Sputtering is a physical vapor deposition (PVD) technique widely used in the semiconductor industry to deposit thin films of materials onto substrates. It involves bombarding a target material with high-energy ions, typically from an inert gas like argon, in a vacuum environment. This bombardment causes atoms or molecules from the target to be ejected and then deposited onto a substrate, forming a thin film. Sputtering is highly precise and is used to create ultra-high-purity coatings for semiconductor devices, optical coatings, and other precision applications. The process is performed under vacuum conditions to ensure controlled deposition and prevent contamination.
Key Points Explained:
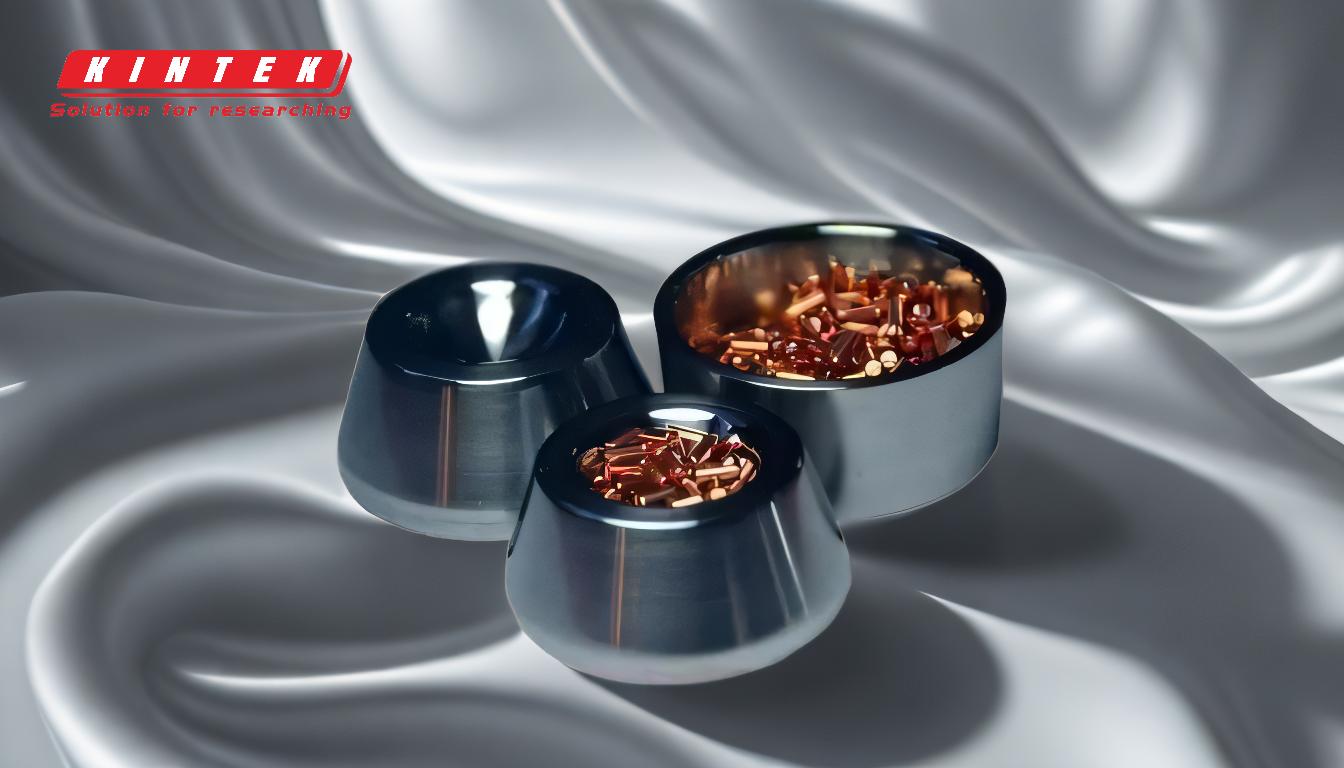
-
Definition of Sputtering
- Sputtering is a physical process where high-energy particles (ions or neutral atoms/molecules) bombard the surface of a solid target material.
