A packed bed reactor is a type of reactor where solid particles (often catalysts or other granular materials) are packed into a fixed bed, and a fluid (gas or liquid) flows through the bed. At lower fluid velocities, the solid particles remain stationary, creating a packed bed configuration. This design is widely used in chemical, petrochemical, and environmental engineering for processes like catalytic reactions, adsorption, and filtration. The packed bed reactor offers advantages such as high surface area for reactions, efficient heat and mass transfer, and ease of operation. However, its performance depends on factors like fluid velocity, particle size, and bed porosity.
Key Points Explained:
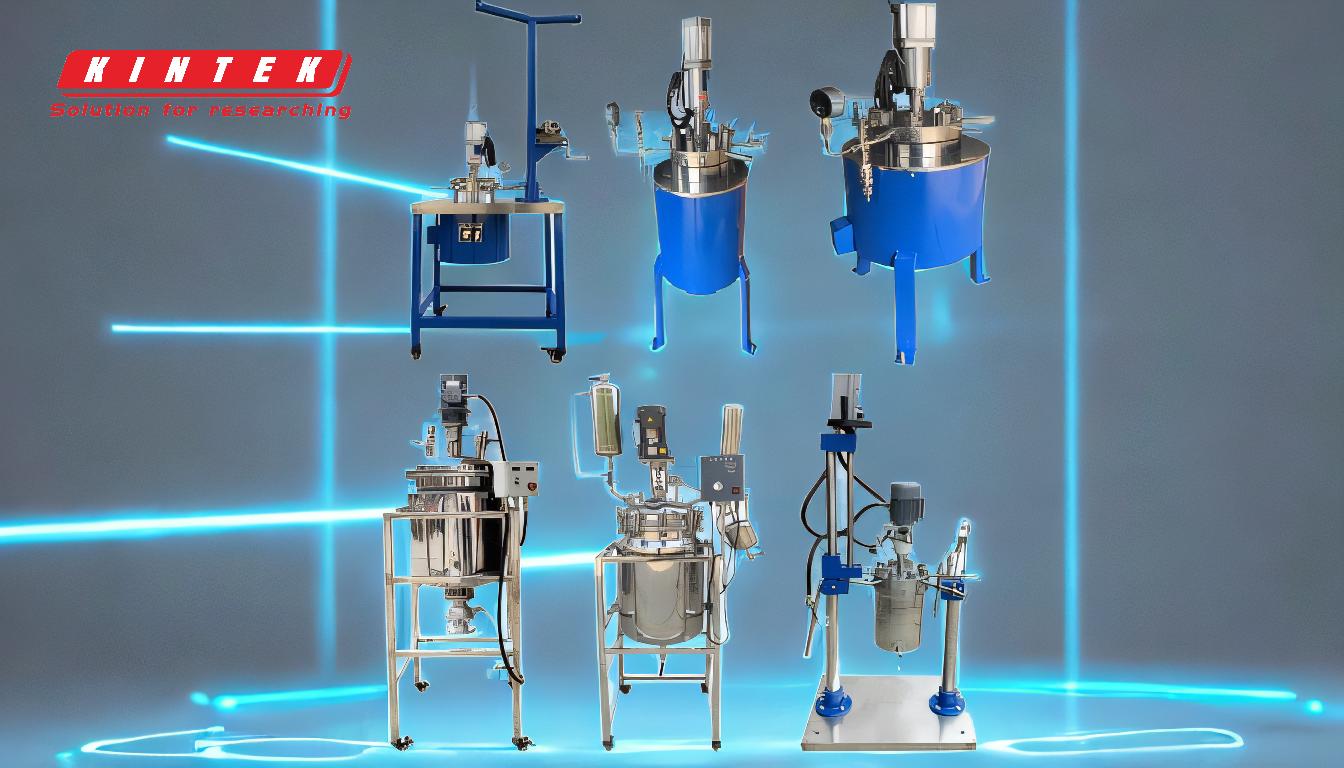
-
Definition and Basic Concept:
- A packed bed reactor consists of a column filled with solid particles (e.g., catalysts or adsorbents) through which a fluid flows.
- The solid particles remain stationary at lower fluid velocities, forming a packed bed.
- This configuration is commonly used in catalytic processes, chemical synthesis, and environmental applications like wastewater treatment.
-
Working Principle:
- The fluid (gas or liquid) flows through the packed bed, interacting with the solid particles.
- In catalytic applications, the solid particles act as catalysts, facilitating chemical reactions as the fluid passes through.
- The reactor operates under conditions where the fluid velocity is low enough to keep the particles stationary, ensuring a stable packed bed.
-
Advantages of Packed Bed Reactors:
- High Surface Area: The large surface area of the packed particles enhances reaction rates and mass transfer.
- Efficient Heat Transfer: Heat generated or required by reactions can be efficiently managed due to the proximity of particles and fluid.
- Scalability: Packed bed reactors are easily scalable from laboratory to industrial applications.
- Cost-Effectiveness: They are relatively simple to construct and operate, making them cost-effective for many processes.
-
Applications:
- Chemical and Petrochemical Industries: Used for catalytic cracking, hydrogenation, and other chemical reactions.
- Environmental Engineering: Applied in wastewater treatment, air purification, and adsorption of pollutants.
- Biotechnology: Utilized in bioreactors for enzyme immobilization and fermentation processes.
-
Factors Affecting Performance:
- Fluid Velocity: Higher velocities can lead to fluidization, transitioning the reactor to a fluidized bed configuration.
- Particle Size and Shape: Smaller particles increase surface area but may cause higher pressure drops.
- Bed Porosity: The void fraction in the bed affects fluid flow and reaction efficiency.
- Temperature and Pressure: These parameters influence reaction kinetics and equilibrium.
-
Comparison with Fluidized Bed Reactors:
- In a packed bed reactor, the solid particles remain stationary, while in a fluidized bed reactor, the particles are suspended by the fluid.
- Packed beds are preferred for processes requiring fixed catalysts, while fluidized beds are used for processes needing intense mixing and heat transfer.
-
Challenges and Limitations:
- Pressure Drop: High fluid flow rates can cause significant pressure drops across the bed.
- Channeling: Uneven fluid flow can lead to inefficient use of the catalyst.
- Fouling: Accumulation of deposits on the particles can reduce reactor efficiency over time.
-
Design Considerations:
- Bed Height and Diameter: These dimensions are optimized based on the required reaction kinetics and fluid dynamics.
- Distributor Plate: Ensures uniform fluid distribution across the bed.
- Material Selection: The choice of particles and reactor materials depends on the chemical and thermal properties of the process.
By understanding these key points, one can appreciate the versatility and importance of packed bed reactors in various industrial and environmental applications. Their design and operation require careful consideration of multiple factors to ensure optimal performance and efficiency.
Summary Table:
Aspect | Details |
---|---|
Definition | A reactor with solid particles packed in a fixed bed, through which fluid flows. |
Working Principle | Fluid flows through stationary solid particles, enabling catalytic reactions. |
Advantages | High surface area, efficient heat transfer, scalability, cost-effectiveness. |
Applications | Catalytic reactions, wastewater treatment, air purification, biotechnology. |
Performance Factors | Fluid velocity, particle size, bed porosity, temperature, and pressure. |
Challenges | Pressure drop, channeling, fouling. |
Design Considerations | Bed height, diameter, distributor plate, material selection. |
Optimize your processes with a packed bed reactor—contact our experts today for tailored solutions!