Sputtering is a versatile and widely used manufacturing process in which atoms are ejected from a solid target material due to bombardment by energetic ions, typically from a plasma. These ejected atoms then deposit onto a substrate, forming a thin film. This process is a type of physical vapor deposition (PVD) and is valued for its ability to create uniform, high-quality coatings on a variety of materials, including heat-sensitive and complex three-dimensional surfaces. Sputtering is essential in industries such as semiconductors, aerospace, optoelectronics, and decorative coatings, enabling the production of advanced materials and devices with precise properties.
Key Points Explained:
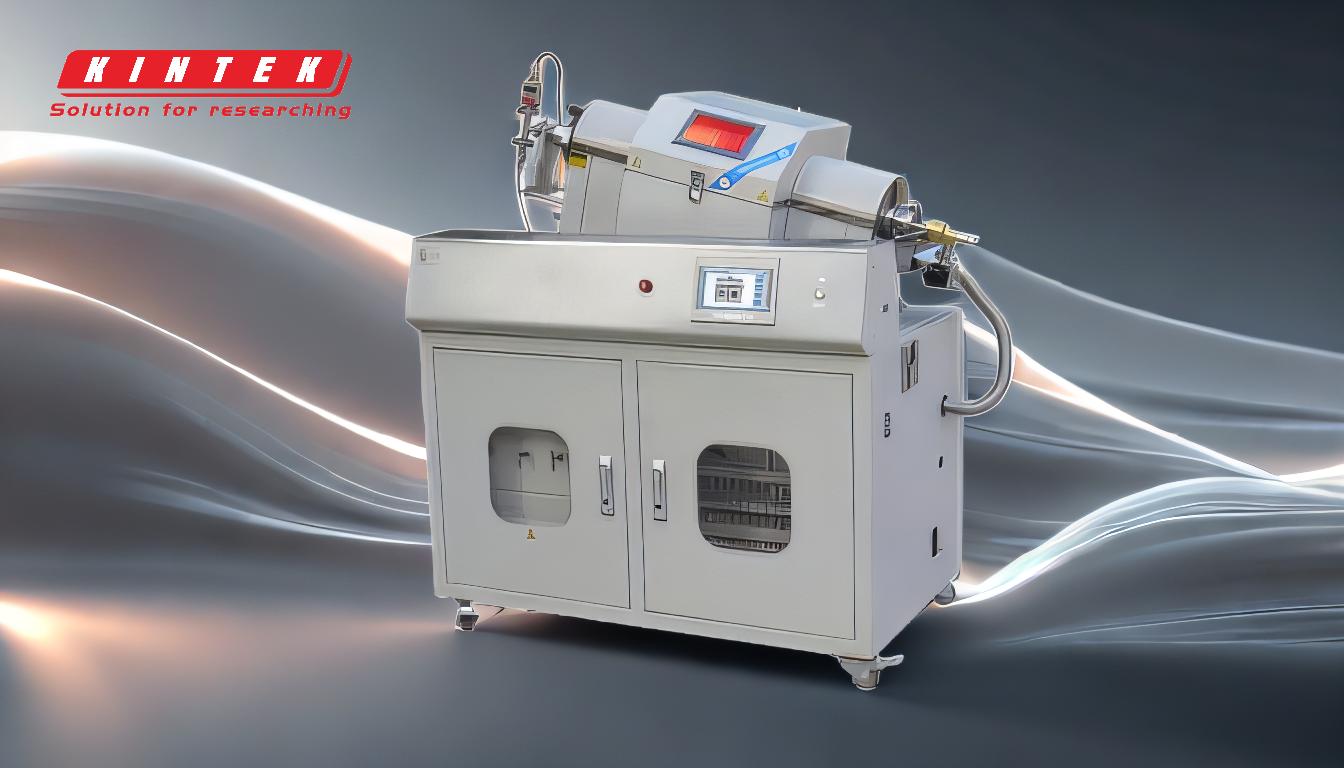
-
What is Sputtering?
- Sputtering is a physical vapor deposition (PVD) process where atoms are ejected from a solid target material when bombarded by energetic ions from a plasma. These ejected atoms travel through a vacuum chamber and deposit onto a substrate, forming a thin film.
- It is a "line of sight" process, meaning the target material and substrate must be positioned appropriately for effective coating.
-
How Sputtering Works
- A plasma is used to generate ions, typically from an inert gas like argon, which are accelerated toward the target material.
- When the ions collide with the target, they dislodge atoms from its surface if the ion energy is sufficient (typically 4 times the bond energy of the target material, around 5 eV).
- The sputtered atoms then travel through the vacuum chamber and deposit onto the substrate, forming a thin film.
-
Applications of Sputtering
- Semiconductor Industry: Sputtering is used to deposit thin films for creating electronic devices, such as transistors and integrated circuits.
- Aerospace and Defense: It is used to apply specialized coatings, such as gadolinium films for neutron radiography.
- Optoelectronics: Sputtering is employed to create transparent conductive coatings for displays and solar cells.
- Decorative Coatings: It is used to apply durable and aesthetically pleasing finishes on consumer products.
- Corrosion Protection: Sputtering can create gas-impermeable films to protect materials prone to corrosion.
- Medical Devices: It is used to produce dielectric stacks for electrically isolating surgical tools.
-
Advantages of Sputtering
- Versatility: Sputtering can deposit a wide range of materials, including metals, alloys, and insulators.
- Uniform Coatings: It produces highly uniform and dense thin films, even on complex three-dimensional surfaces.
- Low Temperature: The process is suitable for heat-sensitive materials, such as biological samples, as the sputtered atoms have very low temperatures.
- High Melting Point Materials: Sputtering is effective for materials with extremely high melting points, such as carbon and silicon.
-
Challenges and Considerations
- Vacuum Requirements: Sputtering requires a controlled vacuum environment, which can be costly and complex to maintain.
- Line of Sight Limitation: The process is limited by the need for a direct line of sight between the target and substrate.
- Insulating Materials: Insulating targets require an RF energy source, which adds complexity to the process.
-
Historical and Modern Significance
- Sputtering has been used since the early 1800s and remains a mature and reliable method for thin film deposition.
- It plays a critical role in modern manufacturing, enabling the production of advanced materials and devices, such as high-quality reflective coatings for mirrors, semiconductor computing devices, and packaging materials like potato chip bags.
In summary, sputtering is a foundational technology in modern manufacturing, offering precise and versatile thin film deposition for a wide range of applications. Its ability to handle complex geometries, heat-sensitive materials, and high-performance coatings makes it indispensable in industries ranging from electronics to aerospace and beyond.
Summary Table:
Aspect | Details |
---|---|
Definition | Physical vapor deposition (PVD) process ejecting atoms from a target material. |
Process | Plasma-generated ions bombard the target, ejecting atoms onto a substrate. |
Applications | Semiconductors, aerospace, optoelectronics, decorative coatings, and more. |
Advantages | Versatile, uniform coatings, low temperature, high melting point materials. |
Challenges | Requires vacuum, line of sight limitation, complexity with insulators. |
Discover how sputtering can revolutionize your manufacturing process—contact our experts today!