Mold tool design is a highly specialized and technical process that involves creating the tools (molds) used to manufacture plastic parts. It requires a deep understanding of engineering principles, material properties, and manufacturing processes to ensure that the final product meets precise dimensional and design specifications. The process involves designing the mold's structure, selecting appropriate materials, and incorporating features like cooling systems, ejection mechanisms, and gating systems. The goal is to produce high-quality, repeatable plastic parts efficiently and cost-effectively.
Key Points Explained:
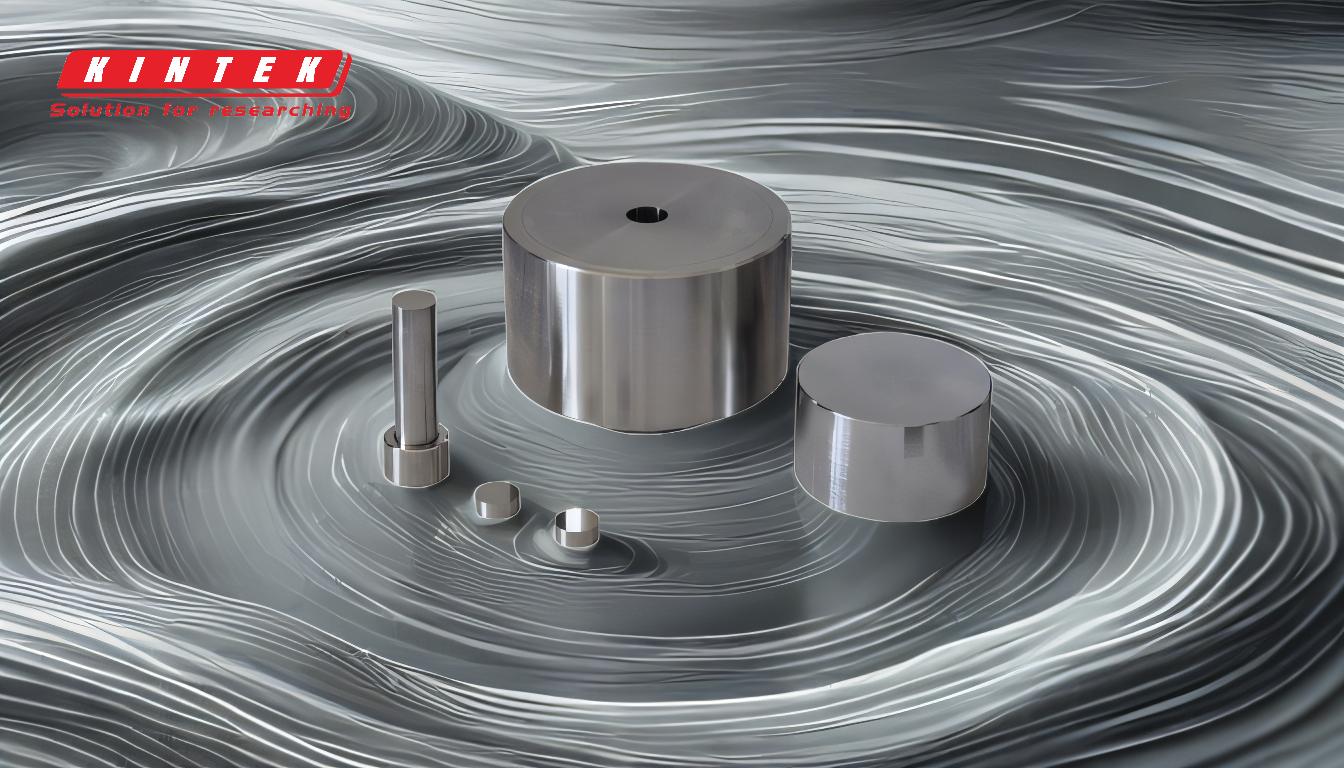
-
Definition of Mold Tool Design
- Mold tool design refers to the process of creating the tools (molds) used in manufacturing plastic parts.
- It involves designing the physical structure of the mold, which will shape molten plastic into the desired part.
- The design must account for the part's geometry, material properties, and production requirements.
-
Complexity and Technical Expertise
- Mold tool design is a complex process that requires high levels of technical expertise.
- Engineers must consider factors such as part shrinkage, cooling rates, and material flow to ensure accuracy.
- The design process often involves advanced software tools like CAD (Computer-Aided Design) and CAE (Computer-Aided Engineering).
-
Components of Mold Tooling
- Cavity and Core: These are the primary components that define the shape of the part. The cavity forms the outer surface, while the core shapes the inner features.
- Cooling System: Designed to regulate the temperature of the mold, ensuring uniform cooling and minimizing defects like warping.
- Ejection System: Mechanisms such as ejector pins or plates that remove the finished part from the mold after cooling.
- Gating System: Channels that direct molten plastic into the mold cavity, including gates, runners, and sprues.
- Venting: Small channels that allow air to escape as the molten plastic fills the mold, preventing air traps and defects.
-
Engineering Considerations
- Material Selection: The mold must be made from materials that can withstand high temperatures, pressure, and wear over time. Common materials include steel and aluminum.
- Dimensional Accuracy: The design must ensure that the final part meets precise dimensional tolerances, accounting for factors like shrinkage and thermal expansion.
- Production Efficiency: The mold design should optimize cycle times, reduce waste, and minimize maintenance requirements.
-
Applications and Importance
- Mold tool design is critical in industries such as automotive, consumer electronics, medical devices, and packaging.
- It enables the mass production of high-quality plastic parts with consistent dimensions and features.
- A well-designed mold reduces production costs, improves product quality, and enhances manufacturing efficiency.
-
Challenges in Mold Tool Design
- Complex Geometries: Designing molds for parts with intricate shapes or undercuts can be challenging.
- Material Behavior: Engineers must account for how different plastics behave during the molding process, including flow characteristics and shrinkage rates.
- Cost Constraints: Balancing the need for precision and durability with budget limitations is a common challenge.
-
Future Trends in Mold Tool Design
- Additive Manufacturing: 3D printing is increasingly used to create prototype molds or even production molds for low-volume runs.
- Smart Molds: Incorporating sensors and IoT (Internet of Things) technology to monitor mold performance in real-time.
- Sustainability: Designing molds that minimize material waste and energy consumption, aligning with environmental goals.
In summary, mold tool design is a critical aspect of plastic part manufacturing, requiring a blend of engineering expertise, advanced tools, and careful consideration of material and production factors. It plays a vital role in ensuring the quality, efficiency, and cost-effectiveness of the manufacturing process.
Summary Table:
Aspect | Details |
---|---|
Definition | Process of creating molds for manufacturing plastic parts. |
Key Components | Cavity & Core, Cooling System, Ejection System, Gating System, Venting. |
Engineering Factors | Material Selection, Dimensional Accuracy, Production Efficiency. |
Applications | Automotive, Consumer Electronics, Medical Devices, Packaging. |
Challenges | Complex Geometries, Material Behavior, Cost Constraints. |
Future Trends | Additive Manufacturing, Smart Molds, Sustainability. |
Need expert mold tool design for your plastic parts? Contact us today for tailored solutions!