Ball milling is a mechanical process used to grind, mix, and blend materials into fine powders or nanoparticles. It involves the use of a rotating cylindrical chamber filled with grinding media (usually balls) and the material to be processed. The process relies on the impact and friction generated by the balls to break down the material into smaller particles. Ball milling can lead to various outcomes, such as flattening and welding of powder particles, formation of layered structures, deformation of these structures, and ultimately the creation of nanoparticles. This technique is widely used in materials science, chemistry, and engineering for synthesizing and refining materials.
Key Points Explained:
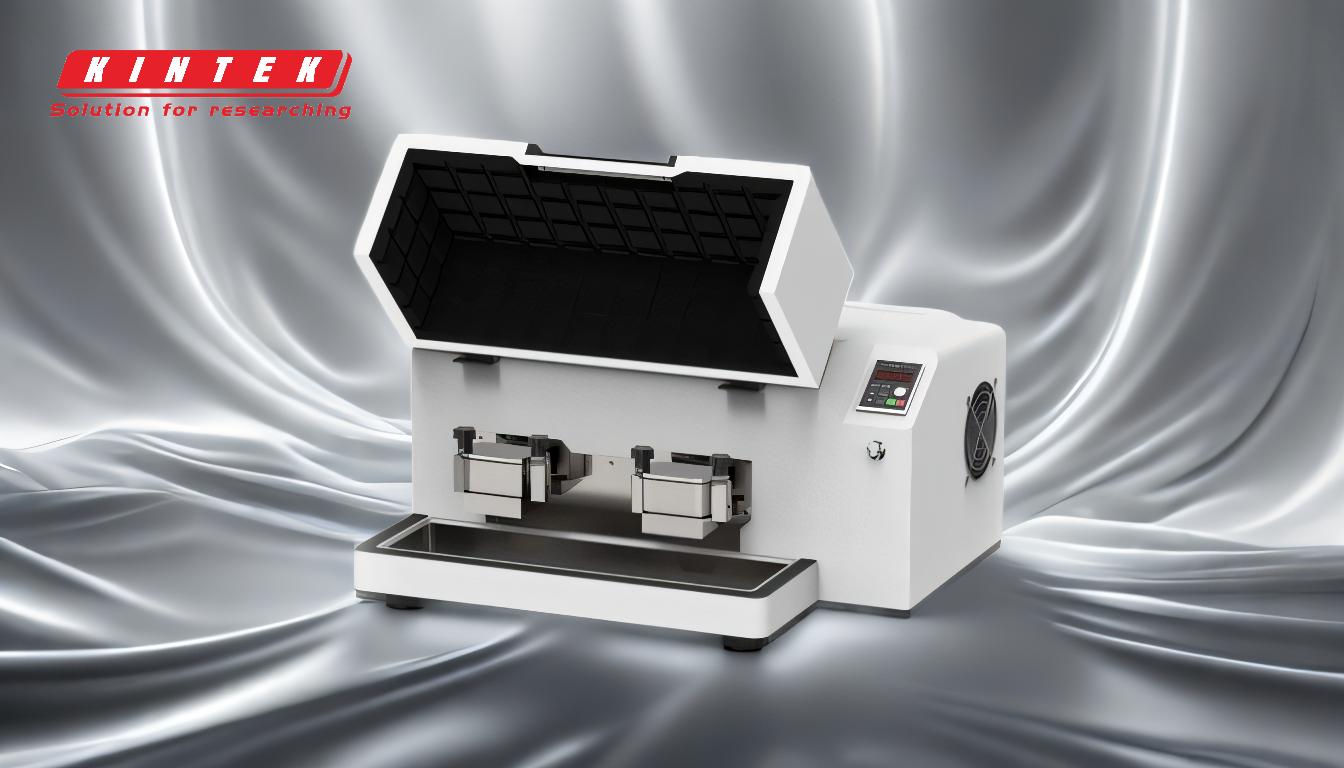
-
Mechanism of Ball Milling:
- Ball milling operates on the principle of impact and attrition. The grinding media (balls) collide with the material, breaking it down into smaller particles through repeated impacts.
- The process involves both high-energy collisions (impact) and the grinding action between the balls and the material (attrition).
-
Processes Involved in Ball Milling:
- Flattening of Powder Particles: The repeated impacts cause the particles to flatten, reducing their size and altering their shape.
- Welding of Powder Particles: Under certain conditions, the particles may weld together due to the mechanical energy imparted by the collisions.
- Formation of Layered Structures: The process can lead to the creation of layered or composite structures as particles are repeatedly deformed and compacted.
- Deformation of Layered Structures: Continued milling can further deform these layered structures, leading to changes in their mechanical and physical properties.
- Formation of Nanoparticles: Prolonged milling can reduce particle sizes to the nanoscale, producing nanoparticles with unique properties.
-
Applications of Ball Milling:
- Materials Synthesis: Ball milling is used to synthesize a variety of materials, including metals, ceramics, and composites.
- Mechanical Alloying: This process involves the repeated welding and fracturing of powder particles to create alloys with uniform microstructures.
- Nanoparticle Production: Ball milling is an effective method for producing nanoparticles, which have applications in catalysis, electronics, and medicine.
- Powder Refinement: The process is used to refine and homogenize powders, improving their properties for further processing or use.
-
Factors Influencing Ball Milling:
- Milling Time: The duration of milling affects the degree of particle size reduction and the formation of new phases or structures.
- Ball Size and Material: The size and material of the grinding balls influence the energy transfer and the efficiency of the milling process.
- Rotational Speed: The speed at which the mill rotates determines the intensity of the impacts and the overall energy input.
- Atmosphere: The environment inside the milling chamber (e.g., inert gas, vacuum) can affect the chemical reactions and phase transformations during milling.
-
Advantages of Ball Milling:
- Versatility: Ball milling can be used for a wide range of materials and applications.
- Scalability: The process can be scaled up for industrial production or down for laboratory research.
- Cost-Effectiveness: Ball milling is relatively inexpensive compared to other methods of particle size reduction and material synthesis.
-
Challenges and Limitations:
- Contamination: The grinding media and milling chamber can introduce impurities into the material.
- Heat Generation: The process can generate significant heat, which may affect the properties of the material being milled.
- Control of Particle Size: Achieving a uniform particle size distribution can be challenging, especially for nanoparticles.
In summary, ball milling is a versatile and effective technique for processing materials, with applications ranging from powder refinement to nanoparticle synthesis. Understanding the basic principles and factors influencing the process is essential for optimizing its use in various fields.
Summary Table:
Aspect | Details |
---|---|
Mechanism | Impact and attrition through grinding media (balls). |
Key Processes | Flattening, welding, layered structure formation, nanoparticle production. |
Applications | Materials synthesis, mechanical alloying, nanoparticle production. |
Influencing Factors | Milling time, ball size/material, rotational speed, atmosphere. |
Advantages | Versatile, scalable, cost-effective. |
Challenges | Contamination, heat generation, particle size control. |
Ready to optimize your material processing? Contact us today for expert guidance on ball milling solutions!