Physical sputtering is a process where ions of an inert gas, such as argon or xenon, are accelerated into a target material within a vacuum chamber. The bombardment of these ions transfers energy to the target, causing atoms or molecules near the surface to escape. These ejected particles, typically in neutral form, travel through the vacuum and deposit onto a substrate, forming a thin film. This process is widely used in industries for creating precise coatings with specific properties like reflectivity, electrical resistivity, or ionic resistivity. It is a vacuum-enabled technique that allows for precise control over film characteristics such as morphology, grain orientation, grain size, and density.
Key Points Explained:
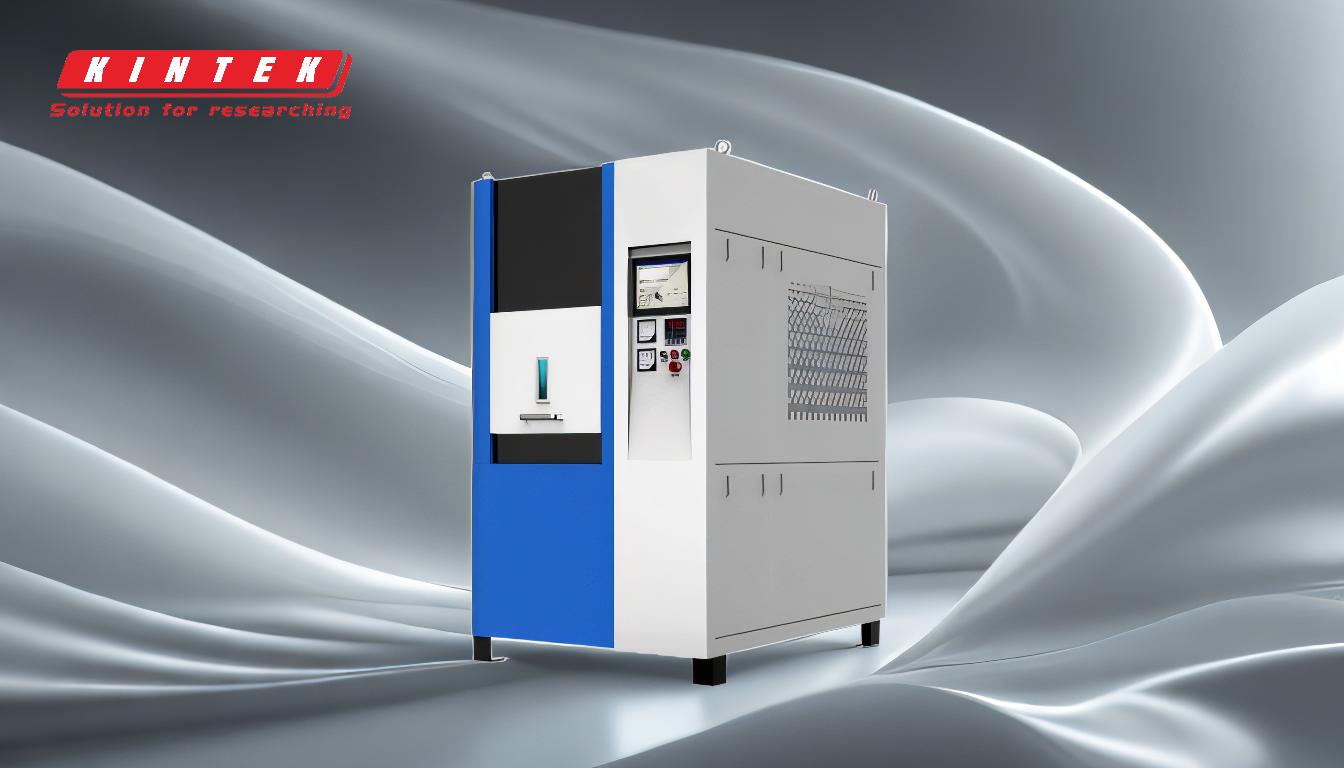
-
Definition of Physical Sputtering:
- Physical sputtering is a process where ions of inert gases (e.g., argon, xenon) are accelerated into a target material, causing atoms or molecules from the target's surface to be ejected due to energy transfer.
- These ejected particles are typically neutral and travel through a vacuum to deposit onto a substrate, forming a thin film.
-
Vacuum Environment:
- The process occurs in a vacuum chamber to ensure that the ejected particles can travel without interference from air molecules.
- The vacuum environment is crucial for maintaining the purity and integrity of the thin film being deposited.
-
Role of Inert Gases:
- Inert gases like argon or xenon are used because they do not react chemically with the target material or the substrate.
- These gases are ionized to create a plasma, which is essential for the sputtering process.
-
Energy Transfer and Ejection:
- The ions from the inert gas are accelerated by an electric field and bombard the target material.
- Upon impact, energy is transferred to the target atoms, providing them with enough energy to escape from the surface.
-
Deposition onto Substrate:
- The ejected particles travel through the vacuum and deposit onto a substrate, such as silicon, glass, or molded plastics.
- The particles nucleate and form a thin film with specific properties, such as reflectivity, electrical resistivity, or ionic resistivity.
-
Control Over Film Properties:
- The sputtering process allows for precise control over the morphology, grain orientation, grain size, and density of the deposited film.
- This precision is essential for applications requiring specific material properties.
-
Applications of Physical Sputtering:
- Physical sputtering is used in various industries for creating thin films with precise characteristics.
- Applications include the production of reflective coatings, semiconductor devices, and other precision products.
-
Advantages of Physical Sputtering:
- The process is highly accurate and can produce uniform thin films with controlled properties.
- It is versatile and can be used with a wide range of target materials and substrates.
-
Challenges and Considerations:
- The process requires a high vacuum environment, which can be costly and complex to maintain.
- The choice of inert gas and target material can significantly impact the efficiency and outcome of the sputtering process.
By understanding these key points, one can appreciate the complexity and precision involved in physical sputtering, making it a valuable technique in modern material science and manufacturing.
Summary Table:
Key Aspect | Description |
---|---|
Definition | Ions of inert gases bombard a target, ejecting particles to form a thin film. |
Vacuum Environment | Ensures particle travel without interference, maintaining film purity. |
Role of Inert Gases | Non-reactive gases like argon or xenon ionize to create plasma for sputtering. |
Energy Transfer | Ions transfer energy to target atoms, causing them to escape the surface. |
Deposition onto Substrate | Ejected particles deposit onto substrates like silicon or glass, forming films. |
Control Over Film Properties | Precise control over morphology, grain size, and density of the film. |
Applications | Used in reflective coatings, semiconductors, and precision product manufacturing. |
Advantages | High accuracy, uniform films, and versatility with materials and substrates. |
Challenges | Requires costly high vacuum environments and careful selection of materials. |
Discover how physical sputtering can enhance your manufacturing process—contact our experts today!