- The energy transfer from the bombarding particles causes atoms or molecules near the target's surface to gain enough energy to escape and be ejected.
- This process is performed under vacuum conditions to ensure precision and prevent contamination.
-
Mechanism of Sputtering
- A target material (e.g., a metal or oxide) is placed in a vacuum chamber along with a substrate.
- The chamber is evacuated and then backfilled with a process gas, typically an inert gas like argon.
- A voltage is applied, creating a plasma of ionized gas atoms.
- Positively charged ions from the plasma are accelerated toward the negatively charged target (cathode), causing target atoms to be ejected.
- The ejected atoms travel through the vacuum and deposit onto the substrate, forming a thin film.
-
Key Components of the Sputtering Process
- Target Material: The source material to be deposited (e.g., metals, oxides, or alloys).
- Substrate: The surface onto which the thin film is deposited (e.g., silicon wafers, glass, or other materials).
- Process Gas: Typically an inert gas like argon, which is ionized to create the plasma.
- Vacuum Chamber: Ensures a controlled environment free from contaminants and allows precise deposition.
- Magnetron: A device that generates a magnetic field to enhance the sputtering process by trapping electrons and increasing ionization efficiency.
-
Applications in Semiconductors
- Sputtering is used to deposit thin films of conductive, insulating, or semiconducting materials onto semiconductor wafers.
- Common applications include:
- Metallization for interconnects (e.g., aluminum, copper).
- Deposition of dielectric layers (e.g., silicon dioxide, silicon nitride).
- Creation of barrier layers (e.g., tantalum, titanium nitride) to prevent diffusion between materials.
-
Advantages of Sputtering
- High Precision: Allows for the deposition of ultra-thin, uniform films with precise control over thickness and composition.
- Versatility: Can deposit a wide range of materials, including metals, alloys, oxides, and nitrides.
- High Purity: Produces films with minimal contamination due to the vacuum environment.
- Scalability: Suitable for both small-scale research and large-scale industrial production.
-
Types of Sputtering
- DC Sputtering: Uses a direct current (DC) power supply to generate the plasma. Commonly used for conductive materials.
- RF Sputtering: Uses radio frequency (RF) power to ionize the gas. Suitable for insulating materials.
- Magnetron Sputtering: Enhances the sputtering rate and efficiency by using a magnetic field to trap electrons near the target surface.
- Reactive Sputtering: Involves introducing a reactive gas (e.g., oxygen or nitrogen) to deposit compound films like oxides or nitrides.
-
Challenges and Considerations
- Target Erosion: The target material erodes over time, requiring periodic replacement.
- Uniformity: Achieving uniform deposition across large substrates can be challenging.
- Cost: High vacuum equipment and target materials can be expensive.
- Contamination: Even trace impurities can affect film quality, necessitating strict control over the vacuum environment.
-
Comparison with Other Deposition Techniques
- Sputtering vs. Evaporation: Sputtering provides better adhesion and uniformity, especially for complex geometries, while evaporation is faster and simpler for certain materials.
- Sputtering vs. Chemical Vapor Deposition (CVD): Sputtering is a physical process, whereas CVD involves chemical reactions. Sputtering is often preferred for lower-temperature processes and simpler material systems.
By understanding these key points, semiconductor manufacturers and equipment purchasers can better evaluate the suitability of sputtering for their specific applications, ensuring optimal performance and cost-effectiveness.
Summary Table:
Key Aspect | Details |
---|---|
Definition | A physical process where high-energy ions bombard a target to eject atoms. |
Mechanism | Uses a vacuum chamber, inert gas (e.g., argon), and plasma to deposit films. |
Key Components | Target material, substrate, process gas, vacuum chamber, magnetron. |
Applications | Semiconductor metallization, dielectric layers, barrier layers. |
Advantages | High precision, versatility, high purity, scalability. |
Types | DC, RF, magnetron, and reactive sputtering. |
Challenges | Target erosion, uniformity, cost, contamination control. |
Comparison | Better adhesion than evaporation; lower temperature than CVD. |
Discover how sputtering can enhance your semiconductor processes—contact our experts today!