure reactor is a specialized container designed to hold and conduct chemical reactions or processes under high pressure and temperature.
- Its primary purpose is to create conditions that alter reaction kinetics and thermodynamic equilibrium, enabling faster reaction rates and unique chemical outcomes.
- These reactors are essential in industries like chemical manufacturing, pharmaceuticals, petrochemicals, and materials science.
-
Design and Construction:
- High-pressure reactors are built from sturdy materials capable of withstanding longitudinal and hoop stresses caused by internal pressure.
- They feature an inert inner surface to prevent corrosion or contamination of the reaction mixture.
- Safety features, such as pressure relief valves and secure closures, are integrated to prevent hazards and ensure safe operation.
-
Key Components:
- Pressure Vessel: The primary container that holds the reaction mixture and withstands high internal pressures.
- Closure: A secure lid or cover designed to seal the reactor, preventing leaks of reactants or products.
- Temperature Control: Systems for heating or cooling to precisely regulate the reaction temperature.
- Pressure Control: Valves, safety devices, and monitoring equipment to maintain and monitor pressure levels.
- Stirring or Mixing Mechanism: Ensures uniform mixing of reactants and homogeneous temperature distribution (e.g., magnetic stirrers or impellers).
- Ports or Connections: Allow for the introduction of reactants, sampling, monitoring, and removal of products.
-
Applications:
- Chemical Industry: Used for hydrogenation, polymerization, catalyst screening, and hydrothermal synthesis.
- Pharmaceuticals: Employed in drug development and synthesis under controlled conditions.
- Materials Science: Utilized for producing composites, curing coatings, and vulcanizing rubber.
- Research and Development: Enables scientists to study reactions under extreme conditions, leading to new discoveries and innovations.
-
Operational Mechanism:
- High-pressure reactors work by controlling the pressure and temperature within the vessel, allowing researchers to optimize reaction conditions.
- The high-pressure environment can significantly alter reaction rates and outcomes, making it possible to achieve results that are not feasible at ambient conditions.
- Precise monitoring and control systems ensure the safety and efficiency of the reaction process.
-
Advantages:
- Enhanced Reaction Rates: High pressure accelerates reaction kinetics, reducing reaction times.
- Improved Thermodynamic Control: Enables reactions that are otherwise impossible at ambient conditions.
- Versatility: Suitable for a wide range of applications across multiple industries.
- Safety: Advanced safety features minimize risks associated with high-pressure operations.
-
Industries and Use Cases:
- Chemical Manufacturing: For processes like hydrogenation and polymerization.
- Petrochemicals: Used in refining and processing hydrocarbons.
- Pharmaceuticals: Essential for synthesizing active pharmaceutical ingredients (APIs).
- Materials Science: Critical for developing advanced materials and composites.
- Research Laboratories: Enables experimental studies under extreme conditions.
-
Considerations for Purchasing:
- Material Compatibility: Ensure the reactor materials are compatible with the chemicals and conditions used.
- Pressure and Temperature Range: Select a reactor that meets the required pressure and temperature specifications.
- Safety Features: Prioritize reactors with robust safety mechanisms, such as pressure relief valves and secure closures.
- Scalability: Consider whether the reactor can be scaled up for industrial use or down for laboratory research.
- Ease of Maintenance: Opt for reactors with accessible components for cleaning and maintenance.
By understanding these key points, purchasers and researchers can make informed decisions when selecting and using high-pressure reactors for their specific needs.
Summary Table:
Key Feature | Description |
---|---|
Purpose | Conducts chemical reactions under high pressure and temperature conditions. |
Design | Sturdy materials, inert inner surfaces, and integrated safety features. |
Key Components | Pressure vessel, temperature control, mixing mechanisms, and safety devices. |
Applications | Hydrogenation, polymerization, drug synthesis, and materials research. |
Advantages | Faster reaction rates, improved thermodynamic control, and enhanced safety. |
Industries | Chemical, petrochemical, pharmaceutical, materials science, and research labs. |
Purchasing Considerations | Material compatibility, pressure/temperature range, safety, scalability, and maintenance. |
Ready to enhance your chemical processes? Contact us today to find the perfect high-pressure reactor for your needs!