DC sputtering is a versatile and widely used technique in various industries, primarily for depositing thin films on substrates. Its applications range from semiconductor manufacturing to decorative coatings, optical components, and energy-efficient materials. The process involves using kinetic energy to dislodge atoms from a target material, which then form a thin film on a substrate in a vacuum environment. This method is valued for its precision, uniformity, and ability to deposit a wide range of materials, making it indispensable in industries such as electronics, optics, aerospace, and medical devices.
Key Points Explained:
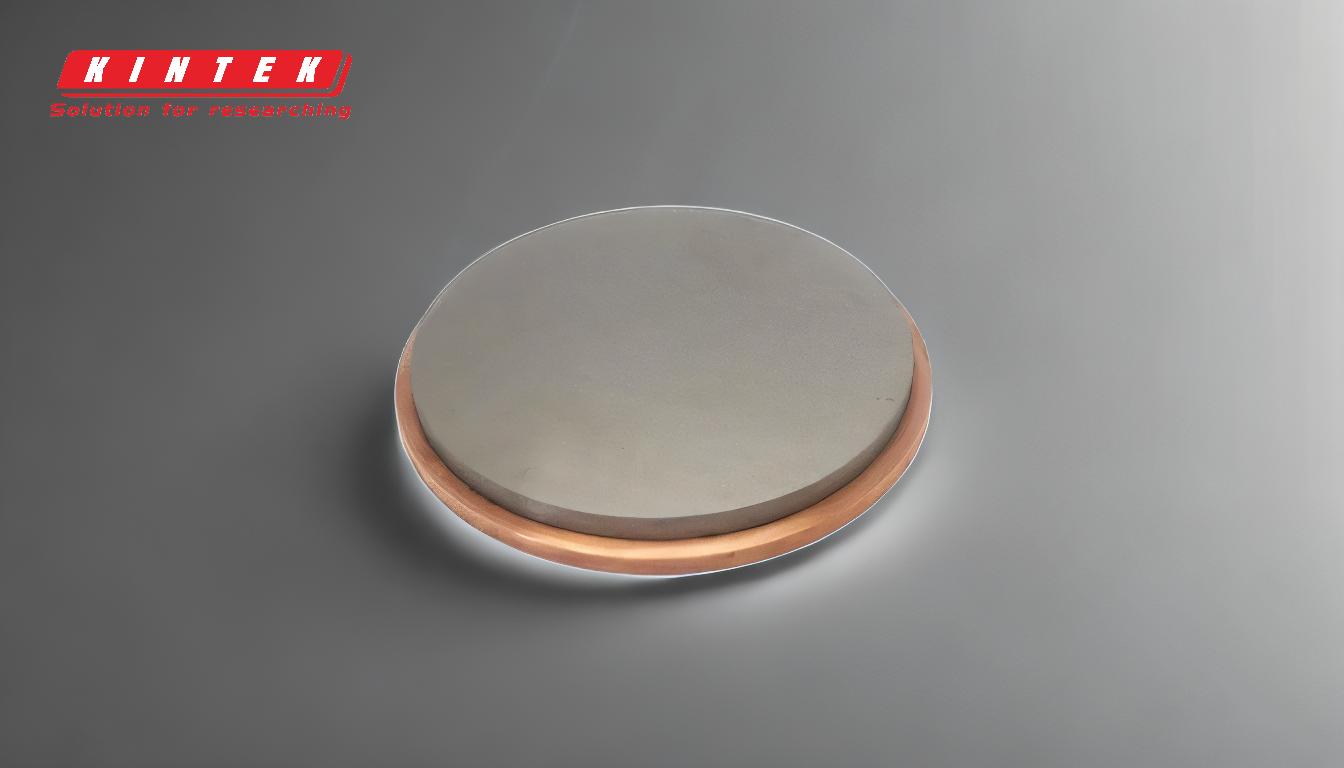
-
Semiconductor Industry
- DC sputtering is extensively used in the semiconductor industry to deposit thin films of various materials during integrated circuit (IC) fabrication.
- It plays a critical role in creating microchip circuitry at the molecular level, ensuring precise and uniform coatings essential for the performance of electronic devices.
- Materials like molybdenum, tantalum, and niobium are commonly deposited using DC sputtering to enhance the properties of semiconductor components.
-
Optical Coatings
- DC sputtering is used to deposit anti-reflective coatings on glass and optical components, such as lenses for binoculars, telescopes, and night-vision equipment.
- These coatings improve light transmission and reduce glare, making them essential for high-performance optical systems.
- Low-emissivity (Low-E) coatings on double-pane windows, which improve energy efficiency, are also produced using this technique.
-
Decorative and Functional Coatings
- DC sputtering is employed to create decorative finishes, such as gold sputter coatings on jewelry, watches, and architectural glass.
- It is also used for functional coatings, such as scratch-resistant layers on nickel-titanium shape memory alloys, enhancing their durability and performance.
-
Energy Applications
- In the energy sector, DC sputtering is used to deposit thin films for solar panels, improving their efficiency and durability.
- It is also applied in coating gas turbine blades, which require high-performance materials to withstand extreme conditions.
-
Consumer Electronics
- DC sputtering is integral to the production of CDs, DVDs, and hard disks, where it is used to deposit metal layers during manufacturing.
- It is also used in the production of LED displays and other electronic components, ensuring high-quality, uniform coatings.
-
Medical and Scientific Applications
- In the medical field, DC sputtering is used to coat medical devices and implants, enhancing their biocompatibility and performance.
- Researchers use sputtering to develop advanced materials and coatings for scientific applications, such as nanotechnology and analytical techniques.
-
Industrial and Decorative Uses
- DC sputtering is applied in industries like aerospace, automotive, and defense for coating components that require high durability and performance.
- It is also used for decorative purposes, such as metalizing plastics and creating finishes for toys and hardware.
-
Advantages of DC Sputtering
- The process allows for precise control over film thickness and uniformity, making it suitable for high-precision applications.
- It can deposit a wide range of materials, including metals, alloys, and ceramics, on various substrates.
- The technique operates at relatively low temperatures, making it suitable for heat-sensitive materials.
-
Technological Innovations
- DC magnetron sputtering, a variant of DC sputtering, is widely used for its ability to produce high-density, low-roughness films with excellent adhesion.
- Innovations in sputtering technology continue to drive advancements in materials science, enabling the development of smaller, lighter, and more durable products.
-
Future Prospects
- As industries demand more advanced materials and coatings, DC sputtering is expected to play an increasingly important role in areas like renewable energy, nanotechnology, and biomedical engineering.
- Ongoing research aims to optimize the process further, reducing costs and expanding its applications.
In summary, DC sputtering is a foundational technology with diverse applications across multiple industries. Its ability to deposit thin films with precision and uniformity makes it indispensable for modern manufacturing and research, driving innovation in fields ranging from electronics to energy and medicine.
Summary Table:
Industry | Applications |
---|---|
Semiconductor | Integrated circuit fabrication, precise coatings for microchip circuitry |
Optical Coatings | Anti-reflective coatings, Low-E glass for energy efficiency |
Decorative Coatings | Gold sputter coatings on jewelry, scratch-resistant layers on alloys |
Energy Applications | Thin films for solar panels, coatings for gas turbine blades |
Consumer Electronics | CDs, DVDs, hard disks, LED displays |
Medical Applications | Biocompatible coatings for implants, advanced materials for nanotechnology |
Industrial Uses | Aerospace, automotive, and defense coatings, decorative metalizing |
Advantages | Precise control, uniform deposition, low-temperature operation |
Discover how DC sputtering can revolutionize your industry—contact our experts today!